You have reached your limit of 3 free stories. A story preview is shown instead.
To view more stories
To view more stories
SUBSCRIBE OR RENEW NOW
(If your subscription is current, click here to Login or Register.)2013 - Volume #37, Issue #1, Page #4
[ Sample Stories From This Issue | List of All Stories In This Issue]
Self-Loading Bale Unroller
Gordon Edgar’s loader-mounted, bale unroller does it all. The lift arm spears a big bale, lifts it into position and holds it in place to be unrolled. The unroller itself slides left and right and can unroll to either side.“We have around 200 goats and milk about 130. Feeding and bedding them takes a lot of..........
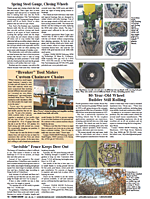
You must sign in, subscribe or renew to see the page.
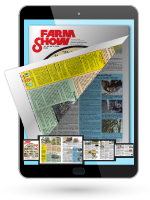
You must sign in, subscribe or renew to see the flip-book
Self-Loading Bale Unroller BALE HANDLING Gordon Edgar’s loader-mounted bale unroller does it all The lift arm spears a big bale lifts it into position and holds it in place to be unrolled The unroller itself slides left and right and can unroll to either side “We have around 200 goats and milk about 130 Feeding and bedding them takes a lot of work ” says Edgar “We use haylage bales for feed and tried just putting them in feeders but the goats couldn’t reach all of the hay We had to stand the bales on end and pull the hay off with a fork ” When the Edgars added cheese-making to their operation time became even more precious He started looking for a better way to handle bales Using the apron chain and sprockets from an old forage wagon Edgar built an unloading platform that slides back and forth on a subframe The subframe has quick-attach couplers so it can be used on a front-end loader The platform has a frame of 2-in square tubing with 1 by 1-in square tubing as cross pieces Cherry boards attached to the crosspieces form the floor of the platform Metal side panels help to hold the bale in place and direct the haylage or bedding to either side A chain drive on an orbital motor powers the apron chain to the left or the right as desired The subframe is built out of 3-in square tubing A hydraulic cylinder slides the platform a foot to the left or right Edgar uses this function when unrolling hay into a feeder or unrolling bedding material “We can pull alongside gates raise the loader and move the platform to extend over the gate so it drops the bedding into the pens as we drive by ” says Edgar The platform cylinder is mounted to the subframe and attaches to the reinforced rear/right corner of the platform This corner also serves as the base for the spear-arm support post The spear-arm post and arm is also fabricated from 3-in square tubing It has an 8-in and a 16-in cylinder mounted to a yoke allowing the spear-arm to travel more than 180° The yoke composed of two 4-in wide by 1/2-in thick steel plates pivots on the upright post mounted to the platform The arm cylinders connect to pins that pivot at either end of the yoke plates The arm is pinned to the post at the center of the yoke The two cylinders are hooked in series so when one has extended fully or retracted fully the other goes into action The 8-in stroke cylinder rides against the outside of the post It extends from one pin to the platform frame As it retracts it lifts the spear-arm from its rest position on the platform to a near vertical position At that point a 16-in cylinder mounted from the opposite pin on the yoke kicks in moving the arm around and into a bale spearing position It is the yoke and the position of the shorter cylinder that ensures the 16-in cylinder doesn t go over center on the post Getting the positioning of the two cylinders and the post was the biggest challenge says Edgar I made a model using plywood to get the reach and positioning right before cutting it out of steel The first steel I used was too light and it bent the first time I tried to pick up a bale With stronger steel it has worked fine Where possible he ran hydraulic lines through the steel tubing to protect it from wear Controlling the various cylinders and the orbital motor required a fairly complex set of control valves Hydraulic power comes from the auxiliary power line that normally controls the grapple on his loader bucket He runs it to a 3-way valve A switch mounted to the joystick sends flow to the orbital motor with the joystick controlling whether the apron unloads left or right explains Edgar When I activate a second switch mounted on the loader post the flow moves from the motor to the cylinder on the bed and the joystick moves the bed left or right When the third switch is activated the flow moves to the loader arm Again the joystick controls moving the arm left or right To simplify connecting and disconnecting the valves that are mounted on the unroller Edgar ran the electric control functions through a common 110 outlet and plug When disconnecting the loader for other uses he simply pulls the plug and disconnects the auxiliary hydraulic hose Since building the unroller in 2007 I ve used it twice a day every day says Edgar It sure saves a lot of work Contact: FARM SHOW Followup Gordon’s Goat Dairy 43253 C-Line Rd Wroxeter Ont Canada N0G 2X0 ph 519 335-4321; gordonsgoatdairy@gmail com; www gordonsgoatdairy ca
To read the rest of this story, download this issue below or click here to register with your account number.