You have reached your limit of 3 free stories. A story preview is shown instead.
To view more stories
To view more stories
SUBSCRIBE OR RENEW NOW
(If your subscription is current, click here to Login or Register.)2012 - Volume #36, Issue #6, Page #35
[ Sample Stories From This Issue | List of All Stories In This Issue]
Cob Burner Heats Their Big Shop And Home
“We talked to commercial contractors who told us we needed a system that would produce more than a million btu’s for our shop and cost $40,000 to $50,000 to install,” says Dan Hall of Butterfield, Minn. “We decided that was way too much money so we bought a used boiler for a tenth of that and built our own system that ..........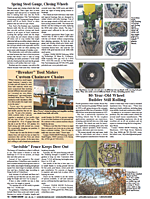
You must sign in, subscribe or renew to see the page.
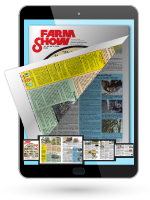
You must sign in, subscribe or renew to see the flip-book
Cob Burner Heats Their Big Shop And Home ENERGY Alternative Fuels “We talked to commercial contractors who told us we needed a system that would produce more than a million btu’s for our shop and cost $40 000 to $50 000 to install ” says Dan Hall of Butterfield Minn “We decided that was way too much money so we bought a used boiler for a tenth of that and built our own system that burns corn cobs Our son Mike said if it works we’re way ahead and if it doesn’t we’ll try something else Turns out it works great and heats both our new 12 000 sq ft shop and 1 500 sq ft temporary living quarters ” The Hall’s boiler is housed in a 24 by 42-ft insulated building that for safety purposes is located 50 ft away from the main shop The boiler which is 4 ft wide 6 ft tall and 10 ft long produces about 400 000 btu’s The Halls use an old grain elevator to convey cobs into the boiler which is thermostatically-controlled to turn off when it reaches 180 degrees “The cobs provide real uniform heat ” says Dan “The system is real easy to maintain The boiler heats water that’s piped into floor tubing spaced every 12 in underneath the concrete shop floor We have auxiliary forced air radiators to use in very cold weather but they’re hardly ever on The shop has 16-ft insulated sidewalls an insulated roof and about 3 000 sq ft of 2nd floor storage About 1 600 sq ft of space on the one end of the building is roughed in for living quarters ” Their home-built furnace burns corn cobs that Dan collects from area farmers He gathers the cobs with a self-propelled cob harvesting machine built from a Gleaner Combine The Halls were not yet ready to disclose details on their cob collector Last year he collected about 400 tons to use for heating He ran the cobs through an old rotary screener and sifted out a couple hundred bushels of small cobs and cracked corn that was used for feed “I’ve used the harvester for several years and it does a great job ” says Dan “With my tractor fuel equipment cost and labor for collecting cobs I figure the heating cost with this system is about 50% less than an LP boiler ” The Hall family which includes Dan Terese and their now adult sons Jeremy Andy Tony and Mike has always been an enterprising group When the boys were young they tinkered with welding projects and helped Dan build a multi-use fencing machine from a self-propelled combine The boys also tuned and rebuilt lawnmowers car motors and snowmobiles The oldest son Jeremy is now a welding instructor at a western Minnesota community college Andy Tony and Mike have welding repair rebuilding and performance machining businesses that operate from the farm site Dan and Terese operate a custom fencing business and raise grass-fed beef and poultry Six years ago while Dan and Terese were attending Farmfest 60 miles away in Morton Minn a huge tornado churned through the Hall farm site demolishing buildings trees machinery equipment and killing livestock “The days and weeks and months after that were incredibly stressful ” says Terese “but we had help from hundreds of people We rebuilt little by little and we’re getting closer to where we want to be ” The basement of their home where Andy Tony and Mike huddled beneath the steps as the tornado tore the house away above them is still intact Today that basement is capped with a well-insulated metal building where Dan Terese Andy and Tony live in cramped but very manageable quarters “I’m glad the side walls are 12 ft tall ” Terese says with a smile “because we at least have a place to stack and hang things ” It’s close living quarters neatly kept with a makeshift kitchen an office a flat screen TV and heat provided by the homebuilt cob burner Eventually they’ll move into the two-story living quarters adjacent to the shop which the boys have vowed will have an electric elevator to reach the second floor Dan says with a laugh “I guess they intend to keep us around even if we can’t get around ” About 3/4ths of that 204-ft long building houses Andy’s welding shop Mike’s machine shop and Tony’s performance machining business Terese has freezers for frozen packages of grass fed beef and poultry Outside the main building equipment in various stages of repair awaits a spot in their sons’ busy work schedule Numerous riding lawnmowers set up for racing attest to at least a few hours of leisure in their days In the past few years Dan and Terese replaced the destroyed wooden farm barns with hoop buildings to house their livestock and machinery and now their attention is on finishing those new living quarters “Dan doesn’t claim to be much of a carpenter ” says Terese “so it looks like I might end up hiring someone to finish our new house At least with the cob-burning boiler we’ll always be warm ” Contact: FARM SHOW Followup Dan and Terese Hall 40133 620th Ave Butterfield Minn 56120 ph 507-956-2657; tereseH77@gmail com
To read the rest of this story, download this issue below or click here to register with your account number.