Van Converted To Old-Style Woodie
A junked-out 1984 commercial van provided the chassis Roy Visser needed to create a 1940’s-style “Woodie”. The van’s unibody construction made it easy to strip down and rebuild with a roll bar framework and real wood exterior. The classic car is known for its look, but was discontinued in its earlier wooden version due to safety concerns.
“The idea was to maintain the strength of a modern car body with the looks of a Woodie,” says Visser. “It’s like a steel roll cage with wood tacked on.”
He started by removing the engine and transmission and sawing off everything above the corrugated steel floor. He then used 1 1/2-in. angle iron and some 1 1/2-in., 1/8-in. wall tubing for the new frame.
The center rollbar is 2 by 3-in. rectangular tubing. A Y-shaped truss bar extends from the front crossmember over the engine to the firewall roll bar and back to the middle rollbar. This truss bar provides triangulation for front frame horn strength. The rollbar frames are all bolted to the chassis frame. The front rollbar also serves as a frame for the firewall and front windshield.
“The truss ties the rollbars into the body to handle the stress of the road,” says Visser. “In 7 years of driving, I’ve never had a cracked weld or lost a nut off a bolt.”
The original van had the motor to one side to leave room for the driver’s legs. As he rebuilt the van into a Woodie, Visser shortened the chassis by about a foot and moved the motor back about 8 in. and centered it. This required the driveshaft to be shortened by about 20 in. The steering shaft was cut in half and then stretched and angled with an after market tractor U-joint to bring it back to the driver’s new location.
“The steering is smooth, and I can go 60 mph without adjusting the steering wheel,” says Visser.
The front bumper, which was exposed after repositioning the motor, is stock from the 1984 van. So is the steering (except for the shaft), brakes and suspension.
Though Visser did all his own welding, the hood, fenders and rocker panels were fabricated by a Wabash, Ind. metal shop, Schleeming Bros. Metal Work. “They have a ribbing machine to put ribs in the fenders,” he says.
Visser welded custom-bent channel for the grill, splitting it so the upper half with the lights goes up with the hood. The lower half is attached to the chassis.
Other parts, such as home sawn burr oak to frame the plywood panels’ exterior and the new dash, were bartered for from a friend. Another friend sold him five wheels originally from a Jeep for $100. Rebuilding the engine at a cost of $3,500 was the most expensive part of the $6,000 total.
Visser is especially proud of the black paint job on the exposed metal, though it only cost about $75.
“I used about a cup and a half of silver/aluminum mixed into a gallon of black RustOleum,” he says. “The aluminum breaks the sheen of the black surface. With glossy black, normally minor imperfections such as drips and small dents stick out like a sore thumb. The aluminum paint trick allows a black coat with near invisible imperfections.”
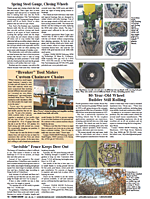
Click here to download page story appeared in.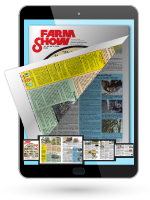
Click here to read entire issue
Van Converted To Old-Style Woodie FARM HOME Cars A junked-out 1984 commercial van provided the chassis Roy Visser needed to create a 1940’s-style “Woodie” The van’s unibody construction made it easy to strip down and rebuild with a roll bar framework and real wood exterior The classic car is known for its look but was discontinued in its earlier wooden version due to safety concerns “The idea was to maintain the strength of a modern car body with the looks of a Woodie ” says Visser “It’s like a steel roll cage with wood tacked on ” He started by removing the engine and transmission and sawing off everything above the corrugated steel floor He then used 1 1/2-in angle iron and some 1 1/2-in 1/8-in wall tubing for the new frame The center rollbar is 2 by 3-in rectangular tubing A Y-shaped truss bar extends from the front crossmember over the engine to the firewall roll bar and back to the middle rollbar This truss bar provides triangulation for front frame horn strength The rollbar frames are all bolted to the chassis frame The front rollbar also serves as a frame for the firewall and front windshield “The truss ties the rollbars into the body to handle the stress of the road ” says Visser “In 7 years of driving I’ve never had a cracked weld or lost a nut off a bolt ” The original van had the motor to one side to leave room for the driver’s legs As he rebuilt the van into a Woodie Visser shortened the chassis by about a foot and moved the motor back about 8 in and centered it This required the driveshaft to be shortened by about 20 in The steering shaft was cut in half and then stretched and angled with an after market tractor U-joint to bring it back to the driver’s new location “The steering is smooth and I can go 60 mph without adjusting the steering wheel ” says Visser The front bumper which was exposed after repositioning the motor is stock from the 1984 van So is the steering except for the shaft brakes and suspension Though Visser did all his own welding the hood fenders and rocker panels were fabricated by a Wabash Ind metal shop Schleeming Bros Metal Work “They have a ribbing machine to put ribs in the fenders ” he says Visser welded custom-bent channel for the grill splitting it so the upper half with the lights goes up with the hood The lower half is attached to the chassis Other parts such as home sawn burr oak to frame the plywood panels’ exterior and the new dash were bartered for from a friend Another friend sold him five wheels originally from a Jeep for $100 Rebuilding the engine at a cost of $3 500 was the most expensive part of the $6 000 total Visser is especially proud of the black paint job on the exposed metal though it only cost about $75 “I used about a cup and a half of silver/aluminum mixed into a gallon of black RustOleum ” he says “The aluminum breaks the sheen of the black surface With glossy black normally minor imperfections such as drips and small dents stick out like a sore thumb The aluminum paint trick allows a black coat with near invisible imperfections ”
To read the rest of this story, download this issue below or click
here to register with your account number.