You have reached your limit of 3 free stories. A story preview is shown instead.
To view more stories
(If your subscription is current,
click here to Login or Register.)
High-Speed Cultivator Adjusts Itself
The Robocrop 2 cultivator can chew through a weedy field at 12 mph, working to within half an inch of the row.
“You get your best performance when using GPS guidance,” says Chris Lunn, Garford Farm Machinery (www.garford.com). “The machine holds its position, and the cultivator hoes adjust in increments of up t
..........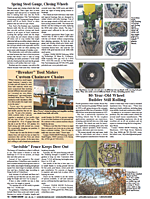
You must sign in, subscribe or renew to see the page.
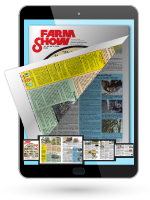
You must sign in, subscribe or renew to see the flip-book
High-Speed Cultivator Adjusts Itself CULTIVATORS The Robocrop 2 cultivator can chew through a weedy field at 12 mph working to within half an inch of the row “You get your best performance when using GPS guidance ” says Chris Lunn Garford Farm Machinery www garford com “The machine holds its position and the cultivator hoes adjust in increments of up to an inch at a time in corn and half an inch at a time in carrots moving to the right or left with the crop plants ” Introduced at Agritechnica in Hannover Germany in 2009 Robocrop was positioned as a combo in-row/between-row cultivator Since then the company has “split” the machine into two with the Garford InRow weeder and the Garford Robocrop high-speed hoe For high-speed work a forward-looking camera identifies the crop rows and compares it to pre-entered row spacing patterns Tillage units selected for the crop and row spacing are then centered on each row adjusting right or left with the row “The guidance system is so accurate that we can put a single hoe between rows on 4 1/2-in spacings such as with cereal grains ” says Lunn Garford offers two variations of the tillage unit One has a maximum lateral movement of 12 in and the other a movement of up to 20 in A 4-row unit requires around 80 hp a 6-row around 100 hp and 150 hp for 12-row units Compact hydraulic side shift systems control hoes InRow cultivation uses the same camera system for between row weeding but also computes spacing between plants in the row and loops a powered hoe in and out between plants Lunn says the InRow unit requires a minimal 8-in spacing between plants and has a maximum speed of 2 mph Lunn indicates that interest in mechanical cultivation is growing “Higher chemical costs restrictions on application and herbicide resistant weeds are all creating demand for mechanical cultivation ” says Lunn “Farmers also see the benefits of cultivation as it aerates the soil breaks up soil caps from a hard rain and mixes nutrients and moisture into that top inch of soil where roots can access it The crop just looks healthier and better within 24 hrs ” The hoe units and guidance system can be mounted on existing toolbars or ordered already mounted Lunn says the highest cost component is the guidance system which includes adjustable tillage units cameras a control unit and in-cab monitor with push button controls “A guidance system mounted on a customer’s existing 40-ft toolbar for high speed cultivating of row crops would be around $30 000 ” says Lunn “If mounted for use on a 20-ft wide 3-bed system for carrots it would be around $60 000 And if intended for in-row cultivation on a 72-in bed you would be looking at around $100 000 ” While the last seems high Lunn says it would allow one man to do 6 to 7 acres a day He says that same amount of cultivation would require 200 men doing hand hoeing “Growers in Michigan told me they sometimes pay as much as $20 per hour for field workers ” says Lunn Currently Garford equipment is distributed by Solex Corporation in California and Willsie Equipment in the rest of North America Contact: FARM SHOW Followup Willsie Equipment Sales R R 1
9516 Northville Rd
Thedford
Ont N0M 2N0 Canada ph 519 243-2616; toll free 800 561-3025; www willsie com ; or Solex Corporation 220 S Jefferson P O Box 490 Dixon Calif 95620 ph 707 678-5533; www solexcorp com
To read the rest of this story, download this issue below or click
here to register with your account number.