Electric Motor Costs Less, Works Better
A new electric motor promises to outperform and outpower traditional electric motors. The Conductor Optimized Rotary Energy (CORE) motor eliminates wound wire and other complexities of traditional electric motors. The CORE motor consists of a printed circuit board with embedded wires sandwiched between two permanent magnet rotors. The new design may revolutionize electric motors and not just in the lawn maintenance products arena where it’s being introduced.
“We have built everything from one hp motors up to a 36-ft. dia. wind generator with our design,” says Matt Jore, chairman, Core Outdoor Power. “We foresee larger versions of our technology going into agricultural equipment. Long-term, we believe it will be adapted to automotive uses.”
He explains that the flat CORE motor design is diameter sensitive. If you double the diameter, you get 8 times the power and torque. The 36-ft. dia., three-megawatt CORE wind generator only generates power in its outer 20 in. The remainder of the diameter is inexpensive struts running out to the stator/rotors ring.
“Most electric motors are complicated systems,” explains Jore. “My son Lincoln had the idea of embedding conductors into a rigid circuit board. Any printed circuit board manufacturer in the world can print one out. All you have to do is laminate the stator, assemble it with rotors on a shaft, and pop a housing over it.”
The CORE motor is not only easy to build, it is also extremely efficient. The CGT line trimmer, the first outdoor tool with a CORE motor, will be introduced in spring 2012 for $249. What sets it apart from other electric trimmers is that it will run as long on a single charge as a gas-powered trimmer would run on a tank of gas. Just as important is that it will produce as much torque as that gas engine.
With the CORE motor mounted right on the trimmer head and no gearbox needed, the CGT trimmer weighs just 8-lbs., 11-lbs.with its power cell. It runs up to 70 min. on a charge and recharges in 3 hours (less with an optional rapid charger). It offers two speed modes -- 7,000 rpm’s for light trimming and 5,000 rpm’s for high torque trimming. It has no vibration, little noise and starts instantly at full torque.
Later in 2012 the company will introduce GasLess hedge trimmers and handheld and backpack blowers. In 2013 a self-propelled lawn mower, the first wheeled product with a CORE motor, will be introduced. It will weigh 85 lbs., cut a 21-in. swath and run up to 60 min. on a single charge. Prices have not yet been set for these tools.
Introducing their own line of outdoor power tools is as much about proving the value of the CORE technology as it is developing a profit center. Jore notes that introducing a new technology is always difficult; however, emission standards are driving costs through the roof. An alternative motor and power source are needed.
“The motor is only 50 percent of the equation,” says Jore. “The other part is the power source.”
Jore notes that most existing lithium ion batteries are not capable of competing with gas motors for power or running time. Those few that can are very expensive. CORE is working on a new non-chemical based power source it hopes to introduce in 2012. The company is working with Molycorp, the only producer of rare earth oxide outside of China. Currently the new energy cell can power a cell phone for two days. The goal is to size it up.
“If we are successful, it will be a superior power source at 1/10 the cost of current lithium ion batteries,” says Jore. “We will then be able to expand the use of our technology from hand held equipment and push mowers to the rest of these categories.”
He acknowledges that the motor’s flat profile limits its use in small diameter spaces where lots of power is needed, such as in-line pumps. That said, he thinks there are plenty of opportunities for its use, such as in vehicles. He points out that electric wheel motors have trouble standing up to the beatings wheels and axles take.
“Really good gears are hard to beat for durability and expense,” suggests Jore. “Why not use the existing proven axle, transmission and differential in a modern car? Put a flat CORE motor on top of the differential and just run the driveshaft between them.”
Given the CORE ratio of power to diameter, the larger the car (axle length), the greater the diameter motor that could be installed. “If a machine designer can give us an inch or two more diameter, it’s always worth it for producing higher torque at a lower cost,” he says.
Currently Core Outdoor Power purchases the circuit board stator and rotors, but makes all other components at its Montana location. Eventually Jore hopes to be providing entire power trains and power sources to OEMs.
Contact: FARM SHOW Followup, Core Outdoor Power, 34837 Innovation Dr., Ronan, Mont. 59864 (ph 855 831-2673; www.coreoutdoorpower.com).
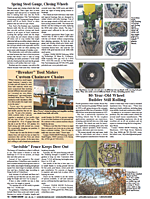
Click here to download page story appeared in.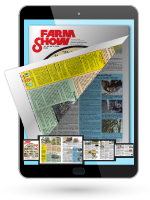
Click here to read entire issue
Electric Motor Costs Less Works Better ENERGY Miscellaneous A new electric motor promises to outperform and outpower traditional electric motors The Conductor Optimized Rotary Energy CORE motor eliminates wound wire and other complexities of traditional electric motors The CORE motor consists of a printed circuit board with embedded wires sandwiched between two permanent magnet rotors The new design may revolutionize electric motors and not just in the lawn maintenance products arena where it’s being introduced “We have built everything from one hp motors up to a 36-ft dia wind generator with our design ” says Matt Jore chairman Core Outdoor Power “We foresee larger versions of our technology going into agricultural equipment Long-term we believe it will be adapted to automotive uses ” He explains that the flat CORE motor design is diameter sensitive If you double the diameter you get 8 times the power and torque The 36-ft dia three-megawatt CORE wind generator only generates power in its outer 20 in The remainder of the diameter is inexpensive struts running out to the stator/rotors ring “Most electric motors are complicated systems ” explains Jore “My son Lincoln had the idea of embedding conductors into a rigid circuit board Any printed circuit board manufacturer in the world can print one out All you have to do is laminate the stator assemble it with rotors on a shaft and pop a housing over it ” The CORE motor is not only easy to build it is also extremely efficient The CGT line trimmer the first outdoor tool with a CORE motor will be introduced in spring 2012 for $249 What sets it apart from other electric trimmers is that it will run as long on a single charge as a gas-powered trimmer would run on a tank of gas Just as important is that it will produce as much torque as that gas engine With the CORE motor mounted right on the trimmer head and no gearbox needed the CGT trimmer weighs just 8-lbs 11-lbs with its power cell It runs up to 70 min on a charge and recharges in 3 hours less with an optional rapid charger It offers two speed modes -- 7 000 rpm’s for light trimming and 5 000 rpm’s for high torque trimming It has no vibration little noise and starts instantly at full torque Later in 2012 the company will introduce GasLess hedge trimmers and handheld and backpack blowers In 2013 a self-propelled lawn mower the first wheeled product with a CORE motor will be introduced It will weigh 85 lbs cut a 21-in swath and run up to 60 min on a single charge Prices have not yet been set for these tools Introducing their own line of outdoor power tools is as much about proving the value of the CORE technology as it is developing a profit center Jore notes that introducing a new technology is always difficult; however emission standards are driving costs through the roof An alternative motor and power source are needed “The motor is only 50 percent of the equation ” says Jore “The other part is the power source ” Jore notes that most existing lithium ion batteries are not capable of competing with gas motors for power or running time Those few that can are very expensive CORE is working on a new non-chemical based power source it hopes to introduce in 2012 The company is working with Molycorp the only producer of rare earth oxide outside of China Currently the new energy cell can power a cell phone for two days The goal is to size it up “If we are successful it will be a superior power source at 1/10 the cost of current lithium ion batteries ” says Jore “We will then be able to expand the use of our technology from hand held equipment and push mowers to the rest of these categories ” He acknowledges that the motor’s flat profile limits its use in small diameter spaces where lots of power is needed such as in-line pumps That said he thinks there are plenty of opportunities for its use such as in vehicles He points out that electric wheel motors have trouble standing up to the beatings wheels and axles take “Really good gears are hard to beat for durability and expense ” suggests Jore “Why not use the existing proven axle transmission and differential in a modern car? Put a flat CORE motor on top of the differential and just run the driveshaft between them ” Given the CORE ratio of power to diameter the larger the car axle length the greater the diameter motor that could be installed “If a machine designer can give us an inch or two more diameter it’s always worth it for producing higher torque at a lower cost ” he says Currently Core Outdoor Power purchases the circuit board stator and rotors but makes all other components at its Montana location Eventually Jore hopes to be providing entire power trains and power sources to OEMs
Contact: FARM SHOW Followup Core Outdoor Power 34837 Innovation Dr Ronan Mont 59864 ph 855 831-2673; www coreoutdoorpower com
To read the rest of this story, download this issue below or click
here to register with your account number.