Expert Repairs Worn-Down Anvils
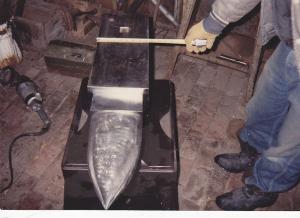 ✖  |
Brian Johnson can make a bashed up old anvil look like new. He also made a new anvil from scratch. An experienced blacksmith, Johnson knows how vital a smooth anvil surface is. He also knows how beat up most old anvils are and how poorly made many new anvils are. That’s why he made his own “giant” anvil and fixes up others.
“I made an 8-in. wide, 1,000-lb. anvil out of 1,237 lbs. of steel,” he says. “The top and base are 4-in. thick steel plate, and the stem is 6-in. thick steel plate.”
The proof of a good anvil is how resilient the top is. Johnson says the way to test an anvil is to drop a ball bearing from about a foot above the surface. It should bounce back up into your hand. The resiliency is what makes a blacksmith’s hammer bounce back into the air when he strikes hot iron on the anvil.
Wrought iron anvil tops and bases are Johnson’s preference. Since wrought iron is no longer made, he settled for mild steel for the top, base and stem on his new anvil. To get the resilient top, he needed a final hard surface. Johnson applied two layers of Rockwell 62 hard facing, 6010 (super buildup) class rod or wire. The second layer was laid down perpendicular to the first, with each layer measuring from 5/32 to 3/16 of an inch thick.
He follows a similar procedure in repairing old anvils. Once he has ground out any rust in pits or cracks, Johnson uses penetrant dye to find fine cracks. He then grinds until no more die can be seen, indicating fresh metal.
In both his new and old anvils, Johnson heats the anvil to a surface temperature of around 400 degrees Farhenheit. This helps ensure an even weld. If the welding process is interrupted, he will reheat before resuming welding. Johnson also fills pritchel and hardy holes with pieces of carbon block to prevent weld deposit.
“Each pass overlaps the previous one,” he explains. “If you lean the anvil away from you, the passes get thicker.”
Johnson uses bumper bars to either side of the welding path. These are copper plates that are clamped in place. This allows him to make a complete pass each time from one end to the other or side-to-side.
On old anvils, the first layer fills in cracks and holes. “You need to lead the forward edge of the puddle into a vertical crack to be sure it fills in properly,” he advises.
As the second layer is finished, Johnson advises using a measuring tape to be sure the new surface is even from the base. He then uses a square to evaluate how level it is at the surface. If needed, more weld is added.
Again Johnson applies heat to the entire surface of the anvil as he finishes layering the weld. “Oftentimes, the welding will leave one part of the surface hotter than other areas,” he explains.
Even cooling is as important as even heating, he adds. “I will turn a smaller anvil over into a pile of barn lime to cool overnight,” he says. “It’s a good insulator and slows the process. Larger anvils will get barn lime heaped over the top, and the entire anvil will then be wrapped in fiberglass insulation and left to cool slowly.”
Once two even layers are in place and evenly cooled, Johnson grinds them down. Initially he uses a grinding wheel on edge to take off the ridges. Once the surface is down to ripples not ridges, he begins a horizontal grinding pattern using a 6-in. cup wheel. He stops frequently to be sure he is maintaining an even, level top. Chalk rubbed on high spots make it easier to level.
“For the final finish, I use a lunchbox grinder with special disks,” says Johnson. “I also chamfer out the pritchel and hardy holes to reduce the chance of chipping.”
Johnson also dresses up the edges of the anvil top. On some anvils he has reworked or rebuilt the horn, pritchel and hardy holes and even the base prior to adding the hard surface to the top.
While some anvils may be too far gone to repair, most can be renewed. The exception in Johnson’s mind is cast iron anvils.
“An old wrought iron anvil is my first preference, followed by mild steel,” he says. “However, if it’s cast iron, it’s not worth anything.”
Contact: FARM SHOW Followup, Brian Johnson, 16777 County Rd. 751 N.W., Clearwater, Minn. 55320 (ph 320 558-6898).
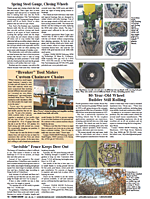
Click here to download page story appeared in.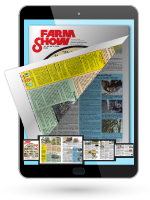
Click here to read entire issue
Expert Repairs Worn-Down Anvils FARM SHOP Tools Brian Johnson can make a bashed up old anvil look like new He also made a new anvil from scratch An experienced blacksmith Johnson knows how vital a smooth anvil surface is He also knows how beat up most old anvils are and how poorly made many new anvils are That’s why he made his own “giant” anvil and fixes up others “I made an 8-in wide 1 000-lb anvil out of 1 237 lbs of steel ” he says “The top and base are 4-in thick steel plate and the stem is 6-in thick steel plate ” The proof of a good anvil is how resilient the top is Johnson says the way to test an anvil is to drop a ball bearing from about a foot above the surface It should bounce back up into your hand The resiliency is what makes a blacksmith’s hammer bounce back into the air when he strikes hot iron on the anvil Wrought iron anvil tops and bases are Johnson’s preference Since wrought iron is no longer made he settled for mild steel for the top base and stem on his new anvil To get the resilient top he needed a final hard surface Johnson applied two layers of Rockwell 62 hard facing 6010 super buildup class rod or wire The second layer was laid down perpendicular to the first with each layer measuring from 5/32 to 3/16 of an inch thick He follows a similar procedure in repairing old anvils Once he has ground out any rust in pits or cracks Johnson uses penetrant dye to find fine cracks He then grinds until no more die can be seen indicating fresh metal In both his new and old anvils Johnson heats the anvil to a surface temperature of around 400 degrees Farhenheit This helps ensure an even weld If the welding process is interrupted he will reheat before resuming welding Johnson also fills pritchel and hardy holes with pieces of carbon block to prevent weld deposit “Each pass overlaps the previous one ” he explains “If you lean the anvil away from you the passes get thicker ” Johnson uses bumper bars to either side of the welding path These are copper plates that are clamped in place This allows him to make a complete pass each time from one end to the other or side-to-side On old anvils the first layer fills in cracks and holes “You need to lead the forward edge of the puddle into a vertical crack to be sure it fills in properly ” he advises As the second layer is finished Johnson advises using a measuring tape to be sure the new surface is even from the base He then uses a square to evaluate how level it is at the surface If needed more weld is added Again Johnson applies heat to the entire surface of the anvil as he finishes layering the weld “Oftentimes the welding will leave one part of the surface hotter than other areas ” he explains Even cooling is as important as even heating he adds “I will turn a smaller anvil over into a pile of barn lime to cool overnight ” he says “It’s a good insulator and slows the process Larger anvils will get barn lime heaped over the top and the entire anvil will then be wrapped in fiberglass insulation and left to cool slowly ” Once two even layers are in place and evenly cooled Johnson grinds them down Initially he uses a grinding wheel on edge to take off the ridges Once the surface is down to ripples not ridges he begins a horizontal grinding pattern using a 6-in cup wheel He stops frequently to be sure he is maintaining an even level top Chalk rubbed on high spots make it easier to level “For the final finish I use a lunchbox grinder with special disks ” says Johnson “I also chamfer out the pritchel and hardy holes to reduce the chance of chipping ” Johnson also dresses up the edges of the anvil top On some anvils he has reworked or rebuilt the horn pritchel and hardy holes and even the base prior to adding the hard surface to the top While some anvils may be too far gone to repair most can be renewed The exception in Johnson’s mind is cast iron anvils “An old wrought iron anvil is my first preference followed by mild steel ” he says “However if it’s cast iron it’s not worth anything ” Contact: FARM SHOW Followup Brian Johnson 16777 County Rd 751 N W Clearwater Minn 55320 ph 320 558-6898
To read the rest of this story, download this issue below or click
here to register with your account number.