Air Exchange Unit Slashes Crop Drying Time And Cost
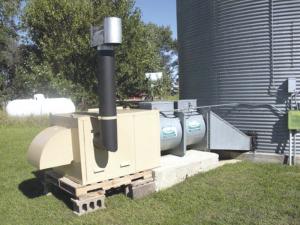 ✖  |
You can cut fuel use when drying crops by up to 75 percent with a Desert Air Crop Dryer, according to Siebring Mfg. The innovative drier uses a heat exchanger to dry with drier, cleaner air than conventional dryers. After several years of testing, the company is now taking orders for this fall’s drying season.
“Conventional direct heat dryers are pumping a pound of water or more into the bin with each pound of fuel used,” says Warren Tiederman, Siebring Mfg. “LP releases nearly a gallon of water per 100,000 btu’s into the grain, plus contaminants. The heat has to dry that water out before it can start to dry the grain.”
By putting a heat exchanger between the burner and the fan blowing the heat into the bin, Siebring uses drier air to begin with. The heat exchanger also prevents the water in the fuel from entering the bin.
When the heat exchanger warms the air even 10°, it doubles the air's water holding capacity. Heating it 20° quadruples water holding capacity. When it hits the grain, it pulls moisture out of the grain more effectively. It is that efficiency that saves fuel and time in the drying process, says Tiederman.
Eliminating the direct discharge of heat from the burners into the bin also protects grain quality. The cooler, but drier air reduces stress cracks and actually increases test weight.
"Farmers tell us corn coming out of our drying process looks more like corn dried on the cob in a crib," says Tiederman. "We had a North Dakota farmer take seed beans out at 19.5 percent, put them in a 60-in. thick layer in the bin and hook up one of our small units. When the company tested the beans, they found no cracks."
Siebring, a supplier of equipment for greenhouses, is new to the crop drying business. Tiederman grew up on a farm and had lots of experience with crop dryers. He and company founder Gordon Siebring realized the more gentle heat and cleaner air they produced with their heat exchanger-equipped greenhouse system would work on grain as well.
"We tested it for a couple years," says Tiederman. "At first we thought we would have to get the temperature up to 130°. We quickly realized we only needed to raise it a few degrees. A 10° increase on a dry, warm day has a huge effect."
The savings are huge as well. Tiederman points to one unit custom installed for a North Dakota farmer. He does the same job with 210,000 btu's that previously required a million btu's with a direct-fire dryer. The cost of the dryer is less as well.
"A 210,000 btu unit with our heat exchanger only costs about $4,000," says Tiederman. "Setup is simple. All you need is a fuel tank and a bin with a fan. Set the heat exchanger in front of the fan and start them up. We have a relay built in, so if the bin fan isn't running, our dryer won't run either."
Tiederman says the Desert Air Crop Dryer works best with a bin equipped with a stirrator. However, even a simple full floor bin will work if the center is drawn down before drying starts.
While the heat exchanger idea is similar to natural air drying, the big difference is time and the expense of running the fan.
“Natural air drying might require the fan to run for a month,” says Tiederman. “With our heat exchanger, energy use will actually be less.”
Contact: FARM SHOW Followup, Siebring Mfg., 303 S. Main St., P.O. Box 658, George, Iowa 51237 (ph 712 475-3317 or 888 475-3317; sales@siebringmfg.com; www.siebringmfg.com).
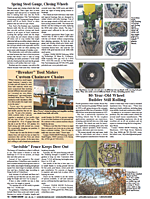
Click here to download page story appeared in.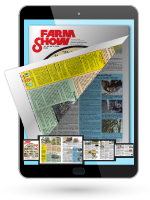
Click here to read entire issue
Air Exchange Unit Slashes Crop Drying Time And Cost GRAIN DRYERS You can cut fuel use when drying crops by up to 75 percent with a Desert Air Crop Dryer according to Siebring Mfg The innovative drier uses a heat exchanger to dry with drier cleaner air than conventional dryers After several years of testing the company is now taking orders for this fall’s drying season “Conventional direct heat dryers are pumping a pound of water or more into the bin with each pound of fuel used ” says Warren Tiederman Siebring Mfg “LP releases nearly a gallon of water per 100 000 btu’s into the grain plus contaminants The heat has to dry that water out before it can start to dry the grain ” By putting a heat exchanger between the burner and the fan blowing the heat into the bin Siebring uses drier air to begin with The heat exchanger also prevents the water in the fuel from entering the bin When the heat exchanger warms the air even 10° it doubles the air s water holding capacity Heating it 20° quadruples water holding capacity When it hits the grain it pulls moisture out of the grain more effectively It is that efficiency that saves fuel and time in the drying process says Tiederman Eliminating the direct discharge of heat from the burners into the bin also protects grain quality The cooler but drier air reduces stress cracks and actually increases test weight Farmers tell us corn coming out of our drying process looks more like corn dried on the cob in a crib says Tiederman We had a North Dakota farmer take seed beans out at 19 5 percent put them in a 60-in thick layer in the bin and hook up one of our small units When the company tested the beans they found no cracks Siebring a supplier of equipment for greenhouses is new to the crop drying business Tiederman grew up on a farm and had lots of experience with crop dryers He and company founder Gordon Siebring realized the more gentle heat and cleaner air they produced with their heat exchanger-equipped greenhouse system would work on grain as well We tested it for a couple years says Tiederman At first we thought we would have to get the temperature up to 130° We quickly realized we only needed to raise it a few degrees A 10° increase on a dry warm day has a huge effect The savings are huge as well Tiederman points to one unit custom installed for a North Dakota farmer He does the same job with 210 000 btu s that previously required a million btu s with a direct-fire dryer The cost of the dryer is less as well A 210 000 btu unit with our heat exchanger only costs about $4 000 says Tiederman Setup is simple All you need is a fuel tank and a bin with a fan Set the heat exchanger in front of the fan and start them up We have a relay built in so if the bin fan isn t running our dryer won t run either Tiederman says the Desert Air Crop Dryer works best with a bin equipped with a stirrator However even a simple full floor bin will work if the center is drawn down before drying starts While the heat exchanger idea is similar to natural air drying the big difference is time and the expense of running the fan “Natural air drying might require the fan to run for a month ” says Tiederman “With our heat exchanger energy use will actually be less ” Contact: FARM SHOW Followup Siebring Mfg 303 S Main St P O Box 658 George Iowa 51237 ph 712 475-3317 or 888 475-3317; sales@siebringmfg com; www siebringmfg com
To read the rest of this story, download this issue below or click
here to register with your account number.