You have reached your limit of 3 free stories. A story preview is shown instead.
To view more stories
(If your subscription is current,
click here to Login or Register.)
One-Of-A-Kind Prefab House
Jim Struble prefabricated his multi-story, 4,500 sq. ft. house, assembling it in 3-story segments on the ground using round logs, flat-sided laminated beams, and structural panels. Even the roof was pre-fabbed in panels that could be lifted in place.
"I spent several years just planning everything out," says S
..........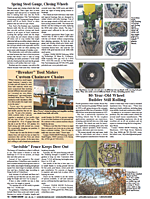
You must sign in, subscribe or renew to see the page.
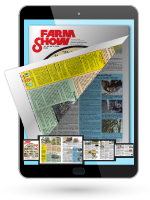
You must sign in, subscribe or renew to see the flip-book
One-Of-A-Kind Prefab House Jim Struble prefabricated his multi-story 4 500 sq ft house assembling it in 3-story segments on the ground using round logs flat-sided laminated beams and structural panels Even the roof was pre-fabbed in panels that could be lifted in place I spent several years just planning everything out says Struble a former shop teacher and automotive engineer Building on the ground in sections let him build the house himself at a much lower cost He cut 90 logs for the project and milled out 45 on a mobile bandsaw-style sawmill The building has a cement foundation with the bottom level serving as storage The dimensions for each of the three floors above it are 32 ft wide by 44 ft long Struble used round logs for beams on the first and third floors with laminated beams on the second floor Squared timbers on the outside walls of the first and third levels match round log beams used on the interior Using the same size and type of wood ensures they will shrink at the same rate as they dry over time explains Struble Using round logs for posts and beams meant each one had to be precisely measured and accounted for in the plan Even the most uniform pair of logs differed to some degree Log tapers from one end to the other had to be taken into account His sawmill helped him to precisely prepare posts and beams for the unique design Struble selected Y-shaped logs for posts and fitted the top ends with support plates Round log beams sawn flat on their top side were notched to rest on the support plate When lifted into place the beam support plate rested on half a post support plate When the next three-floor segment was erected a new beam support plate would rest on the other half of the post support plate Butt or end plates were fixed to each beam end The support plates on the posts and beams provided flat facing surfaces that could be screwed together just as the butt plates on the beam ends did explains Struble If one log end was larger diameter than the facing one I just notched it deeper so the flat top surfaces matched up level When he finished the assembled 39 panels of floor roof and exterior walls were within 1/16-in on one side and 3/4-in on the other of the 32-ft by 44-ft plan Struble still has substantial work remaining on the interior However once complete he and his wife will have living quarters on the third level First and second levels will each have a two-bedroom suite and a one-bedroom suite An elevator is being installed at one end of the house next to a stair tower Each suite and Struble s living quarters will have views of Lake Huron six nearby islands and a lighthouse Struble says it has all been worth it Doing the construction this way I was able to do it all with the help of a friend in his 70 s who operated the crane explains Struble Each panel as it was let down could be shifted around with a bar until it was in just the right spot I couldn t have done it by myself any other way Contact: FARM SHOW Followup James Struble 2363 S Hill Island Rd Cedarville Mich 49719 ph 906 484-2976; cell 517 331-3803; jim@dancingwatersbnb com; www dancingwatersbnb com
To read the rest of this story, download this issue below or click
here to register with your account number.