You have reached your limit of 3 free stories. A story preview is shown instead.
To view more stories
(If your subscription is current,
click here to Login or Register.)
He Built His Own Skid Steer Loader
"I built my own skid steer loader for $3,100, saving thousands of dollars on the cost of a comparable new one," says Rob Martens, Steinbach, Manitoba, who used parts from a pair of self-propelled swathers.
"It's so comfortable to operate that I can hardly wait to find jobs to use it for. When my wife hears me st
..........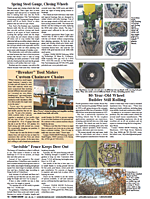
You must sign in, subscribe or renew to see the page.
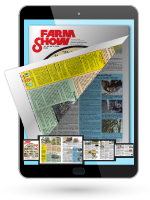
You must sign in, subscribe or renew to see the flip-book
He Built His Own Skid Steer Loader TRACTORS Made-It-Myself 20-1-2 "I built my own skid steer loader for $3,100, saving thousands of dollars on the cost of a comparable new one," says Rob Martens, Steinbach, Manitoba, who used parts from a pair of self-propelled swathers.
"It's so comfortable to operate that I can hardly wait to find jobs to use it for. When my wife hears me start it up, she wonders if I'm really working or just playing around," says Martens, who raises hogs.
He bought an International swather for $100 and stripped off everything except the hydraulic components, gas tank, seat, and 15-in. wheels. He used 4-in. sq., 1/4-in. thick steel tubing to make a frame and welded on two steel posts that attach to the loader arms off a Deere tractor. He used 1 1/4-in. steel rod to make axles and welded steel plates onto each end, drilling holes in the plates that match up with the bolt holes on the swather wheels.
The skid steer is powered by a Wisconsin 4-cyl. air-cooled gas engine (rated at 37 hp) and transmission salvaged from a junked Co-Op self-propelled swather. Originally, Martens used the swather transmission and clutches to chain-drive the wheels, but the clutches needed constant adjustment and wore out quickly so he replaced them with orbit motors powered by a 28 gpm hydraulic pump that's belt-driven off the engine. The orbit motors chain-drive the rear wheels which in turn chain-drive the front wheels. Each orbit motor is controlled by a Gresen 400 single spool valve. A splitter valve runs off the hydraulic pump to divide the flow equally to each of the valves.
Martens used 1 1/2-in. sq., 1/4-in. thick steel tubing to build a rollover cage. The 6-ft. wide bucket was custom made. A separate 12 gpm hydraulic pump operates a pair of hydraulic cylinders that raise or lower the arms. Two more cylinders are used to tilt the bucket.
"It has a lot of pushing power. With a 12-tooth sprocket on the orbital motor and a 72-tooth sprocket on the drive wheel, I get about 5,500 lbs. of torque on each side," says Martens. "By pushing one lever forward and the other back, I can turn the machine around on a dime.
"I built it because I needed a tractor with a bucket but couldn't justify the cost of a new tractor. The least expensive tractor that I could find to do what I wanted would have cost about $10,000. It took about a year to collect the parts and another two winters to build. I got the loader arms from a neighbor who had used it on a tractor that was too big, causing the loader to break. My custom-made, 6-ft. bucket is stronger than any-thing on the market. It's made from 3/8-in. steel and has extra wear plates on the bottom. I'm only 27 but it'll probably last as long as I farm. "The gas tank mounts under the seat and the hydraulic reservoir behind the operator's shoulders. I kept the swather gauges so I can monitor everything from electrical voltage to hydraulic oil temperature."
Contact: FARM SHOW Followup, Rob Martens, Box 20404, Steinbach, Manitoba, Canada R0A 2T1 (ph 204 326-9599).
To read the rest of this story, download this issue below or click
here to register with your account number.