You have reached your limit of 3 free stories. A story preview is shown instead.
To view more stories
(If your subscription is current,
click here to Login or Register.)
Wood Burning Stoves Converted To Burn Corn
A pair of modified Taylor outside wood burning stoves do a great job of burning corn for Charles Wills and his sons Scott and Brian of Carlinville, Ill.
Both stoves were converted to burn corn, which is stored in a pair of bulk bins. An automated delivery system feeds corn from the bins into each stove. The
..........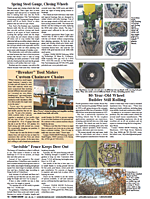
You must sign in, subscribe or renew to see the page.
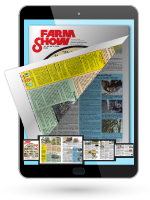
You must sign in, subscribe or renew to see the flip-book
Wood Burning Stoves Converted To Burn Corn ENERGY Alternative Fuels A pair of modified Taylor outside wood burning stoves do a great job of burning corn for Charles Wills and his sons Scott and Brian of Carlinville Ill Both stoves were converted to burn corn which is stored in a pair of bulk bins An automated delivery system feeds corn from the bins into each stove The heat that s generated is delivered through underground pipes that lead to a radiant floor heating system in the building s concrete floor Burning corn instead of wood requires a lot less labor and is far more cost efficient than burning LP gas In fact it has reduced our heating bill by about half says Wills who farms and along with his sons owns a custom cabinetry business that makes everything from interior doors to cabinets and trims He also sells hardwood flooring and countertops Their manufacturing shop occupies about 46 000 sq ft of floor space To keep dust under control they have to move about 35 000 cu ft of air per minute out of the building which makes it more costly to heat An old coal stoker feeds one corn stove that s located at the north end of the building A big hole was cut into the stove where the stoker welds to it The other stove is located at the south end of the building where a motor-driven computerized delivery system automatically feeds corn into the stove as needed Each stove burns 1 to 3 bushels per hour The two stoves produce a total of 1 million btu s per hour which is more than enough to heat the building says Wills Each bin holds 200 to 300 bu and we refill the bins every 7 or 8 days There s a lot of flammable materials inside the building The stoves are located outside the building which greatly reduces fire danger The coal stoker they use was purchased locally Years ago a lot of coal was mined in this area and many people used coal-fired furnaces to heat their homes The coal was dumped into basement bins and then the homeowner hand fed it into a stoker bin which delivered the coal into the furnace The auger on the coal stoker was originally geared to run at 3 rpm s which was too fast for the stove so Wills geared the auger down to run at a slower 7/8 rpm s The other stove is fed corn by a computerized delivery system which was invented by a company in the state of Washington Wills had the stove custom-built to burn on corn The Taylor company had already built stoves that could burn flax seed and cotton seed but not corn says Wills The computerized system they came up with automatically feeds corn into the stove as needed so it burns at maximum efficiency The system wasn t cheap but considering the volume of heat we use it has more than paid for itself through labor savings notes Wills Contact: FARM SHOW Followup Charles Wills 9674 Colt Rd Carlinville Ill 62626 ph 217 854-9056; jwills@willsmilling com; www willsmilling com
To read the rest of this story, download this issue below or click
here to register with your account number.