2010 - Volume #34, Issue #5, Page #10
[ Sample Stories From This Issue | List of All Stories In This Issue | Print this story
| Read this issue]
Combine Converted To Ear Corn Picker
![]() |
"I don't have downed stalks at the end rows anymore," says Newbury. "Instead, I harvest the ears and store them with the silage. The cows eat them like candy, burrowing into the silage to get at them."
Newbury had wanted to build a self-propelled ear corn picker for several years. When a cousin offered him a 1960's 55 Deere, Newbury got busy.
"The combine had been outside for about 10 years. He said I could have it if I could start it," he says. "I had to clean out the fuel lines and replace the battery, radiator, points and fuel pump. That was enough to get it running."
To get it home, Newbury also needed a new set of rear tires. He also found a quick-tach feeder housing that fit the old combine.
"I found a three-row corn head sitting in a fence row and mounted it to the feeder housing," says Newbury. "The hardest thing to find was an elevator."
Newbury wanted an old flat bottom grain or hay elevator to move the ears into a trailing wagon. Once he found one, he cut it down to about 20 ft. in length and gutted out the combine's threshing mechanism to make room for it.
"We slid the elevator in place and welded on some tin to gather the ears as they came through the feeder housing and dropped onto the elevator," he says.
Newbury cut a hole in the top of the combine housing and braced it so the elevator could rest there at an angle above the towed wagon.
"It's high enough. It works with either a gravity box or a barge box with hoist," says Newbury.
To power the elevator, he replaced the original pto shaft with a longer shaft that extends through the combine wall. A drive pulley mounted to the shaft end is driven by the original grain tank unload belt drive.
"The feeder housing was the most expensive part of the whole venture," says Newbury. "I probably have $1,000 in the whole rig."
The ear corn harvester has more than paid for itself. Newbury isn't wasting ears in the field, and his cows love the ears at the feed bunk. To store the ears, he simply spreads them on the floor of his temporary trench silo (two rows of big round bales). As the silage is packed on top of the ears, they ferment along with it.
"The whole ear gets really soft and palatable," he says.
Contact: FARM SHOW Followup, David Newbury, 6701 Horse Prairie Rd., Sesser, Ill. 62884 (ph 618 625-6404).
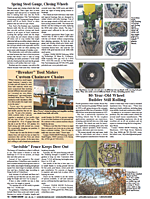
Click here to download page story appeared in.
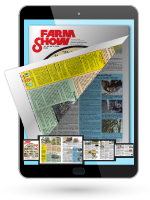
Click here to read entire issue
To read the rest of this story, download this issue below or click here to register with your account number.