You have reached your limit of 3 free stories. A story preview is shown instead.
To view more stories
(If your subscription is current,
click here to Login or Register.)
"Slabwood Cabins" Help Attract New Buisness
Alec Alberti makes his living selling firewood so he's always looking for a way to promote his business.
That's why he decided to build a pair of "slabwood cabins" made from "mortarless" stacks of firewood. One of the cabins is used to store firewood, and the other to store woodworking tools. It has a wood burni
..........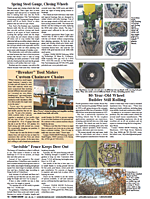
You must sign in, subscribe or renew to see the page.
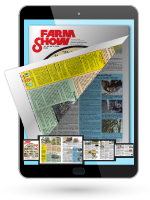
You must sign in, subscribe or renew to see the flip-book
"Slabwood Cabins" Help Attract New Buisness 34-3-9 Alec Alberti makes his living selling firewood so he's always looking for a way to promote his business.
That's why he decided to build a pair of "slabwood cabins" made from "mortarless" stacks of firewood. One of the cabins is used to store firewood, and the other to store woodworking tools. It has a wood burning stove inside with a steel chimney flue sticking out the roof.
To build the walls of each cabin he simply stacked 16-in. lengths of slabwood on top of each other. "The walls are built without a single nail," he says.
The slabwood cabins were erected in 2000 and are still standing in good condition.
"They've become local landmarks and good attention grabbers for my business. People stop by to photograph them all the time," says Alberti.
"When people first see the cabins they can't believe they're really made of slabwood and wonder why they don't fall down. I tell them it's because of the interlocking technique I use and because of the framing system. The strange thing is that all the slabwood is stacked directly on the ground, with no foundation at all, yet the building never heaves or shifts.
"Last winter my slabwood cabins survived the worst snowstorm of the century. I didn't remove the massive amount of snow on the roofs of the cabins and yet, because of their unique construction, they were able to withstand the weight of all that snow and didn't collapse even though many other buildings in our area did collapse from the weight of the snow."
Each cabin measures 30 ft. long by 15 ft. wide and has 10-ft. high slabwood walls. There's a door and windows on three sides and a sloped, tar-papered roof covered with slabs of hemlock.
Building the cabins was easy, once he got started, he says. The first step was to lay interlocking slabwood support stacks at each corner and also at each end of the building. The slabwood is simply piled up between the corner stacks. "I kept everything leaning inward as I built the walls up," says Alberti.
He placed a 15-ft. long spruce pole at each end of the cabin to support the rafters, lashing the bottom of each pole to a locust pole that's buried in the ground. "I didn't want to bury the spruce poles in the ground because they would rot," says Alberti. More locust posts are placed at each corner inside the building to support the slabwood.
The roof's frame is made from small spruce trees spaced 2 ft. apart. The rafters never touch the slabwood walls.
He built the window frames out of 2 by 6's and nailed them to some slabwood, then placed windows off an old building inside them.
"Each cabin took about 2 months to build," says Alberti. "I fill one of the cabins solid with firewood, and take it out as I sell it. The wind blows through and dries the wood, while the roof keeps rain and snow off."
The walls of the cabin with the wood stove are lined by 1/4-in. plywood to keep the wind out. "It can be 20 degrees below zero outside but I can still wear a T-shirt inside," says Alberti. "At one time I had a maple syrup boiler for demonstration purposes inside this cabin, with a cupola on the roof to vent steam produced by the boiler. However, when I converted the cabin into a shop for tools I removed the cupola."
Homemade chainsaw-carved sculptures decorate the cabins, including fake wood crows and toadstools.
Alberti says he started selling firewood at age 16. "I would cut and split wood all winter and pile it to season until I sold it the following autumn."
Alberti has used firewood to build other structures, including a giant 18-axle log truck and a full-sized semi truck (featured in Vol. 21, No. 1).
Contact: FARM SHOW Followup, Alec Alberti Jr., 4924 Rt. 23, Windham, N.Y. 12496 (ph 518 734-4689; alecalbertijr@yahoo.com).
To read the rest of this story, download this issue below or click
here to register with your account number.