You have reached your limit of 3 free stories. A story preview is shown instead.
To view more stories
To view more stories
SUBSCRIBE OR RENEW NOW
(If your subscription is current, click here to Login or Register.)2010 - Volume #34, Issue #1, Page #4
[ Sample Stories From This Issue | List of All Stories In This Issue]
Go-Anywhere Post Driver
Larry Marah's all-hydraulic, self-propelled post driver isn't pretty and it's not fast, but it has enough traction and power to install fencelines on very steep hillsides. "In low gear it goes so slow you can hardly see the wheels move, but it will climb anything the wheels can get footing on," he says. "..........
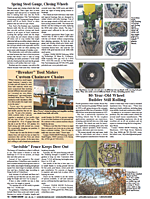
You must sign in, subscribe or renew to see the page.
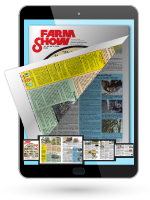
You must sign in, subscribe or renew to see the flip-book
Go-Anywhere Post Driver FENCING Miscellaneous Larry Marah s all-hydraulic self-propelled post driver isn t pretty and it s not fast but it has enough traction and power to install fencelines on very steep hillsides
In low gear it goes so slow you can hardly see the wheels move but it will climb anything the wheels can get footing on he says I ve used it in places I wouldn t take a 4-WD tractor The only way I could improve it is to put tractor treads on the wheels
Once he gets to the general area he can precisely maneuver into position thanks to the two front axles he used and the separate hydraulic cylinders on each set of tie rods
He can turn both sets of wheels in the same direction and crab steer on the diagonal or turn front and back axles in opposite directions to make extremely tight turns He can also steer with either front or back axles and let the other trail
At the job site the post driver can be adjusted across a 90 degree arc from the front of the vehicle to the immediate left Once roughly in the right place Marah can fine tune positioning by telescoping the post driver mount away from the vehicle as needed or tip the post driver at an angle to match the slope he s on Everything is powered hydraulically which is why Marah spent plenty on hydraulics for the rig
When I sat down and figured out how I wanted this thing to work I knew I wanted all-new hydraulics for it says Marah I totaled up all the cylinders hoses motors and valves and told my wife I was going to max out her credit card when I ordered it all I figure I have about $3 000 in it of which $2 500 is for hydraulics Other than welding rod everything else came out of the junk pile
The frame for the wagon is from an old trailer house The engine is from an old Hercules air compressor the breather is from a Massey Ferguson combine and the radiator is from a Plymouth Voyager The front and rear running gears transfer case and transmission are from 1950 s and 1960 s IH trucks The rear axle was flipped upside down to reverse the ring gear so both axles would go in the same direction
The Shaver post driver is a tractor 3-pt mount which Marah modified significantly He moved the down pressure spring from the rear to the sides added supports and a weight box and mounted it inside a pipe framework so he could lift it up to accommodate up to 10-ft posts Military surplus gas cans serve as a fuel tank and cut open also serve as toolboxes
One of the biggest challenges was figuring out the hydraulic flow The 20 hp 4-cyl Hercules engine combined with the 14-gal hydraulic pump meant there was no hydraulic pressure to spare Marah knew the post driver had to be the last valve in the line as the out-flow had to be larger than in-flow to accommodate the release of the weighted head The larger out-flow hose had to return to the reservoir The other problem was steering which required a very low flow
The first valve directed hydraulic flow to the drive; the second went to auxiliary hydraulics on the rear explains Marah The next valves in the line are for steering but ahead of them I had to put a flow control valve and an excess fluid bypass
Once past the steering valves the steering and the excess lines rejoin and full pressure is directed to the post driver portion of the vehicle Here again the flow is directed through a series of valves including the cylinder that moves the driver from the left side of the rig to the front as it extends This required a 1/4 round steel base for it to ride on
I figured out how big an arc I would need and drew a chalk line on the floor of my shop recalls Marah I got out equal lengths of 3/16-in thick 4-in angle iron and made a cut every 8 to 10 in in one face and bent the other face away from the cut What I ended up with was 8 to 10 flat faces rather than a true arc
Marah then welded in bits of metal to fill the gaps that had opened The welded face became the lip the post driver mount arm traveled on while the uncut face became the base
I knew the base needed to be stronger and I knew it would take a lot of beating from the driver he says
The arm itself is a length of 4-in steel tubing with a 3 1/2 in length inside it to provide telescoping action thanks to yet another cylinder Marah mounted L-shape brackets on the 4-in tubing that hook under the lip of the arc While the weight of the driver helps hold it down the brackets help take some of the torque off the hinge pins that attach the post driver tower to the arm A third cylinder/valve mounted a few feet above the telescoping arm and attached to the driver tower adjusts pitch
Another cylinder raises and lowers the post driver head Marah modified the head with a box that he filled with punch-out chunks of metal
The added weight makes the post driver act like a dead blow hammer delivering its full force to the post says Marah However attaching the box required moving the down pressure springs to the side This increases the risk to anyone standing near should they break which they do I slipped pvc pipe over them to contain them which it has when they have broken
Marah also added an emergency brake to the transmission to lock the wheels up
The post-driving rig has worked very well for Marah for about 6 years He does acknowledge one change he would make if redoing it I would put in a larger hydraulic pump and a larger motor on the ground drive he says That would increase ground speed significantly As it is if I am going very far I load it on a trailer and haul it
Contact: FARM SHOW Followup Larry Marah 6885 Marsh Rd Norwood Mo 65717 ph 417 746 4129
In low gear it goes so slow you can hardly see the wheels move but it will climb anything the wheels can get footing on he says I ve used it in places I wouldn t take a 4-WD tractor The only way I could improve it is to put tractor treads on the wheels
Once he gets to the general area he can precisely maneuver into position thanks to the two front axles he used and the separate hydraulic cylinders on each set of tie rods
He can turn both sets of wheels in the same direction and crab steer on the diagonal or turn front and back axles in opposite directions to make extremely tight turns He can also steer with either front or back axles and let the other trail
At the job site the post driver can be adjusted across a 90 degree arc from the front of the vehicle to the immediate left Once roughly in the right place Marah can fine tune positioning by telescoping the post driver mount away from the vehicle as needed or tip the post driver at an angle to match the slope he s on Everything is powered hydraulically which is why Marah spent plenty on hydraulics for the rig
When I sat down and figured out how I wanted this thing to work I knew I wanted all-new hydraulics for it says Marah I totaled up all the cylinders hoses motors and valves and told my wife I was going to max out her credit card when I ordered it all I figure I have about $3 000 in it of which $2 500 is for hydraulics Other than welding rod everything else came out of the junk pile
The frame for the wagon is from an old trailer house The engine is from an old Hercules air compressor the breather is from a Massey Ferguson combine and the radiator is from a Plymouth Voyager The front and rear running gears transfer case and transmission are from 1950 s and 1960 s IH trucks The rear axle was flipped upside down to reverse the ring gear so both axles would go in the same direction
The Shaver post driver is a tractor 3-pt mount which Marah modified significantly He moved the down pressure spring from the rear to the sides added supports and a weight box and mounted it inside a pipe framework so he could lift it up to accommodate up to 10-ft posts Military surplus gas cans serve as a fuel tank and cut open also serve as toolboxes
One of the biggest challenges was figuring out the hydraulic flow The 20 hp 4-cyl Hercules engine combined with the 14-gal hydraulic pump meant there was no hydraulic pressure to spare Marah knew the post driver had to be the last valve in the line as the out-flow had to be larger than in-flow to accommodate the release of the weighted head The larger out-flow hose had to return to the reservoir The other problem was steering which required a very low flow
The first valve directed hydraulic flow to the drive; the second went to auxiliary hydraulics on the rear explains Marah The next valves in the line are for steering but ahead of them I had to put a flow control valve and an excess fluid bypass
Once past the steering valves the steering and the excess lines rejoin and full pressure is directed to the post driver portion of the vehicle Here again the flow is directed through a series of valves including the cylinder that moves the driver from the left side of the rig to the front as it extends This required a 1/4 round steel base for it to ride on
I figured out how big an arc I would need and drew a chalk line on the floor of my shop recalls Marah I got out equal lengths of 3/16-in thick 4-in angle iron and made a cut every 8 to 10 in in one face and bent the other face away from the cut What I ended up with was 8 to 10 flat faces rather than a true arc
Marah then welded in bits of metal to fill the gaps that had opened The welded face became the lip the post driver mount arm traveled on while the uncut face became the base
I knew the base needed to be stronger and I knew it would take a lot of beating from the driver he says
The arm itself is a length of 4-in steel tubing with a 3 1/2 in length inside it to provide telescoping action thanks to yet another cylinder Marah mounted L-shape brackets on the 4-in tubing that hook under the lip of the arc While the weight of the driver helps hold it down the brackets help take some of the torque off the hinge pins that attach the post driver tower to the arm A third cylinder/valve mounted a few feet above the telescoping arm and attached to the driver tower adjusts pitch
Another cylinder raises and lowers the post driver head Marah modified the head with a box that he filled with punch-out chunks of metal
The added weight makes the post driver act like a dead blow hammer delivering its full force to the post says Marah However attaching the box required moving the down pressure springs to the side This increases the risk to anyone standing near should they break which they do I slipped pvc pipe over them to contain them which it has when they have broken
Marah also added an emergency brake to the transmission to lock the wheels up
The post-driving rig has worked very well for Marah for about 6 years He does acknowledge one change he would make if redoing it I would put in a larger hydraulic pump and a larger motor on the ground drive he says That would increase ground speed significantly As it is if I am going very far I load it on a trailer and haul it
Contact: FARM SHOW Followup Larry Marah 6885 Marsh Rd Norwood Mo 65717 ph 417 746 4129
To read the rest of this story, download this issue below or click here to register with your account number.