Profit-Boosting Hog System Designed For Smaller Producers
Eighty-year-old Herman Tripp of Paton, Iowa, is considered by many to be the forefather of modern hog confinement thanks to his invention of the farrowing crate (patented in 1947), slatted floors, and his concept of early weaning, which he started in 1946.
Tripp helped to construct hundreds of confinement operations across North America and in nine foreign countries.
But now that his ideas have been used to concentrate hog production into a small number of hog operations, he has come up with a new concept designed to make it profitable again for smaller farmers to raise hogs.
"Our æOne Step System' turns back time, so that small farmers can once again succeed at raising pigs," says Tripp, who has patented his new system and much of the equipment used for it.
The system consists of build-it-yourself 20 by 260-ft. barns which are designed to house fifty 8-ft. sq. "birth to market" pens.
The main idea is to avoid the dangers of moving young pigs from one area to another area, three or four times during their growing period. The birth-to-market pens have removeable farrowing components for sows to farrow in. Once pigs are weaned, both the sows and the farrowing equipment are removed. The young pigs stay in the same pen with their littermates. This allows them to take advantage of the natural immunity they have to the bacteria in their pen, thanks to antibodies given to them by their mother through nursing.
"What you see with the One Step System is very happy pigs; they're never fighting, very friendly, playful, and they gain very fast. That's the way we think pigs should be raised," Tripp says, who adds that hogs raised in his system require virtually no antibiotics.
One important feature of Tripp's system is what he calls the "Filter Floor," a special brand of floor slats, made of fiberglass bars and spaced so that manure is worked through by the pigs' activity, and then cut off cleanly by the edges. The slats are too narrow for a baby pig's foot to slip through and be caught.
In addition, special-designed feeders get pigs weaned fast, and integrated brooder-heaters draw them away from their mothers. Pigs actually wean earlier in his system, says Tripp.
A totally new ventilation system, which includes a 20-ft. tower at the center of the barn, does a better job removing foul air and drying out manure. The tower filters air through water-cooled curtains. Two 1,000-gal. tanks of water provide constant water supply and also serve as a vertical reservoir that, by creating its own water pressure, supplies each pen of pigs with drinking water and cooling, if and when needed.
Maybe the most radical component of Tripp's new system is the way manure is continuously composted, reducing odors and automatically producing a valuable, odorless byproduct that can be applied to crops or sold. Dead animals can be composted right along with the manure.
"I developed the One Step System so smaller farmers can raise pigs faster, cleaner and without using antibiotics," he says. "The One Step System greatly reduces birth to market time - a reduction of one to four weeks. Much labor is also saved by eliminating clean up time since pigs are not moved from building to building. It has taken me about 15 years to bring all of these ideas together in an integrated, patented system."
By not using antibiotics, it's possible to produce "chemical-free" hogs with this system, and Tripp is finding a specialty market for hogs produced in his system. He says sales of the system have really taken off.
"The family type of hog operation is coming back in droves," he says.
Tripp says conventional feeding systems yield hogs with a feed efficiency of about 3 lbs. to one (feed to gain), but the One Step System has increased efficiency to just 2.4 lbs. of feed for every pound of gain.
The system is sold only as a complete unit including the pre-fab building for 50 sows, the various internal components, and a 10 by 50-ft. composting system. The total cost of a One Step System is $120,000.
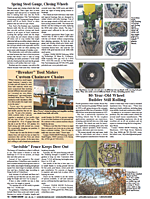
Click here to download page story appeared in.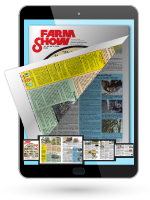
Click here to read entire issue
Profit-Boosting Hog System Designed For Smaller Producers HOG EQUIPMENT & IDEAS Hog Equipment & Ideas 351 Eighty-year-old Herman Tripp of Paton Iowa is considered by many to be the forefather of modern hog confinement thanks to his invention of the farrowing crate patented in 1947 slatted floors and his concept of early weaning which he started in 1946 Tripp helped to construct hundreds of confinement operations across North America and in nine foreign countries But now that his ideas have been used to concentrate hog production into a small number of hog operations he has come up with a new concept designed to make it profitable again for smaller farmers to raise hogs Our æOne Step System turns back time so that small farmers can once again succeed at raising pigs says Tripp who has patented his new system and much of the equipment used for it The system consists of build-it-yourself 20 by 260-ft barns which are designed to house fifty 8-ft sq birth to market pens The main idea is to avoid the dangers of moving young pigs from one area to another area three or four times during their growing period The birth-to-market pens have removeable farrowing components for sows to farrow in Once pigs are weaned both the sows and the farrowing equipment are removed The young pigs stay in the same pen with their littermates This allows them to take advantage of the natural immunity they have to the bacteria in their pen thanks to antibodies given to them by their mother through nursing What you see with the One Step System is very happy pigs; they re never fighting very friendly playful and they gain very fast That s the way we think pigs should be raised Tripp says who adds that hogs raised in his system require virtually no antibiotics One important feature of Tripp s system is what he calls the Filter Floor a special brand of floor slats made of fiberglass bars and spaced so that manure is worked through by the pigs activity and then cut off cleanly by the edges The slats are too narrow for a baby pig s foot to slip through and be caught In addition special-designed feeders get pigs weaned fast and integrated brooder-heaters draw them away from their mothers Pigs actually wean earlier in his system says Tripp A totally new ventilation system which includes a 20-ft tower at the center of the barn does a better job removing foul air and drying out manure The tower filters air through water-cooled curtains Two 1 000-gal tanks of water provide constant water supply and also serve as a vertical reservoir that by creating its own water pressure supplies each pen of pigs with drinking water and cooling if and when needed Maybe the most radical component of Tripp s new system is the way manure is continuously composted reducing odors and automatically producing a valuable odorless byproduct that can be applied to crops or sold Dead animals can be composted right along with the manure I developed the One Step System so smaller farmers can raise pigs faster cleaner and without using antibiotics he says The One Step System greatly reduces birth to market time - a reduction of one to four weeks Much labor is also saved by eliminating clean up time since pigs are not moved from building to building It has taken me about 15 years to bring all of these ideas together in an integrated patented system By not using antibiotics it s possible to produce chemical-free hogs with this system and Tripp is finding a specialty market for hogs produced in his system He says sales of the system have really taken off The family type of hog operation is coming back in droves he says Tripp says conventional feeding systems yield hogs with a feed efficiency of about 3 lbs to one feed to gain but the One Step System has increased efficiency to just 2 4 lbs of feed for every pound of gain The system is sold only as a complete unit including the pre-fab building for 50 sows the various internal components and a 10 by 50-ft composting system The total cost of a One Step System is $120 000 Contact: FARM SHOW Followup The One Step Corporation Herman an
To read the rest of this story, download this issue below or click
here to register with your account number.