You have reached your limit of 3 free stories. A story preview is shown instead.
To view more stories
(If your subscription is current,
click here to Login or Register.)
"Cold Process" Biodiesel
Steve Veenstra says his cold evaporation process for making biodiesel is the lowest cost and easiest way there is to make biodiesel at home. He has made and burned some 4,000 gal. in fuel oil furnaces and in his 7.3-liter diesel F-250 pickup.
"I did nothing to modify the engine, and it works great," says Veenstr
..........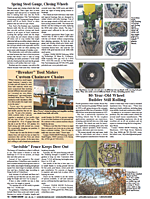
You must sign in, subscribe or renew to see the page.
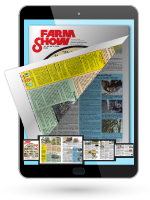
You must sign in, subscribe or renew to see the flip-book
"Cold Process" Biodiesel ENERGY Alternative Fuels 33-1-42 Steve Veenstra says his cold evaporation process for making biodiesel is the lowest cost and easiest way there is to make biodiesel at home. He has made and burned some 4,000 gal. in fuel oil furnaces and in his 7.3-liter diesel F-250 pickup.
"I did nothing to modify the engine, and it works great," says Veenstra. "I think it runs even quieter due to the extra lubrication in the biodiesel."
Veenstra developed the process to reduce the amount of time he had to put into making biodiesel. The process also eliminates the need for water to "wash" the biodiesel, so there are no wastewater issues. Another savings comes from reduced heating during the process. The only use of power for heating is to preheat the vegetable oil to 125 degrees in an old water heater before it's moved to the reactor. The elimination of heat during the reactor stage also allows Veenstra to use poly tanks which let him visually check progress as fuel is made.
Veenstra says he currently makes 40 gal. in about 42 hrs., with only 2 1/2 hrs. of that time as actual physical labor. The rest of the time he doesn't even need to be in the area. His process eliminates many of the steps required to remove impurities in a standard process. With cold evaporation, Veenstra says, simply removing the methanol with his cold evaporation process causes impurities to drop out of suspension.
"Residual heat in the oil after pumping it out of the reactor tank pulls some of the methanol out of the raw biodiesel as it settles." he explains. "Additional steps in my process pull out about two liters of the methanol right away, and the rest evaporates gradually, thanks to a combination of spraying the surface, agitation and bubbling air through the liquid."
He says spraying the surface keeps surface tension down, encouraging evaporation. The bubbler and fan run in the evaporation tank for 24 hours, followed by a minimum of four hours of resting while the final suspensions drop out.
"My evaporation tank is designed to let the suspensions out before pumping the biodiesel out," explains Veenstra. "The biodiesel passes through a 10-micron filter and then a 1-micron bag filter to ensure quality."
He has also developed a simple system for making the methoxide for use in the reactor. He uses nitrogen gas to force methanol into a closed mixing tank with the lye to produce the methoxide, thereby avoiding mixing it by hand.
Veenstra has developed plans and tutorials for his no-wash finishing cold evaporation system and also for his biodiesel production system with its closed methoxide mixing system.
Contact: FARM SHOW Followup, Steve Veenstra, 7420 Parmalee Rd., Middleville, Mich. 49333 (ph 616 240-9227; svp@iserv.net; www.svmade.com).
To read the rest of this story, download this issue below or click
here to register with your account number.