You have reached your limit of 3 free stories. A story preview is shown instead.
To view more stories
(If your subscription is current,
click here to Login or Register.)
Farm Shop Made With Highway Guardrails
Richard Stephens built a 40 by 60-ft. shop using 14 and 26-ft. long sections of highway guard rails for the framework.
"A guy stopped by offering used guard rails for sale when a local highway was being rebuilt. I bought a few, thinking I would use them for cattle feeder skids," recalls Stephens. "After looking
..........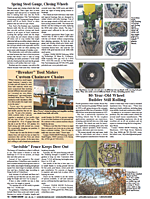
You must sign in, subscribe or renew to see the page.
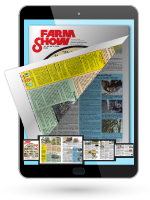
You must sign in, subscribe or renew to see the flip-book
Farm Shop Made With Highway Guardrails FARM SHOP Miscellaneous 33-1-39
Richard Stephens built a 40 by 60-ft. shop using 14 and 26-ft. long sections of highway guard rails for the framework.
"A guy stopped by offering used guard rails for sale when a local highway was being rebuilt. I bought a few, thinking I would use them for cattle feeder skids," recalls Stephens. "After looking at them a while, I ordered a whole load."
He welded them together back-to-back, which created a natural set of flanges. Stood on end, they created ideal surfaces to bolt cross members before putting on siding.
Putting up the shop was not simply a matter of welding guardrails into girders, however. Stephens designed a truss system that he assembled on the ground. It consisted of guard rails, 10-in. dia. log rafters and 2 by 6's for roof braces.
To create strength in the girders and in sidewall braces, splices were always overlaid. In the case of the girders, to get the 40-ft. span, Stephens used four 26 ft. guardrails, i.e. a 26-ft. rail was welded face to face with a 14-ft. rail. Then a second 26-ft. rail was butted to the 14-ft. rail with a second 14-ft. rail butted to the first 26-ft. rail. Once butts and seams were welded, Stephens had an extremely strong 40-ft. beam. Gusset plates made from 3/16-in. steel plate were welded over the seams. They extend up to act as anchor points for vertical supports.
Six trusses were assembled on the ground. Each truss consisted of two uprights, a span, a center post, two rafters and two mid point supports. Stephens then poured cement piers for each upright with steel rebar in it and extending to the surface, where a faceplate was welded in place.
When the first truss was lifted into place, he discovered the weight of the rafters was too great. It bent the gusset plates. He then reinforced each truss where the log rafters and their supports met the guardrail girders.
As additional trusses were lifted into place, Stephens began attaching the 2 by 8-in. sidewall supports, bolting them to the facing flanges. The 2 by 8-in. boards were also spliced with a length of 2 by 8-in. board overlaid and spiked to both ends.
Stephens trimmed 3 1/2-in. poles for roof purlins, giving them a flat top for the metal roof to be attached. These were nailed to the rafters. Before the center beam was lifted into place, it was notched to receive the ends of rafter end gusset plates.
"Once we covered the sides and roof with metal, it looked no different than a commercial steel building," says Stephens. "It has stood up well to high winds, and the trusses support a lot of weight."
Contact: FARM SHOW Followup, Richard Stephens, 14400 N Rock Creek Lane, Haines, Oregon 97833 (ph 541 856-3429).
To read the rest of this story, download this issue below or click
here to register with your account number.