You have reached your limit of 3 free stories. A story preview is shown instead.
To view more stories
To view more stories
SUBSCRIBE OR RENEW NOW
(If your subscription is current, click here to Login or Register.)2008 - Volume #32, Issue #6, Page #32
[ Sample Stories From This Issue | List of All Stories In This Issue]
"Like New" Rebuilt SP Bale Wagon
When Stuart Wilson and Jeremy Tempel went looking for a new self-propelled bale wagon, they quickly learned they'd have to shell out about $150,000. Instead, they bought a used mid 1970's New Holland self-propelled wagon and completely rebuilt it.The two men operate a custom baling business in which t..........
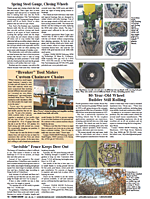
You must sign in, subscribe or renew to see the page.
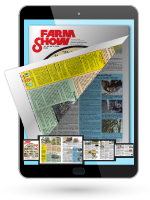
You must sign in, subscribe or renew to see the flip-book
Like New Rebuilt SP Bale Wagon WAGONS/TRAILERS Miscellaneous When Stuart Wilson and Jeremy Tempel went looking for a new self-propelled bale wagon they quickly learned they d have to shell out about $150 000 Instead they bought a used mid 1970 s New Holland self-propelled wagon and completely rebuilt it
The two men operate a custom baling business in which they sell small square bales mostly to the horse market Much of the original wagon was worn out so bad there was almost nothing left There were a lot of parts that we couldn t buy from New Holland so we had to make them ourselves Now it looks much like a modern bale wagon says Wilson of Glenpoll Oklahoma We spent a total of about $10 000 including the $2 400 purchase price
They went online to find the self-propelled New Holland 1048 bale wagon which was equipped with a cab and bale pickup on front and powered by a 361 cu in Ford V-8 engine The seller wanted to part the wagon out but Wilson offered to buy the entire machine He then drove to Moses Lake Wash and hauled the wagon home on a trailer behind his pickup The two men worked on the wagon all winter and finished rebuilding it last June
The bale pickup was almost completely worn out We spent three weeks grinding and rebuilding the pickup s frame and another week rebuilding the mouth where the bale pickup attaches to the wagon says Wilson
The arms that raise and lower the pickup were broken so they rebuilt them The arms have to be exactly located and their pivot angle has to be perfect so it took quite a while to get all the geometry just right says Wilson
They also welded up all the cracks in the cab and repainted it And they rebuilt the engine
The wagon was originally equipped with thin plywood sides which were replaced with horizontal lengths of 2 by 6-in channel iron They built a new tine arch at the front end of the wagon that keeps bales from falling forward off the wagon once it s full
A rolling rack with steel tines is used to group 12 bales together and then roll them to the back of the wagon The rack was originally controlled by a spring and cable return system but it was worn out so they replaced the system with a 6-ft long hydraulic cylinder
The radiator was originally mounted between the cab and pickup where the screen could easily get clogged up with hay and grass The radiator fan was shaft-driven and didn t do a good job of cooling the engine so they replaced it with a radiator off a Ford F-350 pickup They moved the radiator to one side of the wagon on back where the fuel tank was originally mounted They also mounted an electric fan to provide better cooling The electric fan always runs at full speed whether the engine is idling or going at full throttle says Wilson
They moved the fuel tank to the opposite side of the wagon just ahead of the rear wheel
The wagon s hydraulic system was still in good shape However every moving part and every bearing on it was worn out says Wilson We had to make our own bearings and bushings for all the pivot points on the table and pickup There were a lot of parts that we couldn t buy from New Holland
The wagon s flatbed is designed to tilt down to the ground and has four big tines on back A push-off foot is used to push the bales back off the tines
They stack the bales outside a barn and later use a home-built loader-mounted bale clamp to move them into the barn It grabs 12 bales at a time and can stack them up to 14 ft high We need a small tractor to get into the barn but all the commercial bale clamps were too heavy for our Massey Ferguson 243 50 hp tractor says Wilson The entire clamp weighs only about 350 lbs It s the same size as commercical bale clamps but weighs a lot less
The clamp s arms are made from 2 by 6 14-ga C-channel welded together to make a 4-sided tube It s real thin but it s very strong says Wilson The bale clamp arms pin onto the loader arms A single cylinder is connected to four shafts that make all the hooks turn together at the same time Two more cylinders are used to pivot the arms
We spent about $1 200 to build the clamp Commercial ones sell for about $4 000 notes Wilson
Contact: FARM SHOW Followup Stuart Wilson 16701 S 33rd West Ave Glenpoll Okla 74033 ph 918 519-3267; blueskyoklahoma@yahoo com
The two men operate a custom baling business in which they sell small square bales mostly to the horse market Much of the original wagon was worn out so bad there was almost nothing left There were a lot of parts that we couldn t buy from New Holland so we had to make them ourselves Now it looks much like a modern bale wagon says Wilson of Glenpoll Oklahoma We spent a total of about $10 000 including the $2 400 purchase price
They went online to find the self-propelled New Holland 1048 bale wagon which was equipped with a cab and bale pickup on front and powered by a 361 cu in Ford V-8 engine The seller wanted to part the wagon out but Wilson offered to buy the entire machine He then drove to Moses Lake Wash and hauled the wagon home on a trailer behind his pickup The two men worked on the wagon all winter and finished rebuilding it last June
The bale pickup was almost completely worn out We spent three weeks grinding and rebuilding the pickup s frame and another week rebuilding the mouth where the bale pickup attaches to the wagon says Wilson
The arms that raise and lower the pickup were broken so they rebuilt them The arms have to be exactly located and their pivot angle has to be perfect so it took quite a while to get all the geometry just right says Wilson
They also welded up all the cracks in the cab and repainted it And they rebuilt the engine
The wagon was originally equipped with thin plywood sides which were replaced with horizontal lengths of 2 by 6-in channel iron They built a new tine arch at the front end of the wagon that keeps bales from falling forward off the wagon once it s full
A rolling rack with steel tines is used to group 12 bales together and then roll them to the back of the wagon The rack was originally controlled by a spring and cable return system but it was worn out so they replaced the system with a 6-ft long hydraulic cylinder
The radiator was originally mounted between the cab and pickup where the screen could easily get clogged up with hay and grass The radiator fan was shaft-driven and didn t do a good job of cooling the engine so they replaced it with a radiator off a Ford F-350 pickup They moved the radiator to one side of the wagon on back where the fuel tank was originally mounted They also mounted an electric fan to provide better cooling The electric fan always runs at full speed whether the engine is idling or going at full throttle says Wilson
They moved the fuel tank to the opposite side of the wagon just ahead of the rear wheel
The wagon s hydraulic system was still in good shape However every moving part and every bearing on it was worn out says Wilson We had to make our own bearings and bushings for all the pivot points on the table and pickup There were a lot of parts that we couldn t buy from New Holland
The wagon s flatbed is designed to tilt down to the ground and has four big tines on back A push-off foot is used to push the bales back off the tines
They stack the bales outside a barn and later use a home-built loader-mounted bale clamp to move them into the barn It grabs 12 bales at a time and can stack them up to 14 ft high We need a small tractor to get into the barn but all the commercial bale clamps were too heavy for our Massey Ferguson 243 50 hp tractor says Wilson The entire clamp weighs only about 350 lbs It s the same size as commercical bale clamps but weighs a lot less
The clamp s arms are made from 2 by 6 14-ga C-channel welded together to make a 4-sided tube It s real thin but it s very strong says Wilson The bale clamp arms pin onto the loader arms A single cylinder is connected to four shafts that make all the hooks turn together at the same time Two more cylinders are used to pivot the arms
We spent about $1 200 to build the clamp Commercial ones sell for about $4 000 notes Wilson
Contact: FARM SHOW Followup Stuart Wilson 16701 S 33rd West Ave Glenpoll Okla 74033 ph 918 519-3267; blueskyoklahoma@yahoo com
To read the rest of this story, download this issue below or click here to register with your account number.