2008 - Volume #32, Issue #5, Page #04
[ Sample Stories From This Issue | List of All Stories In This Issue | Print this story
| Read this issue]
Zero Turn Swather Mower Fitted With Two Decks
![]() |
![]() |
"We have between six and seven acres to mow, and I can do it in less than two hours," says Ivers. "There's only a couple of things I would change."
One thing he wouldn't change is the simplicity of the rig, including how the two 60-in., 3-pt. hitch mounted finish mowers are mounted. If he wants to use one on a tractor, all he does is reverse the gearbox, pull a couple of pins and it's ready to go. The 10-ft. cut overlaps the wheel width on the swather, so he can trim within 4 in. of a building. He especially likes the hydrostatic drive on the old swather and what that lets him do.
"I can come right up to within a couple of inches of a tree and stop," he says.
Ivers started with a 400 Versatile swather he picked up for about $800. The new deck mowers cost him about $1,500 each. Other parts and steel ran another $700. Modifications to the swather were limited to removing the cab and header table and moving the rear wheel.
"The rear wheel was offset to the side of the windrow," explains Ivers. "Centered, the swather works just like a zero turn mower."
The frame the mowers hang from is 4-in. sq. tubing that Ivers mounted to a new header table pipe. The frame is designed to be at the same level as the drive wheel hubs. The front beam runs at an angle from left to right with the right side about twice the length of the left. This let him hang one ahead of the other so they overlap left to right.
"One change I would make is to set the two decks closer front to rear," says Ivers. "When driving straight or turning right, they overlap fine; however, when turning left they leave a skip."
To hang the mowers, he made a U-shaped bracket. The open end attaches to the frame, while the bottom end fits over one of the 3-pt. hitch pins at the front of the mower decks. This allows the mower to ride freely up and over bumps. At the rear of the deck, a second deck bracket is hooked to the frame with a short chain. This serves to keep the mower parallel to the frame when Ivers uses the swather hydraulics to lift the mowers for transit or maintenance.
To drive the mowers, Ivers used two double belts off a 2,200-rpm, 6-in. pulley on the motor to 12-in. pulleys to either side of the swather. They reduce drive speed to 1,100 rpm's. Because of the type of gearbox on the mowers, Ivers had to not only reverse the direction of their pto mount, but also their rotation. To do so, he mounted steering planetary gearboxes from another swather on the 400. The planetary gears have a ratio of 2.1 to 1, further reducing the drive speed to 540 rpm's on the pto shaft to the mowers.
To get the right heights for the pto shafts, Ivers mounted lengths of channel iron to the frame of the 400. He then attached pillow blocks to hold the shafts that run between the planetary gears.
"If I had bought mowers that reversed direction of rotation, I could have skipped the planetary gears and had room to go direct from that 6-in. pulley to a 24-in. pulley to get the reduction in speed," notes Ivers.
Contact: FARM SHOW Followup, John Ivers, P.O. Box 131, Milo, Alberta, Canada T0L 1L0 (ph 403 599-3874).
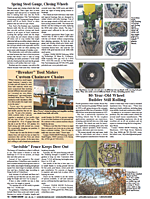
Click here to download page story appeared in.
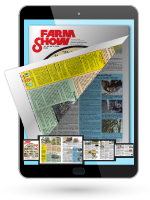
Click here to read entire issue
To read the rest of this story, download this issue below or click here to register with your account number.