You have reached your limit of 3 free stories. A story preview is shown instead.
To view more stories
(If your subscription is current,
click here to Login or Register.)
He Turns Waste Sheet Rock Into Cash
Jim Kramer makes money on both ends when recycling waste wallboard. On the one end, his suppliers pay him $15/ton to haul away the raw product. On the other end, his customers pay him $29/ton for the ground-up product with the paper backing removed. It's used as a gypsum fertilizer and soil amendment and can even reduc
..........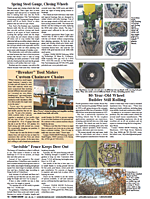
You must sign in, subscribe or renew to see the page.
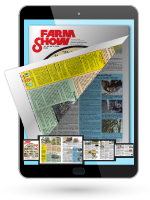
You must sign in, subscribe or renew to see the flip-book
He Turns Waste Sheet Rock Into Cash SPECIALTY/SERVICES Specialty/Services 31-6-9 Jim Kramer makes money on both ends when recycling waste wallboard. On the one end, his suppliers pay him $15/ton to haul away the raw product. On the other end, his customers pay him $29/ton for the ground-up product with the paper backing removed. It's used as a gypsum fertilizer and soil amendment and can even reduce odor and bacteria from manure and control flies.
"It has 20 to 22 percent calcium and 14 to 17 percent sulfur," explains Kramer. "The calcium will mellow up the soil and take out salts. And, it's an economical source of sulfur."
The Brooklyn, Wis. farmer is so busy recycling wallboard he has cut back on acres farmed. When he and a partner first started the business 11 years ago, they didn't know if they had a market or could make any money on it.
Kramer eventually bought out his partner and continued slowly building business. It was easy to get suppliers interested, even though he would only accept brand new scrap that was free of nails, screws and other junk. Construction companies and carpenters were happy to dump the scrap at Kramer's farm for his $15/ton rate versus $36/ton at the landfill. Processing the sheet rock inexpensively and finding customers was the big challenge.
"We didn't want to stick a lot of money into it, so we designed all the equipment ourselves," he says. "All the equipment is based on farm equipment."
The equipment consists of an industrial loader, a Knight "Slinger" side unloading manure spreader, a roller/crusher, a screener, and conveyors. A tractor pto powers the Knight spreader, and an old combine engine provides hydraulic power for hydraulic motors on the roller, screener and various conveyors.
Wallboard scrap is stored in a hoop building before being dumped into the spreader. Cast iron hammers break up the wallboard, knocking much of it off the paper. It also "slings" it against a hood that directs it into a conveyor which carries the pieces to the crusher.
The crusher consists of two steel drums about 8 to 10 in. in diameter and 2 1/2 ft. long with beads welded on them for a rough surface. A slight speed variance between the two helps grind wallboard chunks into powder and pieces fine enough to fall through a 1/4-in. screen.
"The screener is a 6-ft. dia., 12-ft. long drum," explains Kramer. "The powder and small chunks fall through onto a rubber belt and then to a conveyor and a hoop building for storage, while the paper goes out the end."
The screener is important to quality control for customer satisfaction with ease of application and consistency. "We recommend that customers use a crop consultant and do soil testing so you don't over spread," he says.
Based on research conducted at the University of Wisconsin, Kramer applied for and received a patent on the use of gypsum for odor control.
"The gypsum ties up the ammonia, eliminates the odor and adds value to the manure," says Kramer. "It turns it into ammonia sulfate, which is slow-release nitrogen."
Unlike other manure amendments for odor control, the gypsum stays in suspension in slurry tanks and in pits.
The research, market preparation and quality control are working. Recent newspaper coverage has spread the word with an increasing amount of product going to livestock farmers for odor control. For the first time Kramer has had to search for new suppliers of scrap as demand is eating up supply. His low cost processing helps too.
"I had a call from a farmer who was getting gypsum delivered, and my price was about a third less than he was paying," says Kramer, who also encourages other people to enter the business in other parts of the country. "If anybody wants to get in the business, they are welcome to call."
Contact: FARM SHOW Followup, Gypsum Recycling, Inc., W2298 Hwy 92, Brooklyn, Wis. 53521 (cell ph 608 225-1802; fax 608 424-1920).
To read the rest of this story, download this issue below or click
here to register with your account number.