2007 - Volume #31, Issue #4, Page #35
[ Sample Stories From This Issue | List of All Stories In This Issue | Print this story
| Read this issue]
Portable "Scissor" Greenhouse
![]() |
![]() |
![]() |
They had looked into "hoophouse kits," but opted to design and build their own moveable greenhouses, which they've now been using for about six years.
Though they admit they're "not fancy," the structures allow the couple to plant their vegetable crops earlier, and then extend the other end of the growing season as well, harvesting a second crop. The plastic tunnels protect plants from wind, and when used with a fabric row cover over the plants they get extra cold protection.
"Hoophouse kits are stationary and require a foundation, so you can't move them away from bug or disease problems that may occur," Eugene says. "They're also very expensive."
Instead, the Goodmans came up with what they call "scissor hoophouses."
"You can move them sideways because the pieces are light enough that they can be lifted," he explains. "You can lift them over plants without crushing them."
"We have four 50 by 4-ft. beds under the scissor hoophouses, and it only took me about a day to make them from scratch when we first started," Eugene says. "It takes me only about two hours to set up a 100-ft. tunnel."
Goodman's greenhouse design doesn't require perlins. He made each metal hoop using two 10-ft pieces of electrical conduit, bent in a mirror image of each other. Then, he connects them together at the top, using an electrical conduit connector.
Then he placed two of these hoops together at an angle to each other, so that their "straight sides" formed "scissor-like legs." Goodman connected the legs with U-bolts, about halfway up the sides. (The adjustable angle formed between the two hoops determines the height of the greenhouse. Goodman sets his up so the legs are three feet apart, and this creates a 7-ft. tall structure, which is freestanding at this point.)
To prevent the scissors from opening and closing under pressure, Goodman drives a 2-ft long, 3/8-in. rebar brace into the ground one foot deep, at the base of each scissor leg.
He then places a 4-in. long piece of 2 by 4 wood with a hole drilled in it, over top of each rebar brace, and slides it down until it sits on the ground. Goodman then lifts up the foot of the hollow electrical conduit hoop and sets it over the top of the rebar, sliding it down so it's sitting on the wood.
Once a series of hoops has been set up with one foot of space between them, the plastic is dragged over the top.
The block of wood against the ground surface prevents the hoop legs from being driven into the ground by natural forces such as wind or weight from snow. The Goodmans have found that strong winds can actually push the wood into the ground, flush with the surface, which loosens the plastic a bit.
The Goodmans use 24-ft. wide plastic sheeting so there's a little extra sticking out on the sides to bury under 4 to 6 in. of dirt.
"It's important to keep the plastic pulled tight over the hoops." Eugene says. "The scissor hoophouses sort of look like caterpillars when you get them set up. We reuse our plastic each year with this system."
The couple has used up to 13 of these scissor structures to make a 100-ft. long tunnel.
"I don't suggest making them more than 100 ft. long if you want acceptable air circulation," he says. "We use them in the spring until the air gets warm enough to remove the plastic. To move them, I generally close the scissors and take them up and over the plants, then set them down and open them up again. As long as the two feet on each side are attached to the ground, they won't open up any more and they'll support a fair amount of weight."
Goodman says he spent a total of about $300 on materials to build the system, and it quickly paid for itself.
"Conduit and plastic prices have gone up significantly since then, so I think it would be about $600 now to build what we have," he says.
Contact: FARM SHOW Followup, Boulder Belt Eco-Farm, Eugene Goodman, P.O. Box 593, Eaton, Ohio 45320 (ph 937 456-9724; goodows@infinet.com; www.boulderbeltfarm.com).
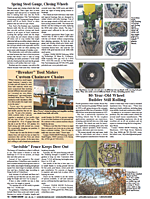
Click here to download page story appeared in.
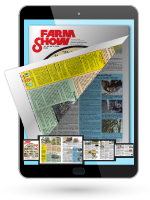
Click here to read entire issue
To read the rest of this story, download this issue below or click here to register with your account number.