2007 - Volume #31, Issue #2, Page #35
[ Sample Stories From This Issue | List of All Stories In This Issue | Print this story
| Read this issue]
Grass Seed Harvester "Sweeps" Seed From Plants
![]() |
"Very few modifications are required on the Massey 300 because of the way the unit was designed," Ray says. "The back end of the combine has a seam about 3 ft. up, where the threshing mechanism is. The body has a split right there, so it was easy to strip off the hopper and all the threshing mechanisms. Then, for strengthening, we bolted in a couple pieces of 4-in. channel iron."
To keep the whole unit in balance, the McDougalds needed to replace the weight that was lost when they stripped the back end down. They did so by sliding a 110-gal. water tank in the bottom where the sieves were. It's multi-purpose, as it also provides a water source for fire fighting, if need be.
"When operating mechanical equipment, there's always a risk of fire, and we harvest this grass seed on large tracts of grazing land. If we had a problem, we could be 10 miles from any source of water.
Next, the brothers bolted an 8-ft. long pickup truck box on top of where the hopper and threshing mechanism had been. They added 4-ft. plywood sides to the box.
"The tailgate opens up so that when we're full, we can transfer the seed into a 3-ton truck, using a pitch fork or scoop shovel," Ray explains.
Modifying the front end of the combine was pretty simple, too. The brothers removed the cutterbar and replaced it with a piece of 2 7/8-in. drill stem for reinforcement.
They removed the reel and, in its place, mounted a 28-in. dia. brush (with approximately 10-in. bristles) similar to a street sweeper brush, but not as dense. They had it custom made by a brush company in Calgary, Alberta.
"The bristles run about 1 in. above the drill stem," Ray points out. Once the seed hits the brush, they go up the feederhouse and the cylinder shoots them into the box, just like if you were harvesting a cereal crop."
The McDougalds harvest in pretty rough terrain (virgin ground that's never been broken up), so at times operating speed can be quite slow. However, on smoother, open country, their harvest speed is similar to that of most grain harvesting.
"With a 12-ft. header, it's a small enough combine that it's actually a nimble little outfit," Ray points out. "Visibility is extremely good."
The major expense was the brush, which cost approximately $2,000. Everything else was salvaged.
The McDougalds harvest spear grasses such as "western porcupine" and "needle and thread". They also harvest "rough fescue," but it only sets seed about twice in a 10-year period, according to Ray.
Seed harvesting doesn't hurt the existing grass stand because there's plenty of seed that doesn't get collected.
"We're lucky if we get a quarter of the total seed production because the heads of native grass plants don't mature all at the same time," Ray explains. "We harvest in early July, before putting the cattle on it for a few weeks."
The McDougalds wholesale their seed to retailers who blend them for reclamation projects across the southern prairies. They say it's a limited and somewhat unpredictable market.
The brothers' grass seed harvester worked so well, they made another one from a Massey combine. Together with another seed harvester they bought, which mounts on the front of their tractor, they can cover a lot of acres.
Contact: FARM SHOW Followup, Ray McDougald, P. O. Box 1839, Maple Creek, Sask., Canada S0N 1N0 (ph/fax 306 662-2963; rmcdougald@sasktel.net).
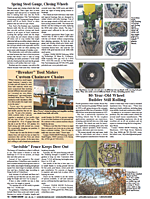
Click here to download page story appeared in.
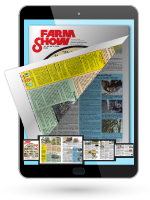
Click here to read entire issue
To read the rest of this story, download this issue below or click here to register with your account number.