You have reached your limit of 3 free stories. A story preview is shown instead.
To view more stories
(If your subscription is current,
click here to Login or Register.)
Gas-Fired Big Boiler Modified For Wood
Tom Harmon wanted an outside wood furnace to heat his house and provide hot water. Already equipped with a closed loop geothermal heat pump that used well water, Harmon felt a commercial wood furnace would be too expensive to justify. When he got his hands on an old 350-gal. conventional boiler, he figured he was halfw
..........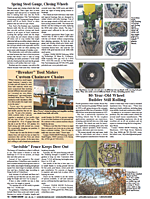
You must sign in, subscribe or renew to see the page.
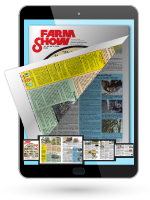
You must sign in, subscribe or renew to see the flip-book
Gas-Fired Big Boiler Modified For Wood ENERGY Miscellaneous 30-5-10 Tom Harmon wanted an outside wood furnace to heat his house and provide hot water. Already equipped with a closed loop geothermal heat pump that used well water, Harmon felt a commercial wood furnace would be too expensive to justify. When he got his hands on an old 350-gal. conventional boiler, he figured he was halfway home.
"I cut off both ends, took out all the tubes and inserted an 80-gal. air compressor tank for a fire box," says Harmon.
He cut one end off the tank/firebox and ran four 3-in. diameter steel tubes (thin wall sprinkler pipe) through the other end to serve as exhaust outlets. At the front, the firebox mounts to a steel plate with a matching hole. The plate closes off the front of the boiler. Legs left on the rear end of the tank support it inside the boiler.
Once the firebox was installed, a steel plate with holes for the exhaust tubes was mounted at the rear of the boiler. Harmon then boxed in the tubes' ends to make an exhaust chamber. The chamber included a clean out door for ashes at the bottom and a short chimney flue at the top.
"I used 8-in., double-wall, galvanized flue pipe, but it didn't last and will be replaced with stainless," says Harmon. "I built a front door for the boiler and firebox out of 3-in. channel iron covered in 1/4-in. steel. The inside of the door is filled with commercial grade boiler insulation."
The insulation is held in place with chain link fence welded to the back of the door. When the door was filled with insulation and closed, the insulation formed a tight seal with the door.
"It is always cool to the touch," says Harmon.
Strips of 2-in. insulation were double layered to the outside of the boiler, glued in place with high temperature silicone and banded with steel strap. Cracks were filled with spray foam insulation.
The front of the stove extends down 8 in. and out 7 in. from the face of the firebox. Harmon wanted to catch any "spill-outs" when the door is opened. This became especially important once he enclosed the furnace/boiler in an 8 by 11-ft. shed, made from a shipping crate from an MRI machine delivered to a nearby hospital.
"The crate had 6-in. I-beams underneath with 1-in. plywood sidewalls," says Harmon. "All I had to do was build stud side walls, reattach the plywood and build a roof."
A hot water coil mounted at the rear of the firebox, runs to a water heater in the house. When the boiler is operating, the coil provides hot water on demand. If the boiler should cool down, the water heater, which is set low, maintains backup warm water.
A circulating in-line pump moves the boiler water through a loop of 3/4-in. feed and return lines to a coil in the existing ductwork in the house. The lines are insulated and sleeved in 50 ft. of irrigation pipe.
The temperature in the boiler is controlled by a dry-well aquastat that opens the draft door as needed. It is powered by a 110-volt vent motor.
"Water only circulates in the house when the heat pump calls for it," explains Harmon. "We have two thermostats, one that overrides everything that takes care of heat in the house. A second one kicks in the geothermal heat pump when the temperature falls in the boiler."
In the winter the thermostats are set at 160 and 180?. In the summer, they are lowered 20?, still sufficient for hot water.
"The total cost, including the new Mig welder I bought for the project, was less than $2,000," says Harmon. "The firebox works great. Green pine will burn as clean as anything."
Contact: FARM SHOW Followup, Tom Harmon, 2604 Wheeler Lane, Church Road, Va. 23833 (ph 804 265-8658).
To read the rest of this story, download this issue below or click
here to register with your account number.