You have reached your limit of 3 free stories. A story preview is shown instead.
To view more stories
(If your subscription is current,
click here to Login or Register.)
He Built His Own Waste Oil Furnace
"My uncle, John Frankish, runs an auto repair shop here in upstate New York and, about four years ago, he decided to build a waste oil stove to get away from the high price of fuel oil," says Casey Frankish, Hall, New York.
"He first looked into factory-built units but couldn't justify the cost. So he started ex
..........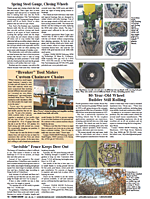
You must sign in, subscribe or renew to see the page.
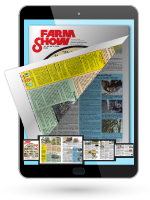
You must sign in, subscribe or renew to see the flip-book
He Built His Own Waste Oil Furnace ENERGY Waste Oil 30-3-4 "My uncle, John Frankish, runs an auto repair shop here in upstate New York and, about four years ago, he decided to build a waste oil stove to get away from the high price of fuel oil," says Casey Frankish, Hall, New York.
"He first looked into factory-built units but couldn't justify the cost. So he started experimenting with different ideas until he found the right combination of air pressure and nozzle types along with a heat exchanger. It has worked out great, with some modifications along the way.
"The current model burns about 10 gal. of waste oil a day. John heats the shop at least five days a week for eight to nine hours a day. His stove easily keeps the shop at 70 degrees no matter how cold it is outside."
The waste oil heater is made from 14-ga. sheet metal and has a 6-ft. long heat exchanger, with a burner at one end. An air compressor is hooked up to the burner. An electric motor belt-drives a squirrel cage fan hooked to a thermostat, which blows air through an L-shaped metal duct and into the heat exchanger. The fan is used to push heat throughout the shop. Heat is blown out of holes cut into the top of the heat exchanger through a curved section of stove pipe.
Oil gravity flows out of a coffee can that Frankish mounted about 4 ft. off the floor.
"It's a simple design, with not much on it to go wrong," says Casey.
"It's amazing how little oil it uses for how much heat it puts out. I think it uses only about half as much oil per heat unit as most commercial models. The key to operating it is to keep the oil at least 70 degrees and the fuel/air mixture set to completely atomize the oil. He fastened a piece of heat tape to the oil line in order to keep the oil warm so that it burns better. The heat exchanger has three holes across the top, and he usually plugs up two of them to keep the shop from getting too hot."
John made his own air nozzle which Casey says "does a great job of atomizing the oil". To make the nozzle he used 1/4-in. dia. copper tubing and used a vise grips to smash the ends down, forming a fish tail for the air to come out of. "It burns so efficiently that even when running at full capacity, there is no smoke, which I find impressive especially considering that it produces about 160,000 to 180,000 btu's per hour. I think this nozzle works twice as well as anything on the market."
It cost John about $1,000 in steel to build the stove but it has paid for itself many times over, says Casey.
Contact: FARM SHOW Followup, John Frankish, 4247 Rt. 247, Stanley, N.Y. 14456 (ph 585 554-4284) or Casey Frankish, P.O. Box 71, Hall, N.Y. 14463 (ph 585 526-6278).
To read the rest of this story, download this issue below or click
here to register with your account number.