You have reached your limit of 3 free stories. A story preview is shown instead.
To view more stories
(If your subscription is current,
click here to Login or Register.)
Do-It-Yourself Oil-Fired Boiler
Joseph Leihgeber doesn't worry about high heating bills since he began heating with his homemade oil-fired boiler. After 12 years of steady heat and low bills, he's sure it's the most economical hot water boiler around. Best of all, it cost him a fraction of a store-bought model.
"It cost less than $500 to build
..........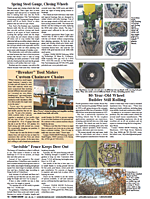
You must sign in, subscribe or renew to see the page.
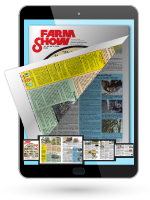
You must sign in, subscribe or renew to see the flip-book
Do-It-Yourself Oil-Fired Boiler ENERGY Alternative Fuels 29-5-32 Joseph Leihgeber doesn't worry about high heating bills since he began heating with his homemade oil-fired boiler. After 12 years of steady heat and low bills, he's sure it's the most economical hot water boiler around. Best of all, it cost him a fraction of a store-bought model.
"It cost less than $500 to build and it's more efficient than a new $2,600 boiler," says Leihgeber. "If a guy can weld, he can build one just like it."
To make his furnace, Leihgeber started out with a 55-gal. metal drum and lined the interior with 3 in. of refractory cement. At the bottom of the combustion chamber, he installed a commercial #2 fuel oil burner with a ceramic brick in front of the burner.
"The brick gets cherry red and makes for almost 100 percent combustion," explains Leihgeber. "The inside of the combustion chamber can reach up to 2,000? and the lining holds that heat."
It is the welded boiler that really sets Leihgeber's oil furnace apart. The 8-gal. water tank rests on a fiberglass rope at the top of the combustion chamber. Sixteen "water" legs extend down from the tank down into the combustion chamber to heat the water. Not only do the legs and the base of the tank provide more than 18 sq. ft. of heat absorbing surface, but the design also reduces maintenance.
"I have put in a lot of burners that are hard to clean, but these pipes hang straight down. If they get a few flakes on them, they fall off and into the chamber," says Leihgeber. "To clean or inspect the boiler, just unscrew two pipe unions and lift the boiler straight up out of the combustion chamber. It takes about two minutes."
While Leihgeber did the welding, he relied on a nearby metal working shop to use plasma cutters to cut out all the water legs. He also bought a commercial grade expansion tank and relief valve as well as all controls.
"This is a low pressure boiler controlled by an automatic water fill," says Leihgeber.
Leihgeber built a small boiler house 20 ft. away from his home to reduce insurance costs. Insulated pipes carry water to and from the boiler. All pipes are foam wrapped and an in-house thermostat controls water circulation. Leihgeber commonly keeps his boiler at 180?, though he can go as high as 220? since it is under pressure.
"My boiler can easily heat a 2,000 sq. ft. building," says Leihgeber. "The unit can be made bigger for larger homes or even apartment buildings just by enlarging the heat absorbing surface and increasing the burner oil nozzle size and the air flow."
Leihgeber can make plans available for a fee.
Contact: FARM SHOW Followup, Joseph Q. Leihgeber, 1815 Bardwell West, Williamsburg, Ohio 45176 (ph 937 444-4835; josephql2@aol.com).
To read the rest of this story, download this issue below or click
here to register with your account number.