2005 - Volume #29, Issue #5, Page #28
[ Sample Stories From This Issue | List of All Stories In This Issue | Print this story
| Read this issue]
Skid Plates Protect Combine Heads
![]() |
![]() |
"I can run the header right on the ground and feel every stone I run over without any damage to the header," he says.
Schwarz's skid plates fit 200 and 900 Series Deere combines, but the idea could easily be adapted to other combine headers. He designed a simple template for fabricating heavy steel skid plates. These plates are installed behind existing poly skid plates standard on most grain headers today.
Template
Step 1. Get under the header with a 1/8-in. thick strip of steel, 3 in. wide and 24 in. long.
"Position the strip under the header, tucking the rear of the strip as far back and above the platform's rear brace tube as possible," says Schwarz. "Using hand pressure, bend the strip to produce a belly of approximately 4 in. in the front half of the template strip. Curve the front end of the strip so it tucks just behind the existing angle iron attaching the stainless steel cutter bar seal."
It is this "belly" that will slide over any rocks and keep them from damaging the under side of the header pan. If the strip is too long after forming the 4-in. bulge, check to be sure the rear end is driven as far back as possible above the rear support tube. If satisfied with the rear positioning, mark the excess, cut it off and try again to fit the front end of the strip just behind the angle iron.
"The template should now fit correctly between each set of cutterbar support arms across the header," says Schwarz.
Step 2. Measure and record the width of each individual pan section under the header. Schwarz points out that they are not all the same width. Measure the distance between support arms, and deduct 1/2 to 3/4 in. from each measurement to allow clearance and "wiggle room" at skid plate installation.
Step 3. Take the template and net width measurements to a metal shop to cut the needed number of skid plates to the proper dimensions and roll-form them to the proper shape.
"The number of plates will vary according to the width of the header," says Schwarz. "I would recommend that 3/16-in. thick, hot rolled plate be used for skid plate fabrication. This thickness can withstand the full weight of the header as it rides over on a field stone."
Installation
Step 1. Remove the two factory-installed carriage bolts and replace with similar Grade-5 quality, but 2-2/12 in. longer carriage bolts. Schwarz warns against using common Grade-2 carriage bolts.
"Stack just enough flat washers on the bolts to cover exposed non-threaded areas on the bolt neck," he adds. "Then reinstall the original flange-style hex nuts removed from the shorter carriage bolts. Tighten the flanged hex nuts against the washers to temporarily secure the bolts in the header pan so they can be used to indicate where bolt holes must be drilled in the new skid plates."
Step 2. Select a skid plate to match the pan width. Center it equally between the two adjacent cutterbar support arms. Slide the rear edge as far back and above the header's rear brace tube as possible. Tap with a hammer to force it as far rearward as possible. Schwarz notes that some skid plates may need corners trimmed or notches added to clear existing header hardware.
"Use a paint stick or other marking instrument to paint two 2-in. diameter circles on top of the skid plate in the approximate area where holes are needed for the carriage bolts," says Schwarz. "Swing the front edge of the plate upward. When the top (painted) side of the skid plate comes in contact with the carriage bolts, the bolt threads will leave a ćwitness mark' where the hole should be drilled."
Also attempt to visually confirm that the front edge of the skid plate will tuck up and just behind the factory-installed angle iron that attaches the cutter bar stainless seal.
Step 3. Remove the skid plate and drill 1/2 to 3/4-in. thru-holes for two carriage bolts using the witness marks for guides.
Step 4. Re-install the skid plate to the header pan over the carriage bolts without removing the previously installed and tightened down hex-nuts and washers. No more than 1/2 to 3/4 in. of carriage bolt thread should protrude through the skid plate. If necessary, lower the plate, remove the hex nuts and add more washers. Reinstall the hex nuts and raise the plate back into position.
“Once the plate is in position, secure it by jamming two locking type hex-nuts on each carriage bolt to cover and protect all the thread,” advises Schwarz. “Just repeat the process for each plate. Steel and metal work shouldn’t cost more than $250 to $300.”
Contact: F ARM SHOW Followup, John J. Schwarz Sr., 5480 S. 1025 E., Hudson, Ind. 46747 (ph 260 908-0366; JSchwarz@cooper standard.com).
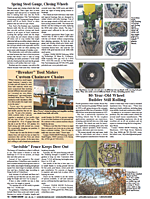
Click here to download page story appeared in.
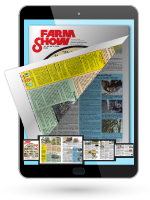
Click here to read entire issue
To read the rest of this story, download this issue below or click here to register with your account number.