2005 - Volume #29, Issue #3, Page #08
[ Sample Stories From This Issue | List of All Stories In This Issue | Print this story
| Read this issue]
Brick Cleaner Quickly Takes Off Old Mortar
![]() |
![]() |
"The beauty of it is its simplicity. My father, who has since passed away, was the brains behind it and I was just the helper."
Carlson says his dad got the idea after an old building burned down and the owner told him he could have all the old bricks for nothing if he hauled them away.
Carlson hired a crew of kids to chip away at the old mortar with hatchets, hammers, and chisels. This was slow, tedious work, so Carlson developed the cleaner. He later sold the cleaned bricks in pallets of 500 each.
His rig looks like a table saw. A 6-in. wide, rotating, dual cutting head comes up and out of a hole in the table. He says, you can use one head at a time, or both at once. "The cutting head is the secret to the whole thing," Carlson says. "Two of them are mounted on a common 1 1/4-in. shaft under the table with bearings on either end."
The cutting heads are comprised of two round plates (3/8-in. thick by 7-in. dia.) joined together by eight 6-in. bolts. Between the plates, each bolt holds about 10 emery wheel cutter heads - they resemble small washers with star points like the tip of a boot spur, and are normally used for dressing up a grinding stone. They are made from extremely hard material and are placed on the bolts with varying numbers of washers to stagger their position on each bolt. As a result, each bolt has a different alignment and it covers the entire brick smoothly.
In the center of the shaft, between the two plates, there's a V-belt pulley. It drops down to the unit's 5-hp gas engine, which drives the whole thing. The arms that hold the bearings and the shaft, all swivel, according to Carlson. At the far end of these two steel arms, two little hand cranks with jam nuts allow you to raise or lower the cutting heads, and tighten them into position.
The 1/4-in. plate steel table has two rectangular cuts in it for the heads to come up through, and there is 1/8-in. angle iron bolted to the tabletop to serve as a cutting guide.
Carlson says the dual cutting heads easily remove old, soft mortar from discarded bricks. "It'll clean 500 bricks per hour," he points out. "We clean all the sides except the facing edge û that's left original."
Carlson says bricks normally come to him with a 1/4-in. layer of mortar on them, and he leaves on "just a little bit of blush." He likes to leave a little of the mortar on them to add color and character, and achieves this effect by not pressing the brick as hard against the head.
You can also make adjustments to the pattern of the emery wheel cutters that will allow you to score the bricks with any pattern you want, making custom designs that are not available commercially.
"Some of the patterns you can make look very nice and are pretty unusual. You can do this on brand new bricks, too," Carlson says. "You never, want to wear gloves or lose clothing when using this machine because it will grab them and you can easily lose fingers."
The machine is only intended for working on the bricks from old, old buildings because that mortar is softer. He says modern mortar is harder like concrete and really wears the machine down fast.
"By putting a sprinkler on the pile of brick you're going to do for about 20 minutes in advance, it makes a lot less dust," he advises. "We wear a dust mask and safety glasses whenever we use it."
Carlson cleans bricks for people, and also rents the unit out. "I'm willing to sell the plans for this unit, so people could either build their own or take them to a machine shop and have it custom made," Carlson says. "All you'd need to build it is a drill press, a lathe and a welder. It'd be a good winter project."
Contact: FARM SHOW Followup, Ted Carlson, 10708 Quartz Valley Rd., Fort Jones, Calif. 96032 (ph 530 468-2975).
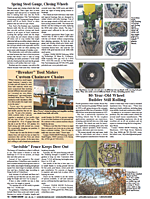
Click here to download page story appeared in.
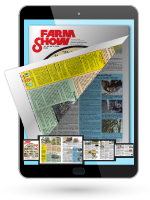
Click here to read entire issue
To read the rest of this story, download this issue below or click here to register with your account number.