2005 - Volume #29, Issue #3, Page #19
[ Sample Stories From This Issue | List of All Stories In This Issue | Print this story
| Read this issue]
Portable Sand And Gravel Seperator
![]() |
He used mostly scrap steel to build the four-legged machine, which looks something like a gravity wagon. It rides on a 20-ft. long tandem axle trailer that Cusack built out of an old mobile home. The machine has a metal hopper on top that measures 8 ft. sq. and 12 ft. high. The hopper is equipped with a screen that sets at an angle and has 1/32-in. dia. holes. Power to vibrate the screen is supplied by a 2 hp electric motor, which belt-drives a commercial vibrating device that he bought from a pickle processing company. It vibrates the screen about 1,000 times per minute.
A front-end loader is used to drop material into the hopper. Sand drops through the screen and falls onto the hopper's slanted floor, then exits through a door on one side of the machine, where a portable bagging machine is used to bag it up.
Gravel flows down a 20-in. wide, 10-in. deep, plastic-lined chute on the other side of the machine and out onto the ground.
A key feature of the machine is the use of springs on all four legs. Each leg sets inside a 4-in. dia. pipe that's welded to a metal base. The pipe is enclosed by a 16-in. long, 4-in. wide spring off a heavy duty truck. Collectively, the springs absorb the shock of the vibrating screens and keeps the machine from shaking up and down too much.
"It works fast and does the work of commercial machines that sell for $100,000 or more," says Cusack. "I was told by some people who work with stationary sand and gravel separators that it couldn't be done, but it runs beautifully. I use it to bag up sand at my own sand and gravel pit. The sand is used to build dikes by local people who live in flood plain areas. I have two bagging machines, one for 25-lb. bags and the other for 50-lb. bags.
"The secret to this machine's success is the use of the springs. The entire upper part of the machine vibrates, but the legs almost float inside the springs. I can hold my hand under the trailer and not even feel it vibrate. "I think the same idea could be used by farmers to process any gravel they may have on their farms. For example, dairy farmers could use the sand for bedding. The hopper can hold up to 1 1/2 yards of sand and gravel at a time. I can bag up to 1,000 bags per day which is a lot of capacity for its size. The door can be raised or lowered by a wheel in order to control the rate at which sand flows through the door. Or, you could process your own play sand or weight sand and sell it commercially. I get about $1.50 to $2 for each bag of sand I sell."
Cusack says the most expensive part of the project was the screens, which have to be specially made. "They're very expensive but they're designed to last a long time," he says.
He uses a big portable generator to operate the electric motor.
The baggers were custom built for him at a cost of $340 apiece. They're open at the top. One person hangs the bags on the bagging machine while another one ties the bags and stacks them on pallets.
Cusack says he's willing to build separator machines for 10 percent over cost.
Contact: FARM SHOW Followup, Patrick Cusack, Quinto Farms, 8572 Borden Road, Muir, Mich. 48860 (ph 989 981-6860; email: agquint@cmsinter.net).
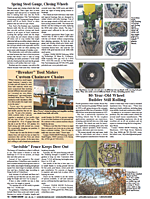
Click here to download page story appeared in.
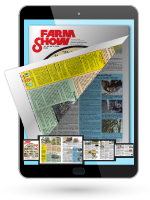
Click here to read entire issue
To read the rest of this story, download this issue below or click here to register with your account number.