Low Cost Air Compressor
 ✖  |
"We use it for all kinds of jobs, such as sandblasting anhydrous tanks, running air tools and cleaning machinery," says David Seifert, 11th grade FFA student at Rice Consolidate High School, Gardwood, Texas, who turned an old pickup engine into a low-cost air compressor.
Here, in his own words, is how he did it: "First, I salvaged a 292 Chevrolet engine from an old pickup. Removing the head, I drilled out the spark plug holes with a 3 in. bit. Then I tapped the holes with a coarse pipe threader and inserted check valves that let compressed air go one way only ù out of the engine.
"I also removed the intake valve springs from the engine head, and replaced them with lighter tension coil springs. This allows air to enter the cylinder block when the crankshaft pulls the piston down. When the piston is pushed up, the pressure closes the intake valve and opens the check valve.
"Next, I took the drive shaft off the old pickup and welded a PTO coupler to one end of the universal joints. This couples to a tractor's PTO to power the compressor.
"I also made a two-wheel trailer from a salvaged Dodge rear axle, and mounted the compressor and a 110-gal. air tank on it. To secure the tank, I bent 1/2 in. steel rods around it and bolted them to the trailer frame.
"Then I fitted the check valves with hydraulic hoses and connected them to a manifold made of plumbing tees. With another piece of hydraulic hose, I connected the manifold, made from the tees, to the tank.
"Next, I removed the exhaust manifold and fitted the intake manifold with a homemade air filter.
"I took off the radiator and the water pump, but to keep the compressor from overheating, I ran a hose from the water drain plug on the side of the block to the fuel pump, and then ran another hose from the fuel pump to the thermostat opening at the top of the engine. The fuel pump circulates water through the hoses and block just enough to cool the compressor.
"I left the transmission on the compressor so we can throw it out of gear without going back to the tractor. We run it in high gear, usually with a 560 International tractor. As a compressor, the engine runs backward.
"Finally, I outfitted the PTO shaft with a safety sleeve made from two different-sized plastic pipes and two plastic containers. The two pipes slide into each other to adjust for length while covering the shaft, and the containers are fiberglassed to the ends to cover the universal joints.
"For further safety, the tank is outfitted with a pop-off valve and a pressure gauge. Total material costs, including engine, trailer, tank and all parts was $387.38.
"The old engine is now a high-volume ù not high-pressure ù compressor. It won a blue ribbon in the mechanical division at the Houston Livestock Show. It'll pump up a 250 gal. tank to 120 lbs. pressure in about 5 min. For sandblasting, it has enough capacity to maintain 100 to 110 lbs. of pressure under load."
David believes a used straight 6 cyl. engine is the best candidate for converting into an air compressor. "You could probably convert an 8 cyl. V-8, using 4 cylinders for compressing air and the other 4 to run the engine. But I'm not sure you'd have enough power."
David suggests going to a machine shop to have the holes drilled out: "I did it by hand and hit the water jacket, which opened up a small water leak into the air tank. Also the hydraulic hoses get pretty hot under load. I'm thinking about replacing them with copper tubing," he told FARM SHOW.
David ordered the intake check valves out of a wholesale motor parts catalog for $4.27 each.
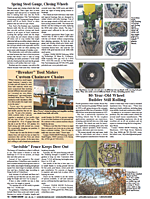
Click here to download page story appeared in.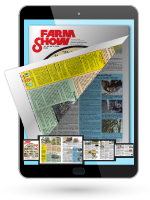
Click here to read entire issue
Low Cost Air Compressor FARM SHOP Tools 7-2-6 "We use it for all kinds of jobs, such as sandblasting anhydrous tanks, running air tools and cleaning machinery," says David Seifert, 11th grade FFA student at Rice Consolidate High School, Gardwood, Texas, who turned an old pickup engine into a low-cost air compressor.
Here, in his own words, is how he did it: "First, I salvaged a 292 Chevrolet engine from an old pickup. Removing the head, I drilled out the spark plug holes with a 3 in. bit. Then I tapped the holes with a coarse pipe threader and inserted check valves that let compressed air go one way only ù out of the engine.
"I also removed the intake valve springs from the engine head, and replaced them with lighter tension coil springs. This allows air to enter the cylinder block when the crankshaft pulls the piston down. When the piston is pushed up, the pressure closes the intake valve and opens the check valve.
"Next, I took the drive shaft off the old pickup and welded a PTO coupler to one end of the universal joints. This couples to a tractor's PTO to power the compressor.
"I also made a two-wheel trailer from a salvaged Dodge rear axle, and mounted the compressor and a 110-gal. air tank on it. To secure the tank, I bent 1/2 in. steel rods around it and bolted them to the trailer frame.
"Then I fitted the check valves with hydraulic hoses and connected them to a manifold made of plumbing tees. With another piece of hydraulic hose, I connected the manifold, made from the tees, to the tank.
"Next, I removed the exhaust manifold and fitted the intake manifold with a homemade air filter.
"I took off the radiator and the water pump, but to keep the compressor from overheating, I ran a hose from the water drain plug on the side of the block to the fuel pump, and then ran another hose from the fuel pump to the thermostat opening at the top of the engine. The fuel pump circulates water through the hoses and block just enough to cool the compressor.
"I left the transmission on the compressor so we can throw it out of gear without going back to the tractor. We run it in high gear, usually with a 560 International tractor. As a compressor, the engine runs backward.
"Finally, I outfitted the PTO shaft with a safety sleeve made from two different-sized plastic pipes and two plastic containers. The two pipes slide into each other to adjust for length while covering the shaft, and the containers are fiberglassed to the ends to cover the universal joints.
"For further safety, the tank is outfitted with a pop-off valve and a pressure gauge. Total material costs, including engine, trailer, tank and all parts was $387.38.
"The old engine is now a high-volume ù not high-pressure ù compressor. It won a blue ribbon in the mechanical division at the Houston Livestock Show. It'll pump up a 250 gal. tank to 120 lbs. pressure in about 5 min. For sandblasting, it has enough capacity to maintain 100 to 110 lbs. of pressure under load."
David believes a used straight 6 cyl. engine is the best candidate for converting into an air compressor. "You could probably convert an 8 cyl. V-8, using 4 cylinders for compressing air and the other 4 to run the engine. But I'm not sure you'd have enough power."
David suggests going to a machine shop to have the holes drilled out: "I did it by hand and hit the water jacket, which opened up a small water leak into the air tank. Also the hydraulic hoses get pretty hot under load. I'm thinking about replacing them with copper tubing," he told FARM SHOW.
David ordered the intake check valves out of a wholesale motor parts catalog for $4.27 each.
To read the rest of this story, download this issue below or click
here to register with your account number.