Performance Boosting Tips From Combine Expert
Combine specialist and performance parts supplier George Kuchar has spent the better part of 35 years working with combines and combine operators across the U.S. and Canada. He gives seminars to combine owners to help them better understand their machines and improve performance. (You can reach Kuchar by phone at 217 854-9838 or by email at kuchar@ctnet.net.)
Kuchar says farmers only have to spend a few days each year and minimal dollars to better maintain their combine, do a better job of harvesting, save repair bills, and make more money from their crops. Kuchar tells farmers attending his combine seminars to go over their machines like a doctor giving a thorough physical. Start the diagnosis, Kuchar says, at the front of the machine, where the sickle meets the grain.
Sickle Timing
Time the sickle in the center of the platform, not on one end or the other. The center section on the head should always stop in the center of the guard. That being done, the sickle will cut uniformly and not tear plant stems and shatter the heads or pods, which can leave 1-2 bushels per acre on the ground.
Reel Setting
Reels are often set too fast or too slow. Either way can shatter grain or cause the platform auger to reject material. Kuchar says his rule of thumb is to set reel speed slightly faster than ground speed. "The reel should look like it's pulling the machine through the field," Kuchar says.
Also, locate the reel as far forward and as high as possible for crop conditions. The fingers should gently tip the crop toward the auger, not lift it or throw it on top of the auger.
Auger Setting
Kuchar says that slowing the auger speed will help it feed material evenly off the sickle. If it runs too fast the material is thrown back toward the sickle and won't move evenly into the auger and the feederhouse. About 130-140 rpm's is the best speed; 170-190 rpm's is too fast. Change the chain sprocket to set the speed.
On many machines, the auger moves more material to the sides of the feederhouse rather than to the center. It should feed evenly across the width of the feederhouse. You can improve infeeding to the machine by removing some of the fingers in the auger. Kuchar suggests removing 3 fingers from each side nearest the edge of the feederhouse to make it feed more evenly. On rotor machines, remove the same number of fingers.
Kuchar says you can look at the paint wear patterns on a new head and tell a great deal about what is happening. On many machines there isn't any wear on the center of the auger, which isn't a good sign. This means that material is feeding too much to the sides and not enough to the center.
Auger Flighting
The main auger should not be sharp to the touch like a knife, it should be smooth on top and sharp on the edges. If it's sharp to the touch, it could be damaging grain as it feeds into the machine. Kuchar recommends grinding the top edge of the auger flat and to also make sure any bends are removed.
Another area to check is the length of the auger flighting. Kuchar says flighting should never extend more than 3 inches past the opening of the feederhouse. If it does, cut the flighting back and material inflow will improve. On pickup headers the length of flighting isn't as critical because the material is already in a swath and not feeding from the sides.
Kuchar says that operators should be careful not to run dirt into their machines. Excessive dirt can cause auger damage in as little as 150-200 hours. Normally auger wear wouldn't occur until 1,200-1,400 hours. Rasp bars and the leading edge of the concave are also subject to abnormal wear when dirt runs into the machine.
Feederhouse
Make sure the chain has the proper tension by checking specifications in the operator's manual. The correct tension should allow you to slide a piece of paper under the chain and remove it without pinching. If the chain is too tight, sprockets and bearings will wear too fast. Chains should run for 2,000 hours or more, but can wear out in only 1,000 hours
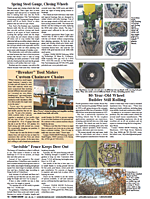
Click here to download page story appeared in.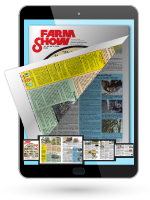
Click here to read entire issue
Performance Boosting Tips From Combine Expert COMBINES Miscellaneous 27-3-32 Combine specialist and performance parts supplier George Kuchar has spent the better part of 35 years working with combines and combine operators across the U.S. and Canada. He gives seminars to combine owners to help them better understand their machines and improve performance. (You can reach Kuchar by phone at 217 854-9838 or by email at kuchar@ctnet.net.)
Kuchar says farmers only have to spend a few days each year and minimal dollars to better maintain their combine, do a better job of harvesting, save repair bills, and make more money from their crops. Kuchar tells farmers attending his combine seminars to go over their machines like a doctor giving a thorough physical. Start the diagnosis, Kuchar says, at the front of the machine, where the sickle meets the grain.
Sickle Timing
Time the sickle in the center of the platform, not on one end or the other. The center section on the head should always stop in the center of the guard. That being done, the sickle will cut uniformly and not tear plant stems and shatter the heads or pods, which can leave 1-2 bushels per acre on the ground.
Reel Setting
Reels are often set too fast or too slow. Either way can shatter grain or cause the platform auger to reject material. Kuchar says his rule of thumb is to set reel speed slightly faster than ground speed. "The reel should look like it's pulling the machine through the field," Kuchar says.
Also, locate the reel as far forward and as high as possible for crop conditions. The fingers should gently tip the crop toward the auger, not lift it or throw it on top of the auger.
Auger Setting
Kuchar says that slowing the auger speed will help it feed material evenly off the sickle. If it runs too fast the material is thrown back toward the sickle and won't move evenly into the auger and the feederhouse. About 130-140 rpm's is the best speed; 170-190 rpm's is too fast. Change the chain sprocket to set the speed.
On many machines, the auger moves more material to the sides of the feederhouse rather than to the center. It should feed evenly across the width of the feederhouse. You can improve infeeding to the machine by removing some of the fingers in the auger. Kuchar suggests removing 3 fingers from each side nearest the edge of the feederhouse to make it feed more evenly. On rotor machines, remove the same number of fingers.
Kuchar says you can look at the paint wear patterns on a new head and tell a great deal about what is happening. On many machines there isn't any wear on the center of the auger, which isn't a good sign. This means that material is feeding too much to the sides and not enough to the center.
Auger Flighting
The main auger should not be sharp to the touch like a knife, it should be smooth on top and sharp on the edges. If it's sharp to the touch, it could be damaging grain as it feeds into the machine. Kuchar recommends grinding the top edge of the auger flat and to also make sure any bends are removed.
Another area to check is the length of the auger flighting. Kuchar says flighting should never extend more than 3 inches past the opening of the feederhouse. If it does, cut the flighting back and material inflow will improve. On pickup headers the length of flighting isn't as critical because the material is already in a swath and not feeding from the sides.
Kuchar says that operators should be careful not to run dirt into their machines. Excessive dirt can cause auger damage in as little as 150-200 hours. Normally auger wear wouldn't occur until 1,200-1,400 hours. Rasp bars and the leading edge of the concave are also subject to abnormal wear when dirt runs into the machine.
Feederhouse
Make sure the chain has the proper tension by checking specifications in the operator's manual. The correct tension should allow you to slide a piece of paper under the chain and remove it without pinching. If the chain is too tight, sprockets and bearings will wear too fast. C
To read the rest of this story, download this issue below or click
here to register with your account number.