You have reached your limit of 3 free stories. A story preview is shown instead.
To view more stories
(If your subscription is current,
click here to Login or Register.)
Metal Casting Skills Lead To Profit, Fun
When Roger Erickson set out to build his own helicopter from scratch (Vol. 28, No. 6), he had to learn how to cast his own metal parts. What he didn't expect was that it would become a new source of profit, and fun.
"I have been doing foundry work now for about 10 years, but I didn't get proficient at it until
..........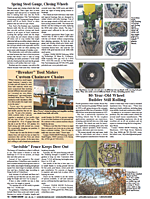
You must sign in, subscribe or renew to see the page.
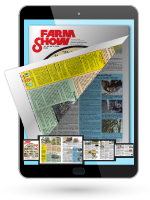
You must sign in, subscribe or renew to see the flip-book
Metal Casting Skills Lead To Profit, Fun FARM SHOP Parts 29-1-27 When Roger Erickson set out to build his own helicopter from scratch (Vol. 28, No. 6), he had to learn how to cast his own metal parts. What he didn't expect was that it would become a new source of profit, and fun.
"I have been doing foundry work now for about 10 years, but I didn't get proficient at it until the last five years," says Erickson, who makes everything from cylinder heads to gears, pistons, and more. "In the last two years, I have also gotten into artwork. I enjoy super heavy detail work, like taking fingerprints off a mold of a finger."
Erickson credits an 85-year old friend, Wayne Thompson, for teaching him much of what he knows about casting metal. Thompson, he says, didn't start doing foundry work until he was 65, suggesting that it is never too late to start.
Although Erickson's walls are adorned with a number of pieces of cast artwork from large eagles to a 50-lb., full-size, brass Sheltie dog, it isn't art that pays the bills. He has casts of everything from gears and gear cases to heads for a WD Allis Chalmers and 4-cylinder Wisconsin engines.
"The Wisconsin cylinder heads tend to crack, and the spark plugs blow out," says Erickson. "I cast new heads and update them by thickening them up where the spark plug goes so it doesn't strip. The original ones also used to warp and lose the head gasket, so I thickened them up slightly, and that's no longer a problem."
Erickson also casts furnace pots for his corn fed furnaces and boilers, as well as parts for converting car engines for airplane use.
"I started out making kits for converting V-8's for use in light planes," explains Erickson. "I made the gears and everything for $6,000 to 8,000 each."
He has built several metal-casting furnaces, including an outside one with a tilter that holds 150 lbs. of molten metal. He can melt steel in them, but does most of his work in brass or aluminum.
"I build the metal furnaces myself out of steel, refractory cement, air blowers, and LP gas fittings," says Erickson. "I can't buy anything that works as well as the ones I build. I can go from a cold start to liquid metal in 15 minutes."
One gear case Erickson cast for his helicopter weighed 72 lbs. It took two people to pour. The lifesize Sheltie dog was another massive pour. Not only was it super detailed, but it was also hollow, which required a sand core.
Erickson makes a pattern of the piece he wants to reproduce. In the case of his artwork, he may use ceramic or whatever is available to create a mold of the original art. Wood or metal pieces may serve as the pattern. Packing sand around the pattern creates a mold to be filled with the liquid metal.
A sprue or channel is cut in the sand at a little distance from the mold. It carries the molten metal to a depression or gate. The metal spills into the gate and then runs out of it and into the mold. A breather in the mold allows hot gasses to escape.
Contact: FARM SHOW Followup, Roger Erickson, Erickson Machine, 1114 East 4th Street, Fairmont, Minn. 56031 (ph 507 238-4134; email: rerick@frontier.net; website: www.cheetah350.com).
To read the rest of this story, download this issue below or click
here to register with your account number.