You have reached your limit of 3 free stories. A story preview is shown instead.
To view more stories
To view more stories
SUBSCRIBE OR RENEW NOW
(If your subscription is current, click here to Login or Register.)2004 - Volume #28, Issue #5, Page #17
[ Sample Stories From This Issue | List of All Stories In This Issue]
Giant Bale Furnace Heats Two Poultry Barns
Bob Pickering of Foam Lake, Sask., built his own large capacity bale furnace that heats 40,000 sq. ft. at a fraction of the price of natural or LP gas.Pickering plans to burn 730 large round flax bales per year to heat two poultry barns. From the time the furnace was completed in November, 2003, until late ..........
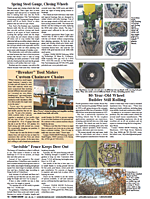
You must sign in, subscribe or renew to see the page.
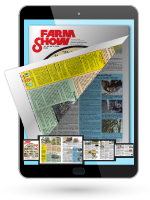
You must sign in, subscribe or renew to see the flip-book
Giant Bale Furnace Heats Two Poultry Barns ENERGY Crop Residue Burners Bob Pickering of Foam Lake Sask built his own large capacity bale furnace that heats 40 000 sq ft at a fraction of the price of natural or LP gas Pickering plans to burn 730 large round flax bales per year to heat two poultry barns From the time the furnace was completed in November 2003 until late July he had used about 400 bales The barns have to be kept at about 95 degrees when we ve got baby day-old chicks Natural gas is still my backup but it only kicks in if I m out of straw or busy doing something else he explains I plan to heat another 15 000 sq ft with it when I eventually run pipes to my shop and another smaller barn Pickering says he was motivated to build the furnace because the cost of natural gas has been continually increasing Two winters ago we had a $7 500 per month bill so we decided to do something about it Pickering says After some research we came up with our own idea The furnace itself including labor cost between $15 000 and $18 000 The total cost with trenching pumps and heating elements in the barns was about $50 000 Canadian We think we should have a payback in 2 1/2 years The furnace s firebox was made by inserting a 7-ft dia by 21-ft long underground fuel tank into a larger 11-ft dia by 23-ft long fuel tank so that the end of the smaller tank sticks out by about 3 in The edges were sealed so that the space between the two tanks serves as a water jacket holding close to 10 000 gal We put a door in the end of the smaller tank to insert the round bales Pickering says The double-walled 2 1/2-in deep door has a sealed hole in it where we installed an old furnace fan with an adjustable damper on it This is controlled by an aquastat The door actually holds 50 to 60 gal of water making it part of the water jacket which keeps it from warping when the furnace is on a hot fast burn Water circulates through the door via a flexible radiator hose When water temperature in the main tank reaches the temperature pre-set on the aquastat it will shut the fan off and the damper automatically closes so the fuel bales smolder until heat is called for again They cut a hole at the back end of both tanks for a 16-ft long by 10-in dia chimney made from 7/16-in thick pipe With the fan and chimney at opposite ends of the furnace Pickering says the unit burns clean because of the air currents created We welded a bunch of valves and bungs on the end of the water jacket and ran underground lines to our chicken barns Each barn has a 14-gal per min pump that circulates hot water from the tank through the barns and then back to the tank he explains All we have in the barns are 1 1/4-in copper lines with 4-in aluminum fins The barn dimensions are 60 by 320 ft and there are approximately 700 ft of element in each barn since each element makes a loop down and back They hang directly under the ceiling fans which push heat downwards for brooding The capacity of the elements varies with the temperature of the water and the amount of air circulation At 120_ water temperature they are rated at about 700 btu/ft At 180_ they produce close to 1 400 btu/ft This makes the capacity of the system close to 1 million btu s per barn We bought the heating element from a plumbing supplier for about $12/ft For insurance purposes Pickering says they had to locate the furnace about 100 ft away from the barns They poured a cement pad and built a metal stand to set the furnace on so it is out of the way He says he can load three 5 by 6-ft round bales into the furnace at one time On average throughout the year he loads two bales per day - one in the morning and one in the evening “We’ve found that flax straw produces the fastest heat and the least amount of ash but we have also burned wheat straw ” he says “Flax burns to dust and is a lot less work to clean I clean the furnace once every six weeks using a scoop I built that attaches to the bale prong on my front-end loader So far I’ve just been spreading the ash around the furnace to keep the weeds down It’s like a heavy dose of phosphorus and would be too rich for anything to grow if you put it on your fields ” Pickering’s bale furnace also serves a dual purpose - as an incinerator for their dead birds and any burnable garbage “The biggest cost is putting the copper aluminum pipes heating elements in your barns Everything else was made from salvage scrap that we picked up around the area ” Pickering says “Flax straw is readily available and most people find it hard to get rid of People are offering it to me all the time or the cost of baling it which is about $10 per bale I expect to grow enough of my own this year as I have about 700 acres in flax It compares to coal in the amount of heat you get per ton ” Contact: FARM SHOW Followup Bob Pickering Box 1029 Foam Lake Sask Canada S0A 1A0 ph 306 272-4766; fax 306 272-3766; email: pick272@sasktel net
To read the rest of this story, download this issue below or click here to register with your account number.