1992 - Volume #16, Issue #6, Page #08
[ Sample Stories From This Issue | List of All Stories In This Issue | Print this story
| Read this issue]
Bale Processor Built Out Of Manure Spreader
Robb Peck, Carey, Idaho, wasn't satisfied with the commercially-built hay processor he was using to chop big square bales for his dairy cows, so he built his own processor out of an old manure spreader.A big drive sprocket off an old Massey Ferguson combine, driven by a truck differential, chain-drives three 6-ft. long rows of beater bars fitted with angled steel knives. An orbit motor drives the spreader's apron chain which feeds bales back into the knives. Chopped hay is thrown backward about 10 ft. and then loaded into a mixer truck.
"It chops hay into 4 to 5-in. lengths which is just right for cows and will process a 1-ton bale in slightly over one minute," says Peck. "I tried using a Haybuster tub grinder, but it chopped the hay too fine which caused it to be low in fiber. I also tried using a Hesston bale processor, but it chopped so coarse that the hay wouldn't feed out evenly from the mixer truck. I bought the manure spreader from a neighbor for $100 and spent a total of less than $2,000 to modify it. A comparable size bale processor would have cost at least $20,000. I built my own knives which saved a lot of money.
"I use tractor hydraulics to operate the apron chain's orbit motor which I salvaged from the reel drive of an old IH combine."
Peck used 4-in. sq., 1/2-in. wall steel tubing to build the three 6-ft. long beater bars. He made each knife out of two pieces of steel. First, he cut 1/2-in. thick steel plate into 4-in. squares and welded them onto the beater bars, spacing them about 3 in. apart in a spiral fashion around the tubing. He then cut 4-in. wide, 3/16-in. steel plate into 5-in. long sections and sheared them diagonally to make knife points and then welded the points onto the 4-in. pieces already on the beater bars.
He used 8-in. channel iron to build a 74-in. sq. steel frame to support the beater bars, which mount on pillow block bearings on each end. He then extended the rear frame of the spreader about 2 ft. and mounted the beater bar assembly on the extension. "All knives turn counter-clockwise so hay is lifted up as it comes into contact with the knives. It never plugs up because the knives overlap slightly."
A 2-ton rear axle (with the wheels removed) salvaged from an old military truck is mounted under the back of the spreader. Peck welded one end of the axle in place and mounted the combine drive sprocket on the other end. The truck's driveline is pto-driven by the tractor pulling the spreader.
Contact: FARM SHOW Followup, Robb Peck, Box 26, Carey, Idaho 83320 (ph 208 823-4440).
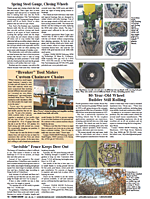
Click here to download page story appeared in.
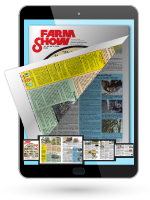
Click here to read entire issue
To read the rest of this story, download this issue below or click here to register with your account number.