2002 - Volume #26, Issue #5, Page #10
[ Sample Stories From This Issue | List of All Stories In This Issue | Print this story
| Read this issue]
Shop Exhaust System Made From PVC Pipe
![]() |
![]() |
![]() |
![]() |
"I bought the pipe at a plumbing store and came up with new techniques to make various parts, such as sliding blast gates. By using plastic pipe and building the system myself I saved a lot of money," says May.
The exhaust system consists of 6-in. dia. pipe and elbows that hook up to a 2 hp, 220-volt electric vacuum motor. There are eight outlets for connecting the pipe to several machines, which include a shaper, planer, 24-in. drum sander, 10-in. table saw, and two sanders. Flexible plastic 4-in. hoses run from the exhaust system to wherever the machines are in use.
Sawdust shavings and dirt are blown into a 55-gal. barrel located in a separate room outside the shop. Material spins around inside the barrel and falls through the open bottom into a 3-ft. sq. wood box for later disposal.
Homemade, tapered reducers connect the main 6-in. pipe to the 4-in. dia. hose that runs to each shop tool. "Using pairs of tapered plastic reducers results in much more efficient air flow than using a single, abrupt plumbing reducer," notes May.
He made sliding "blast gates" out of flat sheets of PVC. The gates work like a valve, opening and closing the air flow to the tool.
"I just open the gate on the tool that I'm using. I installed three extra outlets to vacuum the floor, clean off my work bench, etc.
"I mounted a toggle switch on each gate so I can start or stop the vacuum right from the machine I'm working at. To get current safely to the switches, I installed a 24-volt transformer at each gate. It converts 110-volt electricity down to 24-volt AC. Flipping the switch pulls in a relay, which closes the contacts to deliver 220 volts to the vacuum motor."
To make flat plastic sheets for the blast gates, he cut through one side of a piece of pipe, then heated it to 280 degrees in an oven until the plastic became soft. Then he flattened it out between two boards.
He used the same technique to make the reducers except that he didn't flatten them out but instead rolled each one into a tapered shape. Then he used PVC cement to glue them together. The reducers are attached to the outlets by spring-loaded clamps. A short piece of 1/2-in. dia. pipe serves as a handle for each gate.
According to May, a "cyclone effect" is created inside the barrel as the incoming air - traveling at 3,500 ft. per minute - enters the barrel at a steep angle and lowers the velocity of the air, which causes the debris to start spinning. Clean air is sucked out of another pipe at the top of the barrel and travels back to the blower.
"The barrel has a clear plastic window on it so you can watch debris flying around inside the barrel," notes May.
Contact: FARM SHOW Followup, Steve May, 41464 Ratcliff Dr., Prairieville, La. 70769 (ph 225 622-2246).
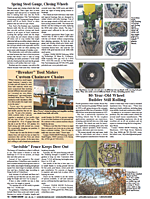
Click here to download page story appeared in.
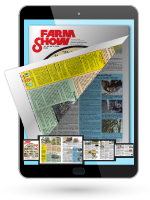
Click here to read entire issue
To read the rest of this story, download this issue below or click here to register with your account number.