2002 - Volume #26, Issue #4, Page #03
[ Sample Stories From This Issue | List of All Stories In This Issue | Print this story
| Read this issue]
PTO Powered By Separate Engine
![]() |
![]() |
![]() |
Even with a good-sized hydraulic motor driving the unload auger on the cart, it still took about 10 minutes to unload a full cart so the Bartmanoviches, Michael and Ron and their respective sons, Ryan and Doug, decided to put a pto on the tractor.
When they looked into it, they found that to fit a factory-style pto to the old 895, they'd need to replace the 12-speed standard transmission with a 15-speed transmission to accommodate the pto. That also meant replacing the bell housing and driveline. On top of that, they'd still need to add the pto shaft to the rear of the transmission.
Thinking there had to be another way, Ryan remembered hearing about someone who had mounted an engine on a tractor just to power a pto.
"I figured we could do that, so I started pulling together what I thought we'd need," says Bartmanovich.
He called Worthington Ag Parts, Niverville, Manitoba, and bought a rebuilt 239 John Deere four cylinder turbo diesel engine. He mounted the 85-hp engine on a skid made of 2 by 3-in. steel tubing that he built to mount to the tractor with just four bolts.
"The skid mounts between the fenders behind the cab," he says. "Two bolts go through the top plate on the drawbar of the 895 and two more go through the tractor frame, one on either side of and just behind the cab."
He mounted the water-cooled engine with the radiator pointing away from the tractor to assure the pto turned the right direction.
The grain cart needed a pto speed of 1,000 rpms, but the engine, when running at optimum speed, turned at 2,100 rpms.
Four high torque V-belts from the engine's flywheel power a gearbox. "I calculated the size of pulleys it would take to step the speed down to 1,000 rpms and put those on the gearbox," he says.
The gearbox has an internal hydraulic clutch so Ryan tapped into lines on the tractor that were set up to power an air seeder. Since the hydraulic clutch requires a flow of only 1 to 2 gal. per minute at 200 psi and the tractor's system puts out 20 gal. per minute at 3,000 psi, he had to install a pressure reduction valve and a flow control valve in the line to the gearbox.
A cable from the gearbox to the tractor cab manually engages the clutch, which turns on the pto.
In addition to tapping into the tractor's hydraulics for the pto engine, Bartmanovich also ran wires so he could use the tractor's battery to start the engine and he put a T in the fuel line, so he can fuel the pto engine from the tractor's fuel tank.
"The Deere engine has an old dead alternator on it, which just serves as a tensioner for the belt since it gets all its electricity from the tractor," he notes.
In order to monitor the pto engine, Bartmanovich made an instrument panel for it by mounting temperature and oil pressure gauges for it on an aluminum plate, which he then mounted in the cab of the tractor.
"We can now unload a full 750 bu. in just 3 minutes. And by speeding up unloading, we're able to move grain away from the combines, so there's never any time spent waiting on the cart.
"We can use it for any pto-powered implement we'd want to use behind the Versatile," he says. "Once we were done with harvest, we just unhooked the hydraulic and fuel lines, disconnected the battery cables, took out the four bolts and moved it off the tractor with a chain on a front-end loader. It takes only a few minutes to take it off or put it on."
He says an unexpected benefit over a factory pto is that the drive unit can be at full rpm while the tractor is at an idle, creeping alongside the truck while unloading. "It's far easier on the clutch," he says.
Bartmanovich says it took 50 to 60 hours to plan and build the pto. He says he couldn't have completed the project without outside help. "Hy Power in Winnipeg provided hydraulic help, and we had a flywheel adapter plate machined for us at Paska Sa
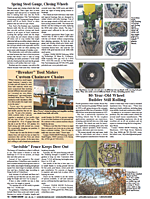
Click here to download page story appeared in.
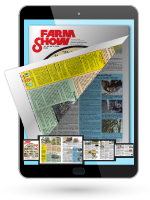
Click here to read entire issue
To read the rest of this story, download this issue below or click here to register with your account number.