You have reached your limit of 3 free stories. A story preview is shown instead.
To view more stories
(If your subscription is current,
click here to Login or Register.)
Low-Cost Shop Exhaust System
All shops have a problem with cleanliness. My shop has an exhaust system that I built at minimal cost. It works quite well.
The exhaust system consists of 4-in. dia. sewer pipe and elbows that hook up to a blower that's belt-driven by a 1 hp electric motor. There are four outlets for connecting the pipe to machi
..........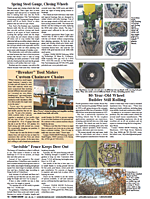
You must sign in, subscribe or renew to see the page.
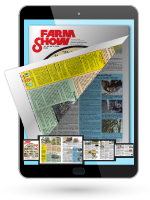
You must sign in, subscribe or renew to see the flip-book
Low-Cost Shop Exhaust System FARM SHOP Miscellaneous 26-2-36 All shops have a problem with cleanliness. My shop has an exhaust system that I built at minimal cost. It works quite well.
The exhaust system consists of 4-in. dia. sewer pipe and elbows that hook up to a blower that's belt-driven by a 1 hp electric motor. There are four outlets for connecting the pipe to machines or to an adapter for floor cleaning. I used 4 to 3-in. reducers at each connector. RV sewer drain bayonet connectors are force fit into the 3-in. end of the reducers and can be closed when not in use by the use of RV drain caps. Heavy duty RV drain hose is used to connect individual machines to the exhaust system whenever the machines are in use. An adapter also lets me use light duty hose and shop vac accessories for floor and machine dust removal.
The blower was built from a lawn mower bearing housing attached to a 9-in. plywood disc. The impeller vanes were made from sections of 3-in. aluminum angle iron. The blower's outer housing is made from 5/8-in. thick plywood, grooved to accept galvanized metal that fits closely to the impeller and is held together by several bolts.
Sawdust and shavings, etc., are blown into a pile outside the shop for later disposal. The overall system is 80 to 90 percent effective in getting rid of shop waste."
The "plumbing" system is spirally wrapped with aluminum electric fence wire and grounded to discharge static electricity. (T. E. Salsman, Southern Tool and Engineering, 124 Jolly Ridge Road, Richmond, Ky. 40475 ph 859 624-1145)
To read the rest of this story, download this issue below or click
here to register with your account number.