You have reached your limit of 3 free stories. A story preview is shown instead.
To view more stories
(If your subscription is current,
click here to Login or Register.)
Drive-In Refrigerator Keeps Vegetables Fresh
Growing and selling fresh vegetables has been a profitable enterprise for Greg and Polly Rinehart, Boone, Iowa, for the past 15 years.
"At first, it was a way to make extra money in the summers," Rinehart says. "But over the years, it has become a more consistent source of income than our 600 acres of row cr
..........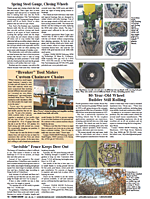
You must sign in, subscribe or renew to see the page.
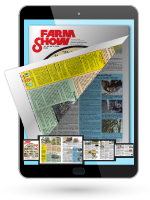
You must sign in, subscribe or renew to see the flip-book
Drive-In Refrigerator Keeps Vegetables Fresh FARM HOME Food 26-2-29 Growing and selling fresh vegetables has been a profitable enterprise for Greg and Polly Rinehart, Boone, Iowa, for the past 15 years.
"At first, it was a way to make extra money in the summers," Rinehart says. "But over the years, it has become a more consistent source of income than our 600 acres of row crops."
The Rineharts sell most of their produce at farmers markets on weekends. Keeping vegetables fresh from the time they're picked was always a problem. For years they used walk-in coolers on the farm.
As the business grew, they decided they needed something large enough that they could drive right into.
"We had this big livestock barn we weren't using anymore so we converted one side of it into a cooler," Greg says.
They enlisted the help of Mark and Cindy Westrum, Stratford, Iowa, who were also in the fresh market vegetable business. The Rineharts and Westrums help each other out and share a green bean picker. "Since we were going to set up a green bean line there, it seemed logical to work with them on this, too," Rinehart says.
On one side of the barn, they installed a conveyor with a sorting table and washer to clean beans. "We pick about 50 bu. of beans at a time with our picker," Rinehart says. "We dump those on the conveyor and then everyone sorts and cleans. Then the beans are packed in bushel containers and carted over to the cooler on other side of the barn."
To make their drive-through cooler, they put up stud walls to make a 14 by 40-ft. room and insulated it all the way around with bat insulation. They added more insulation by finishing the inside of the cooler with styrene board that was finished on the inside. Then they installed insulated doors so they could enter the cooler from either the outside or from the vegetable processing area.
"We cool the room with a large used refrigerator compressor we bought from a neighbor. It keeps the temperature at between 35 and 40 degrees," Rinehart says. "We did most of the work ourselves, but I hired an expert to hook up the cooling system and we had a carpenter help us with the doors, so they fit right."
Shelves along one side of the cooler are designed to hold bushel boxes of green beans and other vegetables.
There are two big swinging doors to the outside. When those are open, they can back a pickup or trailer right into the refrigerated room.
"Sweet corn and green beans take up most of the space in the cooler," Rinehart says. "We sell sweet corn out of the same trailer we pick it on. If we can't sell it the day it's picked we park the trailer in the cooler. We can put as many as four trailers into the cooler at once, although we seldom have more than three in it."
Rinehart says turning the barn into a cooler was relatively inexpensive. They use it for everything from asparagus to zucchini, turning on the cooling system in early July. It's usually the end of October, when they've finally picked and sold the last of 10 plantings of sweet corn and 12 plantings of green beans. He says electricity to run the compressor averages about $150 a month during the four months of use.
Contact: FARM SHOW Followup, Greg and Polly Rinehart, 703 Kale Rd., Boone, Iowa 50036 (ph 515 432-4480; E-mail: rinehart@tdsi.net).
To read the rest of this story, download this issue below or click
here to register with your account number.