You have reached your limit of 3 free stories. A story preview is shown instead.
To view more stories
(If your subscription is current,
click here to Login or Register.)
Stationary Thresher Turned Into Combine
Right after World War II, when new farm machinery was still a little scarce, William Briden, Crookston, Minnesota, needed a combine but the only ones available at the time were for direct-cut grain and they would have choked on the grain that was swathed before it was dry enough to thresh.
"Early combines would
..........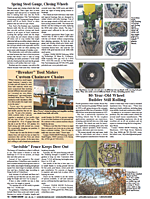
You must sign in, subscribe or renew to see the page.
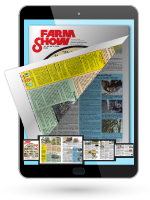
You must sign in, subscribe or renew to see the flip-book
Stationary Thresher Turned Into Combine COMBINES Conversions 26-2-23 Right after World War II, when new farm machinery was still a little scarce, William Briden, Crookston, Minnesota, needed a combine but the only ones available at the time were for direct-cut grain and they would have choked on the grain that was swathed before it was dry enough to thresh.
"Early combines would handle just the heads and a little straw. Threshing machines, on the other hand, were designed to handle lots of straw," he points out.
So Briden decided to make his own combine to handle swathed grain and straw using a Twin City stationary thresher, which he says was ideal.
"It had a 32-in., 16-bar cylinder, instead of the 12-bar cylinder being put into most combines at the time," he notes. "Twin City threshers did a better job of threshing with a cylinder speed of only 700 to 800 rpm's, instead of 1,000 to 1,200 rpm's for most combines. Because of the slower speed, they didn't wear out as fast."
Some other features that made Twin City threshing machines good candidates for converting to combines included the all-steel construction and the fact that they had a full-length non-choke sieve under the straw rack. This arrangement kept the sieves from being overloaded. "And return grain ran through a separate cylinder rather than back through the main cylinder. This kept some of the load off the main threshing cylinder, so grain was cleaner.
"They were very well built and very high priced machines," he says.
Pickup headers weren't readily available, so Briden made his own, with a 3-ft. diameter auger in it. He made the auger by welding 12-in. strips of 16-gauge steel (for flighting) around a 24-in. diameter steel tube. It had a drag chain that was made from chain he found in the junk at a local sugar beet processing plant.
"The circumference of the auger and flighting was about 9 ft., so long straw couldn't get wound around it and choke the header," he says. He added a belt pickup from a John Deere 17 combine and powered it with a 4-in. flat belt from the combine cylinder.
He took the hopper and unload auger off an old Case pull-type combine. "It took longer to unload the hopper than it did to fill it," he says. To get around that, he mounted two more similar hoppers on the combine and cut the sidewalls from between them before welding them together. Beneath the triple sized hopper, he added a straight 10 in. unload auger.
He powered his combine with a Chrysler V-8 Hemi engine. "I don't remember the horsepower on it, but it was a lot more than the combine needed. It would handle the combine at a little more than an idle. Because we weren't making it work hard, the valves had a tendency to carbon up on it," he recalls.
"There was always a lot of rust and dust in the swaths, and air coming out of the cylinder would blow it forward onto the tractor operator," Briden says. To make it a little cleaner and more comfortable, Briden put a blower above the header auger.
He pulled his combine with a 1935 McCormick Deering WD40 diesel. "I bought it from the original owner and used it on the combine for as long as I ran it," he says. Although he's long since sold the tractor, he borrowed it back from the current owner to use to pull his combine at a steam thresher show last fall.
Briden says his Twin City combine conversion worked so well that he built a second one so he could do custom work in addition to harvesting the 500-600 acres of small grains he grew on his 900-acre farm.
Contact: FARM SHOW Followup, William Briden, Box 265, Rt. 2, Crookston, Minn. 56716 (ph 218 281-2829).
To read the rest of this story, download this issue below or click
here to register with your account number.