You have reached your limit of 3 free stories. A story preview is shown instead.
To view more stories
(If your subscription is current,
click here to Login or Register.)
Self-Propelled Compost Turner Makes Farm-Based Business Profitable
When they went looking for a compost turning machine about a year ago, Albert Waardenburg, his son Ron, and their business partner, Mark Stratford, found the price tag of $500,000 for big machines to be a bit hard to justify for their fledgling business.
The Waardenburgs got into the compost business after they
..........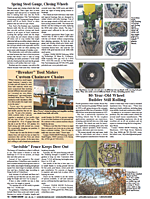
You must sign in, subscribe or renew to see the page.
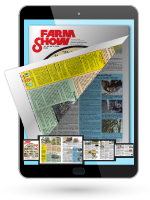
You must sign in, subscribe or renew to see the flip-book
Self-Propelled Compost Turner Makes Farm-Based Business Profitable SPECIALTY/SERVICES Specialty/Services 26-2-19 When they went looking for a compost turning machine about a year ago, Albert Waardenburg, his son Ron, and their business partner, Mark Stratford, found the price tag of $500,000 for big machines to be a bit hard to justify for their fledgling business.
The Waardenburgs got into the compost business after they sold their 150-cow dairy herd and partnered with Stratford to build a 100 by 65-ft. building on Albert's farm near Abbotsford, British Columbia.
They had easy access to livestock and poultry manure, plus waste produce and paper products from area grocery stores. Waardenburg says much of the material would otherwise end up in landfills.
The composting building has four storage alleyways about 11 ft. wide by 100 ft. long. The concrete floors in these alleys slope to the center, where drain outlets take liquid run-off to a septic system, where it's pumped back onto the compost piles to keep them from drying out. The floors are also aerated, so they can pump air into the stacks to aid in the composting process. Along the walls, the floors have a flat curb about 1 ft. wide, the full length of the alley, which they designed as a guide for a compost turner.
Instead of buying a commercial turner the men decided to try something different. They spent about $18,000 on a big, self-propelled Snowblast commercial snowblower. "I thought we might be able to use the blower to turn the compost piles," says Albert.
But the unmodified blower just couldn't handle the compost. So the men, with help from Albert's brother-in-law George Funk, began modifying the machine, a little at a time, to come up with something that would do the job.
After nearly ten months of trial and error, they've come up with a machine that does exactly what they wanted.
The first step in remodeling the snowblower was to give it a wider stance. Even when the wheels were set as wide as possible on the axles, it was still not wide enough to straddle the alley and ride on the curbs.
Waardenburg had help solving this problem from Reg Sanders, also of Abbotsford. Sanders, a retired machinist who likes to stay busy in the shop, cut the rims off the hubs of the snowblower's wheels and welded them back together, giving them as much dish as possible. This gave the loader a track of 10 ft. 6 in., measured from the outside of the tires.
They tried several different methods of turning and restacking the compost. What finally worked is an apparatus that mounts on front in place of the snowblower. It pulls the stack down onto an underslung conveyor belt that runs the compost to the rear of the tractor and deposits it onto a second conveyor that takes the material up 10 ft. and drops if off the back.
There's a 10-ft. long, 2-ft. diameter rotating drum, covered with teeth that the men cut in triangles from 1/2-in. steel plate. The drum picks up the compost and deposits it on the conveyor belt.
Helping the drum do it's job is a 10 ft. beater bar, taken directly from an old power harrow, that's mounted on hydraulic cylinders, so it can be raised or lowered to comb off the front of the stack.
Along both outside edges of the frame are two vertical pipes, also with teeth, that rotate inward to pull the edges of the stack toward the horizontal drum below. Orbit motors from a side delivery rake turn these pipes.
Angled sheet metal on either side of the drum funnels the compost onto the 5-ft. wide conveyor belt.
Getting drive systems in place for all the different moving parts of the turner took time and more outside expertise.
"Reg Sanders helped us with the driveline for the big drum. It runs off the same pto that had run the snowblower. He also helped us get the timing of everything right by selecting the right size sprockets for drive and driven shafts," Waardenburg says. "Reg's brother, Les, is a retired hydraulics expert. He rebuilt some old Caterpillar hydraulic pumps for us and modified their output so we could use them to d
To read the rest of this story, download this issue below or click
here to register with your account number.