2002 - Volume #26, Issue #1, Page #13
[ Sample Stories From This Issue | List of All Stories In This Issue | Print this story
| Read this issue]
Folding Toolbar Converted To Hydraulic Pipe Bender
![]() |
![]() |
But how to make a bender that could handle 1-1/2 to 2-in. pipe was a puzzler. Then one day they got an idea. "We had an old 30-ft. Crust Buster folding toolbar. It had been retired for some time but there was nothing wrong with the bar and cylinders," Alan Busenitz says. The toolbar's side wings folded forward manually.
They removed the hoe drill units and then proceeded to turn the toolbar into a pipe bender.
They started by mounting wheel rims at the center of the middle section and on the end of the wings. A hydraulic motor chain-drives the wheels on the center section.
The motor, chain and sprockets were taken from an old combine header they no longer used.
To bend pipe, they feed the pipe in front of a wing wheel, behind the center wheel and then in front of the wheel on the other wing. Then they set the angle of the bend they want by changing the angle of the wings. Once that's done, they start the hydraulic motor on the center wheel and roll the pipe through.
If they need several sections with the same bend, they add pipe to the input side by welding lengths together as the pipe feeds in. On the opposite side, they added a bracket to mount their chop saw. When the arched section is the proper length, they cut it off. By welding and cutting as they go, they never have to remove the pipe from the bender, so the arch is the same on all pipe bent.
Working together, the Busenitz brothers can bend one hoop in about five minutes. They use 14 hoops for each of their hoop buildings, so it takes an hour and ten minutes to bend the hoops for one building.
Busenitz says they've used their bender to make several 36-ft. wide hoop shelters. In fact, they've rolled about 10,000 ft. of pipe through it. "We checked with one machine shop about bending pipe for us before we made this and they wanted $1 a ft. for bending," he says.
"We've made only 36-ft. wide buildings with it so far, but I'm sure the angle of the arch could be more or somewhat less and you could make wider or narrower spans with it. The tighter the bend, the more pressure there would be on the center wheel and at some point, it would probably spin on the pipe," says Busenitz.
Contact: FARM SHOW Followup, Alan Busenitz, 8831 NW Hopkins Switch Road, Potwin, Kan. 67123 (ph 620 752-3563).
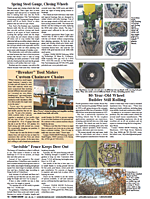
Click here to download page story appeared in.
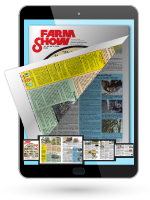
Click here to read entire issue
To read the rest of this story, download this issue below or click here to register with your account number.