You have reached your limit of 3 free stories. A story preview is shown instead.
To view more stories
(If your subscription is current,
click here to Login or Register.)
Washing Machine Sand Blasting Cabinet
After using commercial sand blasting cabinets for years, Bruce Graham knew their shortcomings û dust that causes poor visibility, poor lighting, difficult-to-maintain filters, and expensive and difficult-to-change media. He avoided most of those problems when he built his own sand blaster out of a top-loading washing m
..........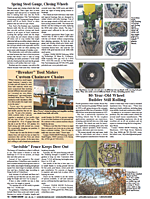
You must sign in, subscribe or renew to see the page.
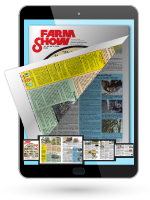
You must sign in, subscribe or renew to see the flip-book
Washing Machine Sand Blasting Cabinet FARM SHOP Miscellaneous 24-6-42 After using commercial sand blasting cabinets for years, Bruce Graham knew their shortcomings û dust that causes poor visibility, poor lighting, difficult-to-maintain filters, and expensive and difficult-to-change media. He avoided most of those problems when he built his own sand blaster out of a top-loading washing machine.
Graham made an angle iron framework and set the stripped-down washing machine case in it on its side at a 35 degree angle. He used galvanized sheet metal to close off the top and bottom of the washing machine (which are now the sides). On one side he left a large removable half section on to serve as an access door. Two large windows were cut out of the top and front-facing sides and 1/4-in. thick glass panes inserted in them. A clamp-style floodlight mounts directly against one window.
He cut a pair of 7-in. dia. holes, spaced 16 in. apart, in the front of the cabinet and attached industrial quality rubber gloves inside them. He cut a 2-in. wide opening in the bottom of the cabinet along its entire length, allowing heavy particles to fall through a galvanized steel funnel and into a hopper. A large kitchen strainer mounted across the top of the hopper traps any debris or parts that might fall through the edges of the grating.
Inside the cabinet is an expanded steel grating laid across four 1-in. angle iron supports. A piece of 1/4-in. sq. hardware cloth on top of the grating prevents small parts from falling through.
To suck dust out of the cabinet, he closed off both sides of an old furnace blower and mounted it on the shop wall about 2 ft. above the sand blaster. The blower is activated by flipping a switch on the cabinet. A 6-ft. length of 4-in. dia. flexible hose runs from the blower down to the sand blaster and sucks out light dust particles, blowing them outside the shop through an opening in the wall. A pair of automotive breather units keep the suction caused by the blower from breaking the glass windows.
"I've had very few problems with it," says Graham. "I spent about $250. Commercial units of comparable size sell for about $1,000.
"The blower does a great job of removing dust. It pulls enough air through the cabinet to keep the area around the cabinet relatively dust-free. At first I used a canister-type shop vacuum cleaner to suck out dust. However, it was noisy and dirty and tended to clog up. I use inexpensive playground sand to do the cleaning. I sift the sand through a standard window screen sieve as I fill the hopper and discard any larger pebbles that might plug up the unit.
"The blower is much quieter than most commercial vacuum units. These types of blowers are available from junk dealers for little or nothing. The blasting gun I use is an older Craftsman model that has a replaceable ceramic tip."
Graham used wooden frames to install the windows, mitering a groove in the wood that's the same thickness as the glass. "The grooves make it easy to replace the glass," notes Graham.
Contact: FARM SHOW Followup, Bruce Graham, 13801 Eastside Rd., Tyler, Texas 75707 (ph 903 566-1248; E-mail: mechtechtyler@yahoo.com).
To read the rest of this story, download this issue below or click
here to register with your account number.