You have reached your limit of 3 free stories. A story preview is shown instead.
To view more stories
(If your subscription is current,
click here to Login or Register.)
Harvestore Silo Makes Great Wet Holding Bin
"It was an ambitious project but I'm happy with how it turned out. I saved a lot of money." says Jeff Bridgewater, Blairstown, Iowa, who converted an old 20 by 70-ft. Harvestore silo into a wet holding grain bin that's complete with a home-built, perforated, bottom aeration floor.
The 16,000-bu. capacity silo is
..........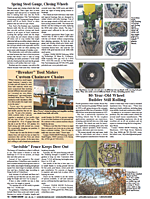
You must sign in, subscribe or renew to see the page.
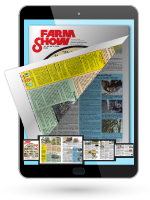
You must sign in, subscribe or renew to see the flip-book
Harvestore Silo Makes Great Wet Holding Bin SILOS Silos 24-4-44 "It was an ambitious project but I'm happy with how it turned out. I saved a lot of money." says Jeff Bridgewater, Blairstown, Iowa, who converted an old 20 by 70-ft. Harvestore silo into a wet holding grain bin that's complete with a home-built, perforated, bottom aeration floor.
The 16,000-bu. capacity silo is set between four 20,000-bu. bins and helps support a 100-ft. grain leg that towers 30 ft. above it. The leg can be used to transfer grain between any of the bins as well as the silo. A chain drag that leads from two of the bins goes through the silo and under the hopper bottom, then feeds into the grain leg which is located just outside the silo. The grain dumping site used to load the bins and silo, and the discharge spout that's used to unload grain into trucks, are both located off to one side of the silo.
From the outside, the only noticeable difference between Bridgewater's wet holding bin and an ordinary Harvestore silo is a walk-in door that he cut near the bottom of the silo. The door provides access to the cone so that he can clean it out occasionally and provided a way to winch materials into the silo during construction of the hopper bottom.
Bridgewater got the Harvestore from his landlord who wasn't using it any more. He hired someone to tear it down panel by panel and haul it on a flatbed trailer to his farm one mile away. There the silo was put back up on top of a newly-poured cement floor. The hopper stands 12 ft. high, with the bottom about 2 ft. off the floor. He used 5-in. sq. steel tubing to build 24 legs that are spaced every 2 ft. around the inside of the silo. The bottom of each leg is bolted to the floor, while the top is bolted to a 6-1/2 in. wide steel ring that runs the circumference of the silo. More 5-in. sq. tubing was used to make the hopper bottom's frame, which comes back down at a 45-degree angle off the top of the legs. Short lengths of tubing are welded horizontally between the frame legs. He then welded in perforated sheeting.
From the bottom of the cone grain falls through a slide gate and a metal "transition" and into the drag chain. A steel rod extends from the slide gate outside the silo to a wheel which is used to open or shut the slide gate.
"It was a much bigger project than I anticipated, but it was worth it because I saved a lot of money," says Bridgewater, who made the silo conversion four years ago. "I spent a total of about $7,000 on materials. A comparable commercial bin would cost thousands of dollars more than that, and it wouldn't have a perforated aeration floor. The silo makes good use of the space between the four bins. When I moved the silo to its new location there were only two bins. I put up the grain legs and the other two bins later. The beauty of tieing the grain leg in with the silo and the four bins is that we can deliver grain anywhere we want to. There are a lot of used Harvestores around that can be bought cheap, so other farmers could benefit from my idea.
"I wanted a hopper bottom instead of a flat floor and sweep auger because I didn't want to have to clean out heavy, wet corn every week or so. The hopper bottom empties out completely with no corn left in it to spoil. Because the hopper is perforated we can aerate the grain and hold it longer before we have to dry it. I probably would've installed a commercial hopper bottom if I could've found one with a perforated floor. A fan in the silo wall blows air up through the floor.
"It's a real versatile system. We use it in the fall as a wet holding bin when bringing grain in from the field. The silo can store at least 80 acres worth of corn, allowing us to keep on combining during the day and then dry the grain at night. After the harvest is over we can also use the silo to store dry grain. We've even used it to store soybeans.
"When the silo is full there are almost one million lbs. of grain on top of the hopper bottom. The horizontal pieces in the hopper bottom frame keep the funnel from bending under all that weight. They
To read the rest of this story, download this issue below or click
here to register with your account number.