You have reached your limit of 3 free stories. A story preview is shown instead.
To view more stories
(If your subscription is current,
click here to Login or Register.)
Grain Bin Mounts On Home-Built Hopper Bottom
"It saved me a lot of money," says Gary Stelpflug, Lancaster, Wis., who mounted a 3,000-bu. grain bin on top of a home-built, 10-ft. tall steel hopper to make his own 4,000-bu. wet holding bin.
Stelpflug uses the wet holding bin to dump wet corn from the field during harvest. The bin stands next to his continuou
..........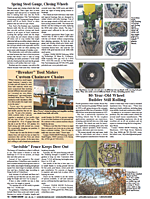
You must sign in, subscribe or renew to see the page.
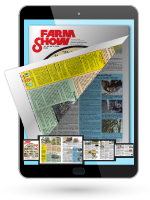
You must sign in, subscribe or renew to see the flip-book
Grain Bin Mounts On Home-Built Hopper Bottom CROP STORAGE Grain Storage 24-4-19 "It saved me a lot of money," says Gary Stelpflug, Lancaster, Wis., who mounted a 3,000-bu. grain bin on top of a home-built, 10-ft. tall steel hopper to make his own 4,000-bu. wet holding bin.
Stelpflug uses the wet holding bin to dump wet corn from the field during harvest. The bin stands next to his continuous flow grain dryer.
He made the hopper bottom out of 1/4-in. thick steel plate and mounted it on 16 steel legs (made out of 3 by 3-in., 3/8-in. thick angle iron) that are anchored on 5-ft. deep footings. He unbolted the grain bin from its concrete pad and used a truck-mounted crane to set it on top of the hopper bottom, where he bolted it on.
An auger automatically delivers corn from the hopper into the dryer. From there the corn is augered to storage bins for cooling.
"It lets us keep our combine working in the field all the time and is a real time saver," says Stelpflug, who built the unit with the help of a local machine shop. "We can keep the dryer going all night long and by the next morning the bin is empty so we can go back to the field. We can run about 7,000 bu. a day through the bin and dryer. We had been using a big gravity box as a wet holding bin but it could hold only about 600 bu. We didn't have any place else to dump our corn so our combine had a lot of downtime.
"I think my wet holding bin actually works better than commercial models because it's sloped at a 45 degree angle so even wet corn will slide down it. Most commercial models slope at only a 23 degree angle. Mine is also built much stronger than most commercial units.
"I already had the bin which was too small for our needs and didn't have a drying floor. We had to make our own hopper because, as far as I know, no one makes a pre-fab hopper bottom for a 16-ft. dia. bin. I spent $2,000 to build the hopper bottom. Commercial wet holding bins sell for $8,000 to 9,000, and you also have to spend another $1,000 to $2,000 more for concrete and to hire a crane to set the bin onto the hopper bottom."
He used eight 4-ft. wide, 10-ft. long sheets of 1/4-in. thick steel to make the hopper bottom. He cut each sheet into a triangle shape and made three bends in it, then welded all eight pieces together to form a circular shape. He bolted 4-in. wide flat steel all the way around the top of the hopper so he could bolt the bin onto it and then welded vertical lengths of 3-in. angle iron, reinforced by 1/2-in. rerod, to the bottom of the rail. He cut a series of 1/2-in. dia. holes in the rail and ran a J-bolt through each one. He then tarred the entire outside part of the rail.
Contact: FARM SHOW Followup, Gary Stelpflug, 7694 Pigeon River Road, Lancaster, Wis. 53813 (ph 608 723-4993).
To read the rest of this story, download this issue below or click
here to register with your account number.