He Repaired Dented Auger
Ray Obrecht, McCallsburg, Iowa: "Last fall my son David's 70-ft. long, 8-in. dia. grain auger blew off his 20,000-bu. grain bin during a storm, just a few days after we had finished filling the bin. The auger crashed down onto his driveway.
"The impact of the fall caused dents in the auger's heavy gauge tube and it also became somewhat egg-shaped. Also, the undercarriage got bent and twisted. A lot of other augers in Iowa were wrecked during that same storm so it was hard to find a used auger as a replacement. We didn't want to spend the money for a new one so we decided to repair ours.
"A friend who's in the body and fender business told us it would be easier to straighten one piece at a time, so I disassembled the auger into as many pieces as possible. It came apart in 20-ft. lengths. I fed each tube through my 30-ton capacity press 18 to 24 in. at a time in order to make the tube round again. We made a platform out of 2 by 8-in. wood with a bit of circle to help stabilize the tube and used a 2 by 4 to press down on the top of the tube.
"To remove the dents we borrowed the scissors car jack out of my wife's new Ford Taurus and mounted it on the press. We made a long flat base for the jack by welding a 15-in. length of 2-in. hollow square steel to the bottom of the jack. We capped the top of the jack with a slightly convex piece of metal.
"Because the tube was in 20-ft. lengths, we added 12 ft. to the jack's crank handle and welded 16 ft. of steel rod to the base so that we could position the jack anywhere we wanted to inside the tube in order to reduce the dents. One person needs to be at each end of the tube - one to position the jack while the other cranks the jack up. We also attached a 7 7/8-in. dia. sprocket to a length of aluminum conduit pipe. When we could insert the sprocket all the way through the tube we knew it had been restored to its original shape. We also used the press to straighten the auger's undercarriage.
"We used two loader tractors to reassemble all the parts. We tried to avoid tightening any bolts until a section was reassembled. The project took about seven days. We saved about $2,000 - not too bad for off-season work right at home."
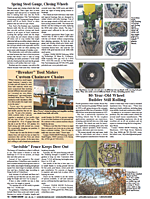
Click here to download page story appeared in.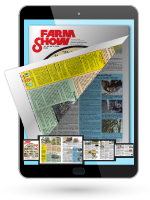
Click here to read entire issue
He Repaired Dented Auger AUGERS Augers (29B) 24-1-39 Ray Obrecht, McCallsburg, Iowa: "Last fall my son David's 70-ft. long, 8-in. dia. grain auger blew off his 20,000-bu. grain bin during a storm, just a few days after we had finished filling the bin. The auger crashed down onto his driveway.
"The impact of the fall caused dents in the auger's heavy gauge tube and it also became somewhat egg-shaped. Also, the undercarriage got bent and twisted. A lot of other augers in Iowa were wrecked during that same storm so it was hard to find a used auger as a replacement. We didn't want to spend the money for a new one so we decided to repair ours.
"A friend who's in the body and fender business told us it would be easier to straighten one piece at a time, so I disassembled the auger into as many pieces as possible. It came apart in 20-ft. lengths. I fed each tube through my 30-ton capacity press 18 to 24 in. at a time in order to make the tube round again. We made a platform out of 2 by 8-in. wood with a bit of circle to help stabilize the tube and used a 2 by 4 to press down on the top of the tube.
"To remove the dents we borrowed the scissors car jack out of my wife's new Ford Taurus and mounted it on the press. We made a long flat base for the jack by welding a 15-in. length of 2-in. hollow square steel to the bottom of the jack. We capped the top of the jack with a slightly convex piece of metal.
"Because the tube was in 20-ft. lengths, we added 12 ft. to the jack's crank handle and welded 16 ft. of steel rod to the base so that we could position the jack anywhere we wanted to inside the tube in order to reduce the dents. One person needs to be at each end of the tube - one to position the jack while the other cranks the jack up. We also attached a 7 7/8-in. dia. sprocket to a length of aluminum conduit pipe. When we could insert the sprocket all the way through the tube we knew it had been restored to its original shape. We also used the press to straighten the auger's undercarriage.
"We used two loader tractors to reassemble all the parts. We tried to avoid tightening any bolts until a section was reassembled. The project took about seven days. We saved about $2,000 - not too bad for off-season work right at home."
To read the rest of this story, download this issue below or click
here to register with your account number.