1997 - Volume #21, Issue #4, Page #30
[ Sample Stories From This Issue | List of All Stories In This Issue | Print this story
| Read this issue]
They Make Their Own Grain Bins
![]() |
The bins look a little like the ends of giant-size bullets sticking out of the ground. They're 33 1/3 ft. in diameter and stand 24 ft. high at the eave and 45 ft. at the peak. They were made by welding 6 by 20-ft. sheets of 3/16-in. thick, 10 and 12 gauge steel together so they have smooth sides both inside and out. Each bin has a rung ladder on the side that leads up to a stairway and hand rail on the roof.
Each bin has an auger that's permanently mounted on the roof and powered by a 5 hp electric motor. A pair of 40-ft. long, 8-in. dia. portable augers are used to dump grain into the roof augers. Grain is unloaded by auger out the bottom of the bin.
"We saved a lot of money by building them on our own," says David, who says that he gives credit to the Lord for their abilities. "The steep 45 degree roof angle increases the bin's capacity and makes it stronger. It also eliminates the need for trusses. By filling the bin all the way to the peak we can increase capacity to 21,000 bu. while also reducing the surface area available to insects.
"We've stored wheat and milo in the bins for up to 2 1/2 years with no insect problems. Because the bins are welded together, there are no cracks for insects to crawl through and no bolts or seams to catch and hold grain like on commercial bins. Also, grain can't catch on the round access door at the bottom of the bin like it can on a conventional door frame. There are only two ways insects can get into our bins - through the blower at the bottom or the fill hole at the top. Another advantage is that the smooth sides make the bins easy to sweep out.
"We store high moisture milo in a couple of the bins. Thermal heat caused by the sun heating the roof can raise the inside temperature by 20 degrees. The aeration system we use pulls air from the top of the bin and out the bottom, which combined with the thermal heat allows the grain on top to dry first. As a result we can unload about 5,000 bu. from the top without having to wait for the entire bin to dry. We've cut milo with up to 23% moisture with no problems, although when it's that wet we fill the bin only 1/2 to 2/3 full."
The Rays used a home-built crane on a truck axle to build the bins. It tows behind the tractor and can raise a 750-lb. load 55 ft. in the air. "We put up one 6-ft. high steel ring at a time," says Martin. "We weld ears on the first ring which ends up being the top ring, then bolt trusses to them and weld the roof into place. Then we remove the trusses. After the roof is welded together, we use the hoist to raise the entire bin 6 ft. so we can install the next ring. Once the cement floor is poured it takes two men about 10 days to get the first ring up and finish building the roof. It takes about one week to weld the body of the bin together. We then install grain temperature sensors as well as the augers.
"The sides of the bins are anchored by 7/ 8-in. dia. steel rods spaced 2 ft. apart and cast in cement. The rods stick about 8 in. above the cement and are welded to the bottom ring on the bin. The cement foundation is 3 1/2 ft. deep."
The Rays unload grain from the bins into a 1,200 bu. overhead holding bin that allows semi trucks to be loaded fast. A nearby 400 bu. hopper serves as a holding bin for a grain cleaner that mounts inside a shed. Eventually they plan to add a leg system which will make it easier to load and unload the bins and will allow them to start their own wheat seed cleaning business.
They make their own augers by welding flighting that they buy from an auger manufacturer onto steel tubes, then inserting it into a pipe. They use their own lathe to make stub shafts that they weld into the ends of the auger. "We build our own augers for less than half the cost of new commercial augers," says David.
Contact: FARM SHOW Followup, David and Martin Ray, RR 2, Box 236A, Winfield, Kan. 67156 (ph 316 2
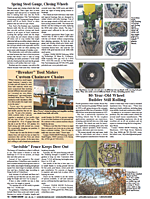
Click here to download page story appeared in.
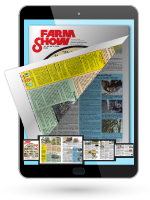
Click here to read entire issue
To read the rest of this story, download this issue below or click here to register with your account number.