You have reached your limit of 3 free stories. A story preview is shown instead.
To view more stories
(If your subscription is current,
click here to Login or Register.)
Handy Way To Handle Big Round Bales
Bruce Dalman, a Petersfield, Man., dairyman switched from square to round bales in 1981 so he could run a one-man dairy operation. He soon discovered that hauling round bales in through a 6-ft. wide side-door with a tractor and spreading the hay with a fork was for the birds. His cows eat 2 round bales a day. In winter
..........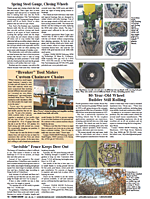
You must sign in, subscribe or renew to see the page.
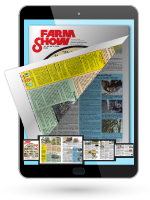
You must sign in, subscribe or renew to see the flip-book
Handy way to handle big round bales HAY & FORAGE HARVESTING Bale Handling (5) 10-5-23 Bruce Dalman, a Petersfield, Man., dairyman switched from square to round bales in 1981 so he could run a one-man dairy operation. He soon discovered that hauling round bales in through a 6-ft. wide side-door with a tractor and spreading the hay with a fork was for the birds. His cows eat 2 round bales a day. In winter, when snow piled up near the door, handling hay was a real hassle.
He figured it would speed things up if he cut the bales into pieces before he moved them into the barn. Some producers use a chain saw to slice up bales, and then carry the pieces into the barn by hand. That didn't appeal to Dalman. The hay, he reasoned, would probably plug the saw. Besides, carrying hay by hand would only add to his problems.
In the end, he settled on a system composed of a large band saw and an elevated track. Bales are cut in half outside, attached to hangers, and slid along an overhead rail into the barn. It works similar to the track system used by packing house workers to move carcasses through a meat plant.
Bales are cut, one at a time, on a 4 ft. by 6-ft. table located 30-ft. from one end of the barn. The 3¢-ft. high table has a movable ¥ in. plywood cutting platform bolted to a 3-in. x ?-in. channel iron frame. The platform's 3-in.diameter wheels sit on 12-ft. long channel iron wheel guides, which allows Dalman to move the bale through the saw.
A winch and cable system is used to pull the table and bale past the sawblade. A slot in the table accommodates the blade.
The band-saw runs on two, 14-in. diameter, steel wheels, one 11-ft. high set on a steel frame above the platform, the other below, with a smaller tension wheel set off to the side. It's powered by a 2 hp motor salvaged from an electric auger.
It takes about 2 minutes to cut an 800-pound bale in half. Each half is then fastened to a home-made bale hanger. This is a simple frame with a solid 30-in. long piece of steel on top and two 27-in. long pieces of ¢-in. rebar down the sides. Each rebar has a 2-in. square bracket on the end. To hang a half-bale, Dalman fits the hanger over the bale and works a 33-in. steel spike through the brackets and the center of the bale. The spike has a handle on one end and a hole in the point so it can be pinned in place to secure the bale.
A packing house wheel is welded to the top of the hanger. Once the bale is secured, the hanger is hoisted up with a block and tackle and the wheel set on an elevated rail supported by a wooden post and crossbeam structure in the yard. Dalman has 2 sections of rail set up in the yard where he can hang up to 20 half-bales for future use. Bales can be switched from either storage track onto the single rail that enters the barn.
Inside the barn, 16-in. long rail supports bolted to ceiling joists every 6 ft. hold up two, 400 lb. half-bales.
When Dalman wants to feed hay, he simply pushes one half-bale to the center of the barn and another just inside the door, cuts the twine and forks the hay to the nearest cows. Afterwards, the 20 lb. hangers are either pushed back into the yard or lifted off the rail and carried back.
Later this year, he plans to add another 60ft. of rail to complete the loop through the barn and back to the saw.
Dalman spent roughly $5,000 on his half-bale system, including $1,500 for the custom-made band-saw, $1,300 for the tracking and supports, and the balance on poles, motor, hangers, blade and other odds and ends. A blade will cut an average 170 bales before it fails, and costs about $160 to replace.
Story and photos reprinted with permission from Country Guide, Manitoba, Canada.
To read the rest of this story, download this issue below or click
here to register with your account number.