Bale Drying System For High Quality Hay
"My home-built dryer for small square bales saves a lot of good quality hay that might otherwise go to waste," says hay grower Stan Kokolus, Coplay, Penn., who dries up to 1,400 square bales at a time on pallets inside a shed specially designed to dry high moisture bales.
The shed, 34 ft. wide and 60 ft. long, contains two separate drying chambers with concrete walls and two 20-ft. long, 2-ft. sq. "gutters" in the floor. Hot air is blown into the gutters by a pair of old New Holland oil-fired bale dryers that are in a separate mom between the two drying chambers. Kokolus uses a 3-ton forklift to set pallets of bales onto the floor over the parallel drying gutters. Ten pallets, holding 70 bales each, are placed over the tunnels 5 deep, side by side. Once the bales are dried, he uses the forklift to stack the pallets inside a storage shed or directly onto a semi truck trailer.
"I wanted to find a way to eliminate weather damage to my crop as it dried in the field," says Kokolus, who sells his high-quality hay for a premium to horse producers. "Artificial drying of bales lets me beat the weather because I can cut hay earlier, at moisture contents up to 30%, without waiting for it to dry. The result is more leaves saved and higher quality hay. Lets me bale when no one else can.
"It takes an average of 36 hours to dry a batch of 25% moisture bales and 48 hours to dry 30% bales. One disadvantage is that by the time bales on top are dry, the bottom bales are sometimes a little too dry but that's a drawback we can live with. It costs about $20 per ton to do the drying. Each dryer burns about 5 gal. of fuel per hour and they're fitted with heat exchangers so there's no danger of an open flame igniting the bales. Heated air inside the drying chambers is recirculated back into the dryer.
Kokolus bought the dryers for about $2,000 apiece. New Holland made the dryers in the late 1950's and early 1960's as part of their "Hay in a Day" system, says Kokolus. "Hay was hand stacked on wagons, then covered by canvas. The dryer was then used to blow hot air under the canvas. The problem with this system was that it tied up wagons for several days while hay was drying, and after the hay was dry you had to unload the wagon by hand and restack the bales.
"The only time we handle bales is when we stack them onto pallets on a specially-built wagon equipped with stiff wooden sides. The stiff sides keep bales in line so they fit snug between the concrete walls of the drying chamber. Each wagon can handle two pallets. The forklift can't reach the back pallet so we bolt a home-built scissors-type hook and chain onto it and use the forklift to pull the pallet out to the front of the wagon. Using pallets really speed up hay handling. It takes only about 5 minutes to unload a wagon, One man can load a semi truck with 16 tons of hay in only 1/2 hour."
Contact: FARM SHOW Followup, Stan Kokolus, 2535 Crest St., Coplay, Penn. 18037 (ph 215 262-4501).
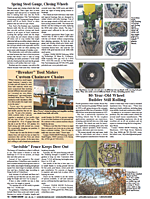
Click here to download page story appeared in.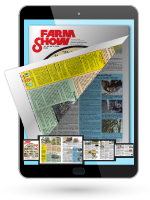
Click here to read entire issue
Bale drying system for high quality hay BALERS Balers 17-2-4 "My home-built dryer for small square bales saves a lot of good quality hay that might otherwise go to waste," says hay grower Stan Kokolus, Coplay, Penn., who dries up to 1,400 square bales at a time on pallets inside a shed specially designed to dry high moisture bales.
The shed, 34 ft. wide and 60 ft. long, contains two separate drying chambers with concrete walls and two 20-ft. long, 2-ft. sq. "gutters" in the floor. Hot air is blown into the gutters by a pair of old New Holland oil-fired bale dryers that are in a separate mom between the two drying chambers. Kokolus uses a 3-ton forklift to set pallets of bales onto the floor over the parallel drying gutters. Ten pallets, holding 70 bales each, are placed over the tunnels 5 deep, side by side. Once the bales are dried, he uses the forklift to stack the pallets inside a storage shed or directly onto a semi truck trailer.
"I wanted to find a way to eliminate weather damage to my crop as it dried in the field," says Kokolus, who sells his high-quality hay for a premium to horse producers. "Artificial drying of bales lets me beat the weather because I can cut hay earlier, at moisture contents up to 30%, without waiting for it to dry. The result is more leaves saved and higher quality hay. Lets me bale when no one else can.
"It takes an average of 36 hours to dry a batch of 25% moisture bales and 48 hours to dry 30% bales. One disadvantage is that by the time bales on top are dry, the bottom bales are sometimes a little too dry but that's a drawback we can live with. It costs about $20 per ton to do the drying. Each dryer burns about 5 gal. of fuel per hour and they're fitted with heat exchangers so there's no danger of an open flame igniting the bales. Heated air inside the drying chambers is recirculated back into the dryer.
Kokolus bought the dryers for about $2,000 apiece. New Holland made the dryers in the late 1950's and early 1960's as part of their "Hay in a Day" system, says Kokolus. "Hay was hand stacked on wagons, then covered by canvas. The dryer was then used to blow hot air under the canvas. The problem with this system was that it tied up wagons for several days while hay was drying, and after the hay was dry you had to unload the wagon by hand and restack the bales.
"The only time we handle bales is when we stack them onto pallets on a specially-built wagon equipped with stiff wooden sides. The stiff sides keep bales in line so they fit snug between the concrete walls of the drying chamber. Each wagon can handle two pallets. The forklift can't reach the back pallet so we bolt a home-built scissors-type hook and chain onto it and use the forklift to pull the pallet out to the front of the wagon. Using pallets really speed up hay handling. It takes only about 5 minutes to unload a wagon, One man can load a semi truck with 16 tons of hay in only 1/2 hour."
Contact: FARM SHOW Followup, Stan Kokolus, 2535 Crest St., Coplay, Penn. 18037 (ph 215 262-4501).
To read the rest of this story, download this issue below or click
here to register with your account number.