You have reached your limit of 3 free stories. A story preview is shown instead.
To view more stories
(If your subscription is current,
click here to Login or Register.)
School Bus Grain Truck
"Works as well as any conventional grain truck and was a lot cheaper," says Saskatchewan farmer Dave Rogers, of May-fair, who turned an old 48-passenger school bus into a 350 bu. grain truck.
Rogers started with a 1974 Chevrolet C-50 school bus equipped with a 350 cu. in. engine and 5-speed transmission. He stri
..........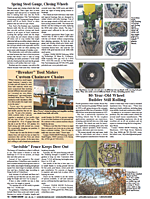
You must sign in, subscribe or renew to see the page.
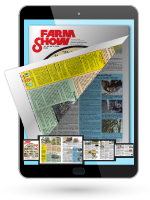
You must sign in, subscribe or renew to see the flip-book
School Bus Grain Truck GRAIN HANDLING Miscellaneous 15-5-2 "Works as well as any conventional grain truck and was a lot cheaper," says Saskatchewan farmer Dave Rogers, of May-fair, who turned an old 48-passenger school bus into a 350 bu. grain truck.
Rogers started with a 1974 Chevrolet C-50 school bus equipped with a 350 cu. in. engine and 5-speed transmission. He stripped out the seats and cut a 3-ft. wide, 7 ft. long hole in the roof. He cut three 10-in. sq. dump holes 5 ft. apart in the floor and covered them with slide chutes equipped with grab handles. He constructed a 4-ft. high retaining wall behind the driver's seat by bolting 2 by 6 planks to a pair of metal uprights. Rogers uses the bus to unload bins or to load out combines in the field.
"It does everything a regular grain truck can do and was the only grain truck hauler we owned for two years," says Rogers, who built the rig with the help of sons Frank, Jim, and Bob. "It also makes a handy fertilizer supply truck when we're seeding grain.
"We built it because we needed to save money. I was in a farming partnership for 20 years when it was suddenly dissolved. I didn't have all the machinery I needed to farm and couldn't afford to buy a truck. I paid $710 for the school bus. A used truck of comparable capacity would cost at least $8,500."
The grain box is 22 ft. long. Rogers can't fill it to the top with grain because that would put the bus over the legal road weight limit. "The legal limit in the bus for oats is 350 bu., but it can hold up to 598 bu.," says Rogers. "The windows are strong enough to support the weight of grain without any reinforcement. The sides of the bus are also strong enough to support the weight of the grain, but we run a safety chain across the bus as a precaution. Each end of the chain is bolted to a 6-in. long piece of steel that's bolted to the outside of the bus. During unloading we shovel grain out of the corners."
Two unloading holes are located in front of the rear wheels and one hole is located behind them. The auger unloads grain from one hole at a time. "We plan to speed up unloading time and eliminate the need to shovel corners by building a sloping false floor that will lead to the center hole," says Rogers, who notes that graincan be unloaded from two or three holes at a time at the elevator depending on the size of the grates over the dump pit.
The loading hole on the roof is covered by a hinged 4 by 8-ft. plywood "flip lid" that latches shut.
Contact: FARM SHOW Followup, Dave Rogers, Box 83, Mayfair, Sask. Canada SOM ISO (ph 306 246-4449).
To read the rest of this story, download this issue below or click
here to register with your account number.