1993 - Volume #17, Issue #1, Page #08
[ Sample Stories From This Issue | List of All Stories In This Issue | Print this story
| Read this issue]
Bunk Feeder Built From Manure Spreader
![]() |
![]() |
The spreader rides on top of a steel track over a 100-ft. long bunk. A 1 1/2-hp electric motor mounted on back of the spreader is used to power the apron and beaters and to drive the spreader back and forth on the track. The operator stands on a wooden platform mounted on the front end of the spreader.
"We built it 22 years ago for $500 and it still works great," says Klug, who built the feeder with the help of Ezra Schauer. He who uses it to feed a mixture of silage and grain to 70 Holstein feeders. "We had been pushing silage down the feed bunk with shovels and garden carts which was a half hour job. We looked at automated bunk feeders but they cost too much. Also, our feed bunk is out in the open where feeder mechanisms could freeze up and we didn't want to have to spend a lot of time repairing it.
"The spreader is loaded inside a shed between two concrete stave silos. One silo holds silage and the other holds grain. The apron and beaters mix silage so well that every animal gets virtually the same proportion of grain and silage. The spreader holds about 1,000 lbs. of feed."
Klug replaced the original spreader wheels with 14-in. dia. car wheel rims, then mounted a large sprocket on one of the rims. The rear-mounted 11/2 hp electric motor belt-drives a jackshaft that chain-drives the sprocket. An electric cord rides along a wire suspended from the shed to a telephone pole near the end of the bunk. The wire supports the cord as it unfolds from a steel post welded onto the back of the spreader.
Klug flips a switch to start the motor, then uses a lever on the left side of the operator platform to disengage an idler, allowing the spreader to go forward. He uses a lever on the right side of the plat-form to engage the apron. When he reaches the end of the bunk he reverses the motor to reverse direction of the drive wheel and beaters (a slip clutch prevents the apron from running backward).
Klug replaced the spreader's rotted-out floor with a new plywood floor. He also used sections of plywood to close up the back of the spreader to keep wind from blowing feed away.
To make the track he mounted 3-in. dia. steel pipes, spaced 5 ft. apart, on top of the bunk and used lengths of channel iron to brace them every 6 ft.
Contact FARM SHOW Followup, John Klug, Rt. 2, Box 298, Waseca, Minn. 56093 (ph 507 835-2129).
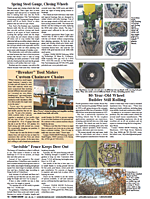
Click here to download page story appeared in.
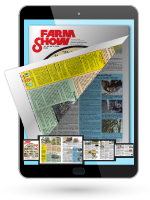
Click here to read entire issue
To read the rest of this story, download this issue below or click here to register with your account number.