2022 - Volume #46, Issue #5, Page #39
[ Sample Stories From This Issue | List of All Stories In This Issue | Print this story
| Read this issue]
“Made-It-Myself” Field Aerator
![]() |
“One neighbor had a hay field that was seeded in 1994, and when a government assessor looked at it, he said it looked like a 4-year-old stand,” recalls Erdman. “Another said fields where he aerated grew hay twice the height of unaerated fields, and the soil was alive with earthworms and other bugs.”
Even with testimony like that, Erdman couldn’t justify the $45,000 price tag of a commercial unit. A long-time journeyman welder with experience in heavy equipment, he had access to low-cost, high-quality steel.
“I’ve had contracts to go in and clean up an oil lease, and all they wanted was to get rid of the steel,” he says.
Erdman went to work on a 12 1/2-ft. long, 4-ft. dia., 1 1/4-in. thick pipe. For the cutting surfaces, he used worn-out Caterpillar track pads.
To make the cutting plates, he cut a template out of tin for use with a plasma cutter. He cut the leading edge that has the grouser bar off the pad and set it aside. The rear edge of the pad has a 1-in. slant that he mounted pointing away from the pipe.
“The cutting plates are 7 in. wide with the angled edge 6 in. high on one side and 5 in. high on the other,” says Erdman. “They cut into the ground like a knife.”
He used 11018 welding rod designed for high tensile strength joints to weld the hardened and wear-resistant steel to the mild steel pipe. “I expect the track pads are around 100,000 tensile strength,” says Erdman.
He welded 1-in. steel plate ends to the pipe to make the aerator drum, reinforcing them with four 1-in. by 4-in. steel bars from the rim to the spindle. He centered a 3-in. steel pipe in the drum for an axle.
Erdman built the frame for the aerator drum out of 3 by 6-in. heavy wall steel tubing and 6-in. steel pipe. To mount the drum axle on the frame, he first mounted oil-impregnated brass bushings on it.
“A lot of guys use bearings, but I didn’t know what kind of impact the aerator might have to take,” says Erdman. “The bushings are like the ones used on rail cars.”
Erdman machined a steel shaft into a spindle to fit the bushing and fit the 3-in. pipe. He welded it into place in the pipe to secure the drum to the frame.
For transit purposes, Erdman added an axle off a tandem high-boy. A set of hydraulic cylinders pull the axle in to lift the aerator drum. If he plans to pull it behind a Cat to knock down brush or trees, he can pull two pins and detach the hoist assembly, hoses, and wheels. That allows him to back the aerator up without damaging the wheels.
The aerator weighs in at around 14,000 lbs. Erdman estimates it could hold an additional 12,000 lbs. of water.
“I over-engineered it, building it really strong,” says Erdman. “In a couple of hundred years, it’ll still be in use.”
If it is, his fields should be in extremely good shape. “While the drought hasn’t been as bad as last year, it’s been very dry,” says Erdman. “On a field with a 30-year-old grass mix, I’m seeing alfalfa for the first time in 20 years. I believe if you can keep your soil alive, it’s a win-win situation.”
Contact: FARM SHOW Followup, Dan Erdman, Box 1620, Claresholm, Alta. Canada T0L 0T0 (ph 403-382-1020; derdman2@telusplanet.net).
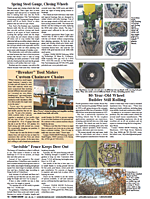
Click here to download page story appeared in.
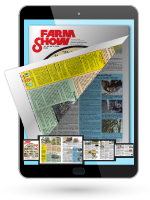
Click here to read entire issue