2022 - Volume #46, Issue #2, Page #18
[ Sample Stories From This Issue | List of All Stories In This Issue | Print this story
| Read this issue]
Reverse Rollers Leave Concrete Smooth
![]() |
“I had seen commercial rollers, but none that worked the way I wanted,” says Vandeventer. “Some are powered by a hydraulic pump on a stationary engine off to the side. I didn’t want to deal with possible hydraulic oil spills on fresh concrete.”
A 3 hp. Briggs & Stratton engine with 10 to 1 gear reduction provides the spin. It works with nine different roller lengths and two frames. The frames were fabricated mostly from 1 by 1-in. steel tubing. The rollers were a lucky find.
“The first roller I used was a piece of irrigation tubing, but it was too light,” says Vandeventer. “It would float up and required a second person to push down on the other end, even on a narrow job.”
During a visit to a local salvage yard, he ran across 4 1/2-in. dia., 1/4-in. wall, aluminum alloy pipe. It was left over from the construction of a nuclear power plant.
“I took a piece home and tried it,” says Vandeventer. “It was ideal. I went back and bought all they had, in lengths from 10 to 22 1/2 ft.”
The frames include a wheeled unit pulled by a worker with the roller to one side. The frame supports the motor and a winch and anchors one end of a roller.
The wheels are height adjustable, so it can run on a form or alongside as needed. The throttle control and clutches for the roller and the winch are mounted to the handlebar.
On narrower pours, the operator pulls it down grade or down the slab against the spin of the roller. If a second trip is needed, the operator revs the motor, and the roller pulls itself back up the slab.
For wider jobs, a winch and a system of anchored pulleys pull the roller forward, pushing the concrete ahead. The Briggs & Stratton powers the winch and the roller simultaneously, but with separate clutches and at different speeds, thanks to different size pulleys on the jackshaft.
“The output shaft on the motor has a 1 1/2-in. pulley that drives a 6 or 7-in. pulley on a jackshaft,” explains Vandeventer. “A roller chain from a 2-in. sprocket on the right side of the jackshaft drives a 3 1/2-in. sprocket on the pipe drive, giving it a 10 to 1 gear reduction. There’s a 1 1/2-in. pulley on the jackshaft and a 7-in. pulley on the winch to gear it down even further.”
The pipe drive is a steel core with two raised cogs. The roller pipes are notched to match the cogs that hold them in place. Switching rollers is a simple matter of sliding one off and the other on.
When he uses the winch, Vandeventer sets a ground anchor to the left side of the end of the concrete slab. Pulleys are anchored at the start of the slab and to either corner at the end of the slab.
“We make one short pass of about 4 ft. with the winch pulling the roller, release the winch clutch and rev the motor,” says Vandeventer. “The roller pulls itself back to the start. The first pass strikes the concrete down, but on a wider slab, we often need to go back and forth.”
Contact: FARM SHOW Followup, Kenneth Vandeventer, 3139 Indiana Rd., Ottawa, Kan. 66067 (ph 785-241-0613; kennethvandeventer@gmail.com).
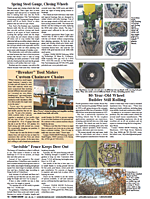
Click here to download page story appeared in.
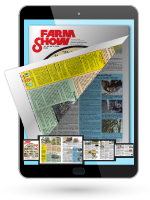
Click here to read entire issue